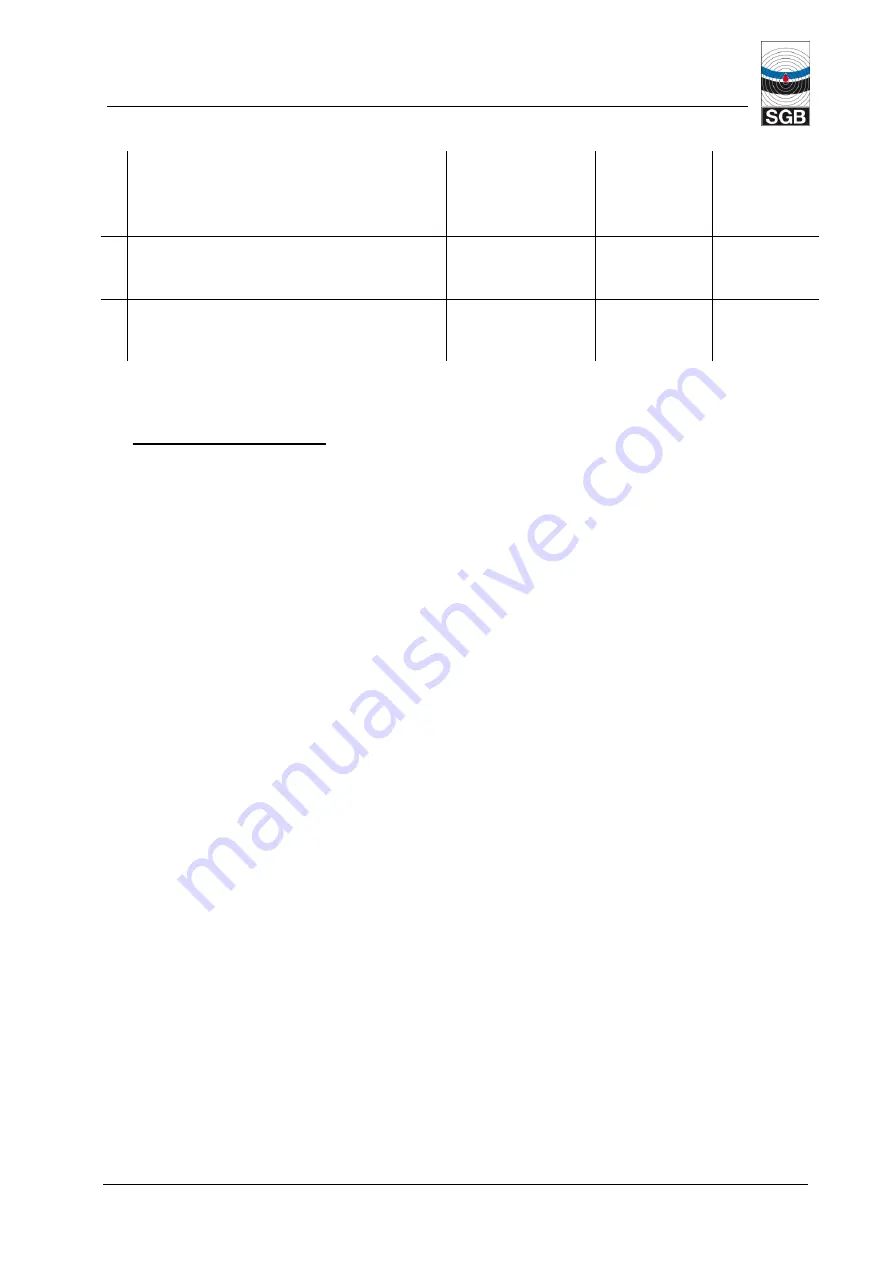
VACUUM LEAK DETECTOR VLR ..
2020-06-29
3
2.4. Double-walled pipes (up to 5 bar or up to 25 bar)
G
roup
Type of pipe
Installation ex-
ample
Suitable leak
detector type
Use limits
P
Double-walled pipes made in the factory
or on site with up to 5 bar pressure in the
primary pipe (conveying pressure)
P
– 01
to
P
– 03
VLR 230
to
VLR 570
Appendix E,
No. E.1
Q
Double-walled pipes made in the factory
or on site with up to 25 bar pressure in the
primary pipe (conveying pressure)
Only
with
solenoid
valve(s): Q
– 01 to
Q
– 04
VLR 230/E
to
VLR 570/E
Appendix E,
No. E.1
3. Functional description
3.1. Normal operation
The vacuum leak detector is connected to the interstitial space via the suction and measuring
line, possibly also via the connection line(s). The vacuum generated by the pump is measured
and controlled by a pressure sensor.
When the operating vacuum (pump OFF) has been reached, the pump is switched off. Due to
slight, unavoidable leaks in the leak detection system, the vacuum begins to fall slowly. When
the switching value for “pump ON” has been reached, the pump is switched on and the intersti-
tial space evacuated until the operating vacuum (pump OFF) has been reached again.
During normal operation the vacuum moves between the switching value pump OFF and the
switching value pump ON, with the pump running for a short time and then switching off for a
longer time, depending on the tightness and temperature fluctuations in the complete system.
3.2. Air leak
If an air leak occurs (in the outer or inner wall, above the liquid level) the vacuum pump switch-
es on in order to re-establish the operating pressure. If the air flow leaking into the pipe exceeds
the limited feed flow of the pump, the pump remains on continuously.
Increasing leak rates lead to a further increase in pressure until the switching value for alarm
ON has been reached. An optical and audible alarm signal is triggered. If solenoid valves are
closed, the pump stops.
3.3. Liquid leak
In the case of a liquid leak, liquid enters the interstitial space and collects at the lowest point of
the interstitial space.
The incomming liquid leads to the vacuum dropping, the pump is switched on and evacuates
the interstitial space(s) until operating pressure has been reached. This process is repeated
until the liquid stop valve in the suction line closes.
Due to the vacuum still present in the measuring line, further leak liquid is sucked into the inter-
stitial space, the measuring pipe and into a pressure compensating vessel if appropriate. This
leads to reduction of the vacuum until the pressure has reached the “alarm ON” level. The opti-
Summary of Contents for VLR 230
Page 19: ...I I II II III III IV IV 21 21 21 21 20 20 20 20 27 11 2002 P 060 000...
Page 27: ...21 02 2017 SL 853 600 2 6 4 5 3 11 12 1 AC DC 105 106 102 71 01 69 24 1 24 3 59 09 76 17 60 Rp...
Page 29: ...22 84 85 85 22 52 98 98 0 Kl 1 0 17 12 2002 P 115 392 21 21 20 20 90 90...
Page 39: ...28 06 2005 D i hrbild Abmes 200 3 0 0 2 6 0 220 T 140 8 Dimension Drilling...