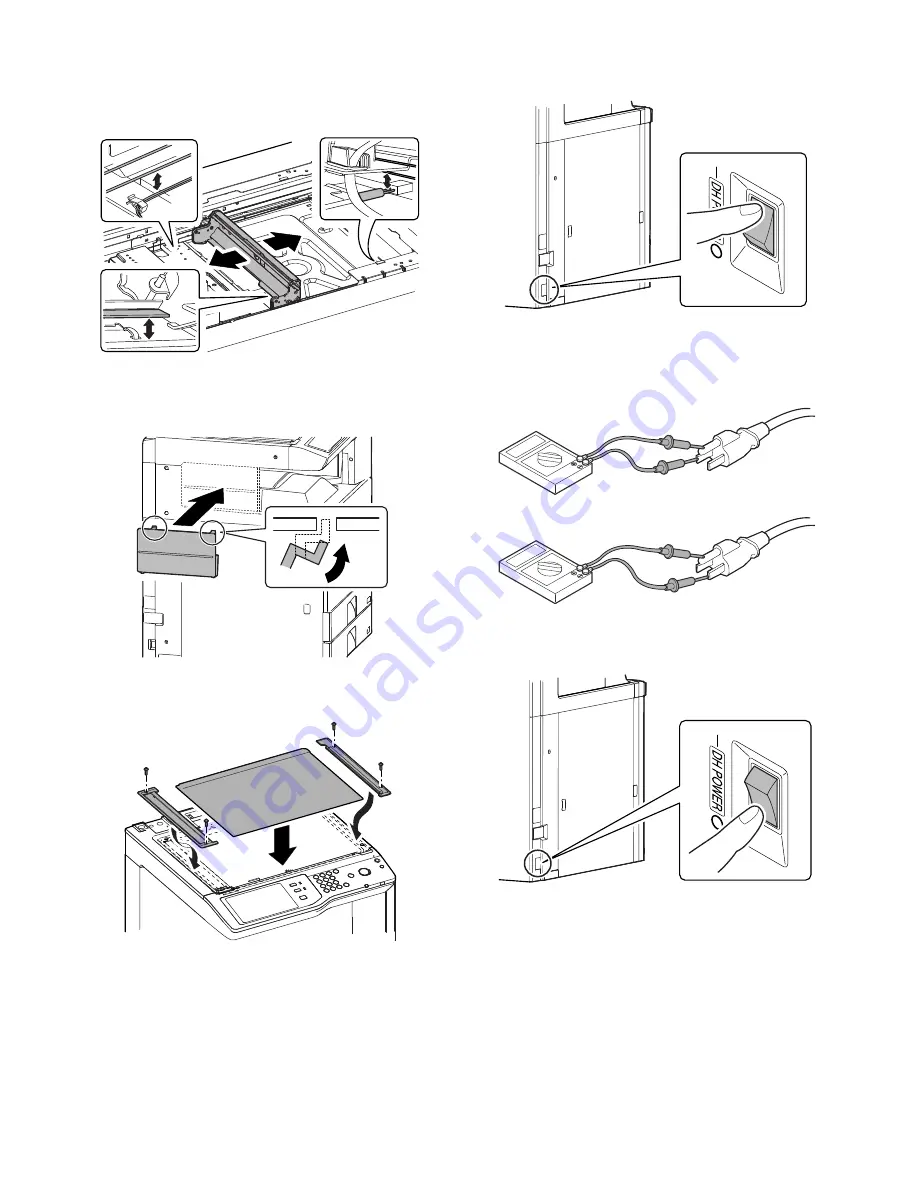
MX-M503N Dehumidifying heater 27 – 6
6)
Move the lamp unit by hand and check that it move smoothly in
all movable area.
NOTE: Check that there is no interference of the harness of the
scanner heater in the wire and the 2/3 mirror unit.
(4) Installation of the table glass, the paper exit cover
1)
Install the paper exit cover.
2)
Install the table glass. Install the SPF glass and the glass
holder, and secure it with the screw.
F. Operation check after installation
1)
Turn on the dehumidifier heater switch.
2)
Measure the resistance value between the earth terminal and
the AC terminal (L side), and between the earth terminal and
AC terminal (N side) with the circuit tester, and confirm they
are not short-circuited.
3)
When not using the heater after checking, turn off the dehu-
midifier heater switch.