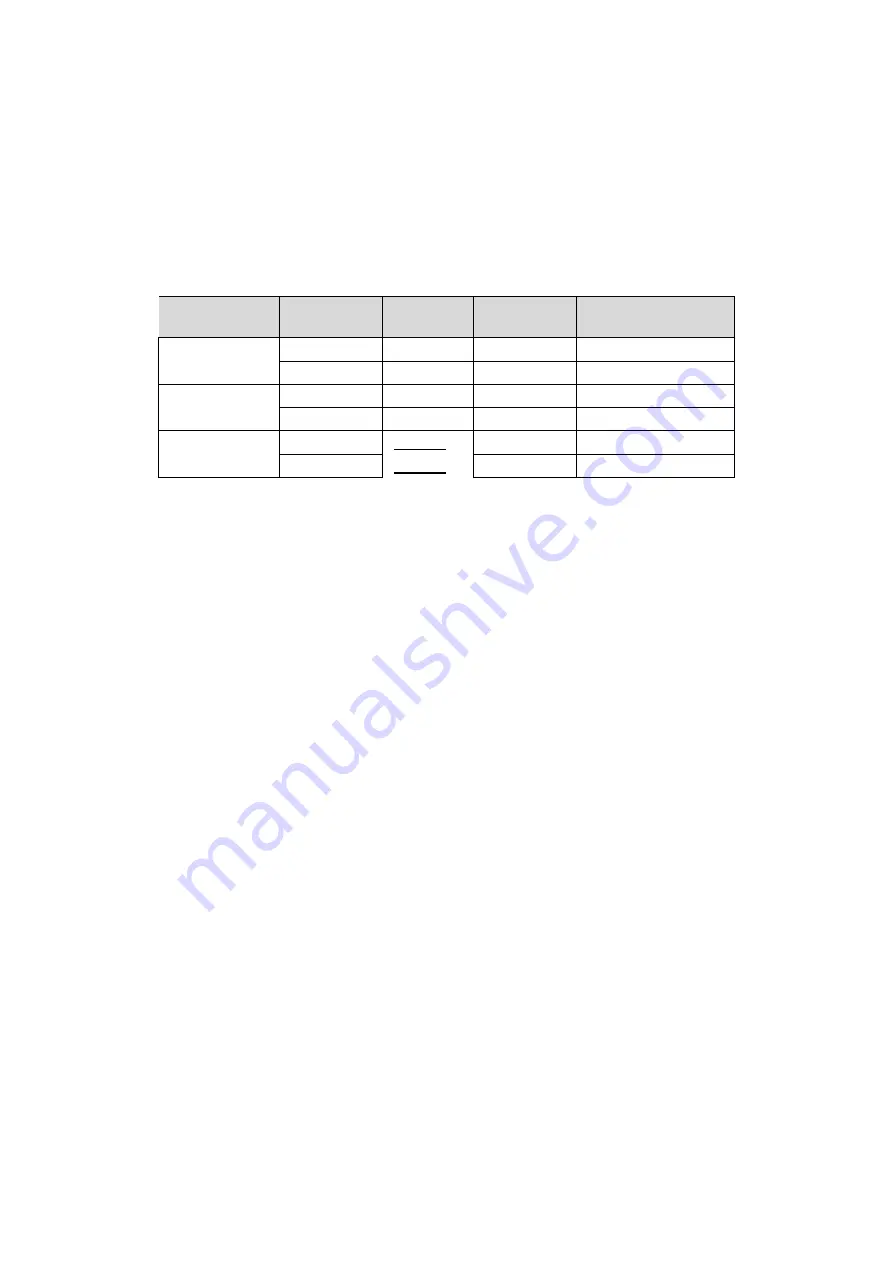
twenty
pulse width
The pulse width is a pulse duration, allows you to adjust the depth of penetration. The increase in width increase the depth of penetration,
reduction reduces the amount of heat entering the material, reducing the risk of burnout of thinner plates and smaller components.
Lower values of the pulse width must be used for higher currents. The greater the pulse width must be applied to small currents, a width of more than
50% should be used for currents lower than 100A.
Welding machine has a built-in synergic programs for selected materials, wire diameters and shielding gases in accordance with the following table:
Material
designation Species
wire
diameter
Shielding gas -
recommended
Mild steel
Fe Co2
0.8 / 1.0
WHAT
2
WHAT
2
Fe Mix
0.8 / 1.0
Ar + CO
2 (
82/18)
Ar + CO
2 (
82/18)
Ar + CO
2 (
82/18)
Aluminum
AlMg5
ER5356
1.0 / 1.2
Argon
AlSi5
ER4043
1.0 / 1.2
Argon
stainless steel
E308
ER308LSi
0.8 / 1.0
Ar + CO
2 (
98/2)
Ar + CO
2 (
98/2)
Ar + CO
2 (
98/2)
E316
ER316LSi
0.8 / 1.0
Ar + CO
2 (
98/2)
Ar + CO
2 (
98/2)
Ar + CO
2 (
98/2)
•
Argon should be used with high-class quality: 4.8 and above recommended
In addition, depending on the operating conditions can be set inductance value, which affects the shape of the weld, the depth of penetration and the
In addition, depending on the operating conditions can be set inductance value, which affects the shape of the weld, the depth of penetration and the
amount of weld spatter
.
It should take into account the fact that the welding parameters recommended in synergy mode on conventional
amount of weld spatter
.
It should take into account the fact that the welding parameters recommended in synergy mode on conventional
amount of weld spatter
.
It should take into account the fact that the welding parameters recommended in synergy mode on conventional
welding materials from the selected group and the recommended shielding gases. When welding materials of various parameters of the alloy
may not be optimal and require adjustment settings. For this reason, the synergistic mode should not be regarded as a universal parameter
proposal, but as a starting point for the fine adjustment of settings.
Manual SPL function MIG or manual selection of parameters is particularly useful for braze welding. Using the three welding parameters must be set
optimal set capable of producing a proper weld. When selecting parameters to be selected low and high voltage wire feed speed. It is recommended to
use argon as a shielding gas, but good results can also use a mixture of argon with CO
2 (
82/18). Due to the required shape of the weld inductance
use argon as a shielding gas, but good results can also use a mixture of argon with CO
2 (
82/18). Due to the required shape of the weld inductance
use argon as a shielding gas, but good results can also use a mixture of argon with CO
2 (
82/18). Due to the required shape of the weld inductance
should be selected empirically depending on the thickness and type of material being welded. As additional material is most commonly used
copper-based binder. These wires are labeled CuSi3 or SG -CuAl.
It is recommended to use the handle of not more than 3 m with a pad equipped with Teflon.
8. WELDING ALUMINUM ALLOY
In synergy mode, you can select one of two programs for aluminum welding. The programs were selected for welding wire ALSi5 type ER 4043, primarily
intended for aluminum casting and wire AlMg5 type ER 5356, which is suitable for welding all types of constructions and profiles. Welding aluminum is
not a simple function, the welder requires experience, knowledge and behavior of certain practices that will facilitate the welds on aluminum elements.
Device in a synergistic adjusts the output of the corresponding grade materials and types of wires. Depending on your needs, make the appropriate
adjustment of the voltage and the inductance to get the desired effect.
It should first of all remember a few important things that greatly affect the appearance of the joint and affect the correct welding process.
Before starting work on the welding of aluminum components, follow these steps:
Device:
•
Ensure that the feed rollers are designed to work with aluminum groove is shaped like the letter "U" and are dedicated to the appropriate
diameter of the welding wire. Using the wrong rollers will cause deformation of the wire and the problems in the welding process.