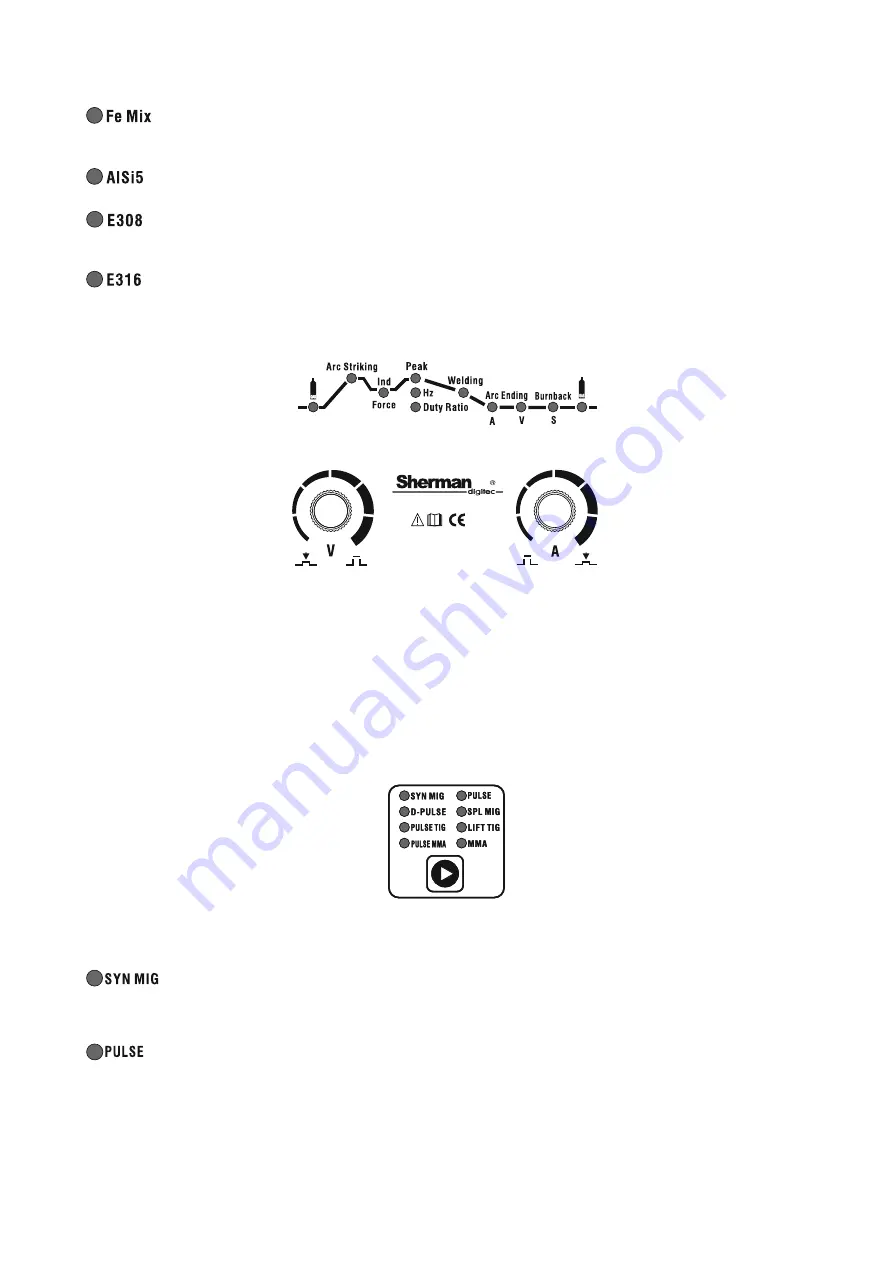
15
-
welding of carbon steel in the shell mixture of Ar / CO
2.
Recommended mixing ratio of 82% Ar
welding of carbon steel in the shell mixture of Ar / CO
2.
Recommended mixing ratio of 82% Ar
welding of carbon steel in the shell mixture of Ar / CO
2.
Recommended mixing ratio of 82% Ar
18% CO
2.
18% CO
2.
- welding of aluminum alloys, silicon and argon.
- Welding of stainless steel to cover mixtures of Ar / CO
2.
Recommended mixing ratio to 98%
Welding of stainless steel to cover mixtures of Ar / CO
2.
Recommended mixing ratio to 98%
Welding of stainless steel to cover mixtures of Ar / CO
2.
Recommended mixing ratio to 98%
Ar 2% CO
2.
Ar 2% CO
2.
- Welding of stainless steel to cover mixtures of Ar / CO
2.
Recommended mixing ratio is 98% Ar 2% CO
2.
Welding of stainless steel to cover mixtures of Ar / CO
2.
Recommended mixing ratio is 98% Ar 2% CO
2.
Welding of stainless steel to cover mixtures of Ar / CO
2.
Recommended mixing ratio is 98% Ar 2% CO
2.
Welding of stainless steel to cover mixtures of Ar / CO
2.
Recommended mixing ratio is 98% Ar 2% CO
2.
L, P - knob / control buttons and chart parameters
DIGIMIG 200 PULSE
PARAMETERS
CHOICE
MODE
CHOICE
Knobs (L lh) and (T-right) are used to control the welding parameters. Rotate the knobs to the left to decrease, and turning to the right to increase the
parameter value. Pressing the knob (P) will save the currently settable parameter and moves to the next parameter or group of parameters. Currently set
parameter or parameter group is indicated by illumination of the corresponding LED on the chart parameters. In the case of a group of parameters
pressing (L) switches between the individual parameters in the group. Knob (P) is regulated most parameters, the knob (L) may be carried out only
welding current during the welding or MIG SPL offset voltage during MIG settings utilizing a synergistic effect.
H - welding method selection button
The button is used to select the welding method. Selecting the appropriate mode is confirmed by lighting of the LED.
- MIG / MAG welding using settings synergistic. The unit sets
welding parameters depending on the type and thickness of material. These parameters can be changed by the user.
- MIG / MAG pulse. This is an advanced form of welding using
the best form of transfer of molten material in the welded wire electrode material. Significantly reduces the formation of chips and permits welding in all
positions. Lower heat input eliminates burn thin materials. This method uses a synergistic settings.