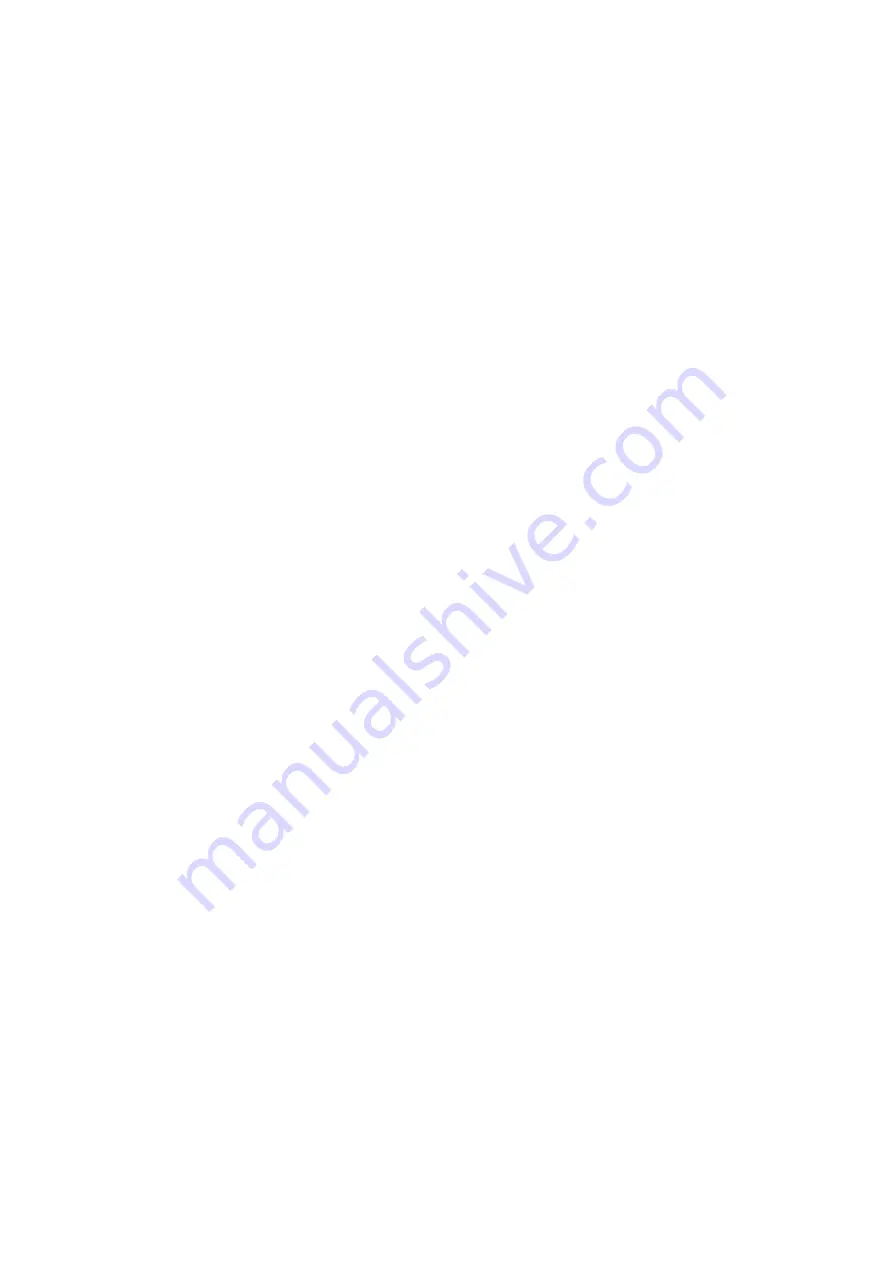
9
5.1.3.3 Welding type handle Spool Gun (optional)
Terminal current holder should be connected to MIG (1). Plug polarization changes (4) in the socket (3). The negative pole of the source (5) connected to
the work piece by means of a wire with a clamp. Plug the device into a power outlet 230V 50Hz. The switch (11) located inside the tray switch position
Spool Gun.
5.2 Connection shielding gas
1. Attach the bottle and secure it against tipping.
2. Remove the cylinder valve briefly to remove any impurities.
3. Install the regulator on the cylinder.
4. Connect the hose with a discharge gas regulator (8) to the rear of the welder.
5. Remove the cylinder valve and regulator.
5.3 Connection to the mains
5.3 Connection to the mains
1. A device to be used only in a single-phase, three-wire, with earthed neutral.
2. Rectifier Inverter 200 DIGIMIG PULSE is adapted to cooperate with the network 230V50 Hz fused 25 A time-delayed action. Power supply
should be stable, with no voltage drops.
3. The device is equipped with a power cord and a plug. Before connecting, make sure the power switch (6) is in the OFF position (off).
5.4 Inserting the spool of wire electrode
1. Open the side housing cover.
2. Check that the drive rollers are suitable for the wire size and type. If necessary, set up a proper roll. For steel wire, use of rollers with V-shaped
grooves, and the aluminum wire with the groove in the U-shaped
3. Place the spool of wire electrode on the stem.
4. Secure the spool from falling.
5. Release the pressure feed rollers.
6. blunt end of the electrode wire.
7. Enter the wire by the driving roller tray holder.
8. Press the wire in the groove of the drive roller.
9. Remove from the handle end of the current, to power equipment and pull wire holder welder using speed wire feeding.
10. When you see the wire in the outlet handle release button and screw the current.
11. Adjust the pressure force by the feed roller rotation of the platen knob. Too little contact force will result in slipping of the drive roller, too much
pressing force, will increase the resistance of administration, which may lead to deformation and damage to the wire feeder.
5.5 Preparation of MIG to work
Depending on the type of material being welded and the filler wire diameter assumed the MIG current, and one end of the input wire guide.
For steel welding tips used for welding current and the contribution of steel. In the case of aluminum welding tip current used to weld aluminum and the
input of Teflon.
5.5.1 Quick extension wire
The device has the function of high-speed wire feeding. Pressing the button (B) causes a rapid extension wire for easy putting it into the holder.