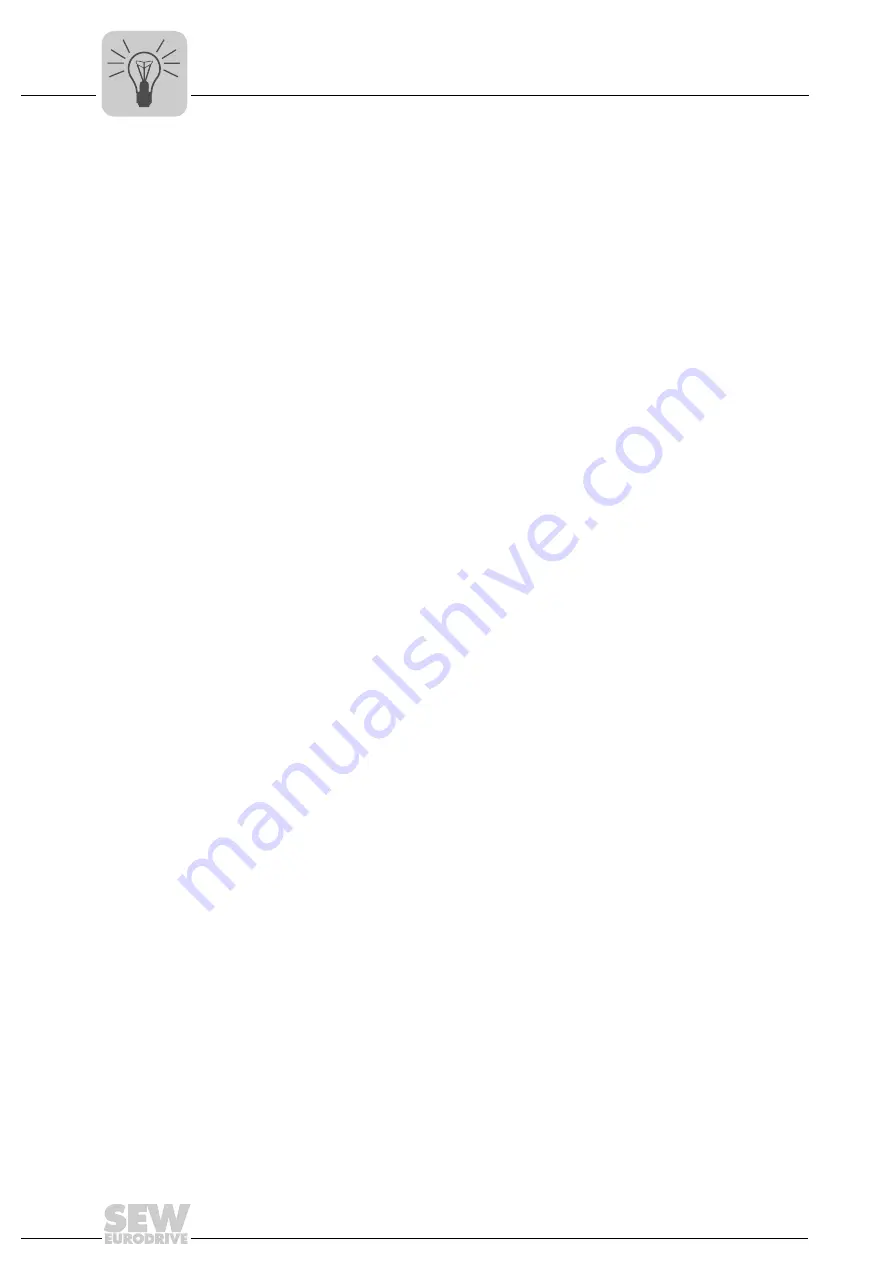
80
Manual – MOVI-PLC® advanced DHR41B for EtherNet/IP, Modbus/TCP and PROFINET IO
9
Diagnostic sequence
Fault Diagnostics for Operation on EtherNet/IP and Modbus/TCP
Step 2: Check the status LED and the status display on the master (scanner)
To do so, use the documentation of the controller or master module.
Should there be no working EtherNet/IP or Modbus/TCP master yet, you can use an
SEW master simulator for testing or starting up the DHR41B option. The latest version
of the master simulator is available on the SEW website.
You can use the SEW master simulator to exchange process or parameter data with
EtherNet/IP or Modbus/TCP profile with an SEW fieldbus interface.
Step 3: Fault diagnostics
If DHR41B is in the 'Connected' status, data exchange between master (scanner) and
slave is active. If the data is not transferred to the IEC application of MOVI-PLC
®
ad-
vanced
DHR41B via EtherNet/IP or Modbus/TCP correctly, the following steps will as-
sist you in finding the cause for the problem.
A Are the correct values for the process data words displayed in the PLC Editor?
If yes, continue with F.
B Is the process data exchange activated in the scanner (master)?
C Is the process data written to the correct location in the scanner? Check the tags and
scanner mapping.
D Is the PLC in RUN mode or does active forcing overwrite the transfer of the normal
process data words?
E If the PLC is not sending data to the DHR41B, please refer to the documentation of
the PLC manufacturer for support.
F Are the process data words being used correctly in the IEC program?
G Which status is displayed in the IEC application for the communication interface via
the
FBusGetInfo
module (see chapter "Settings in MOVI-PLC
®
advanced
DHR41B")?
Summary of Contents for DHR41B
Page 2: ...SEW EURODRIVE Driving the world ...
Page 129: ...SEW EURODRIVE Driving the world ...