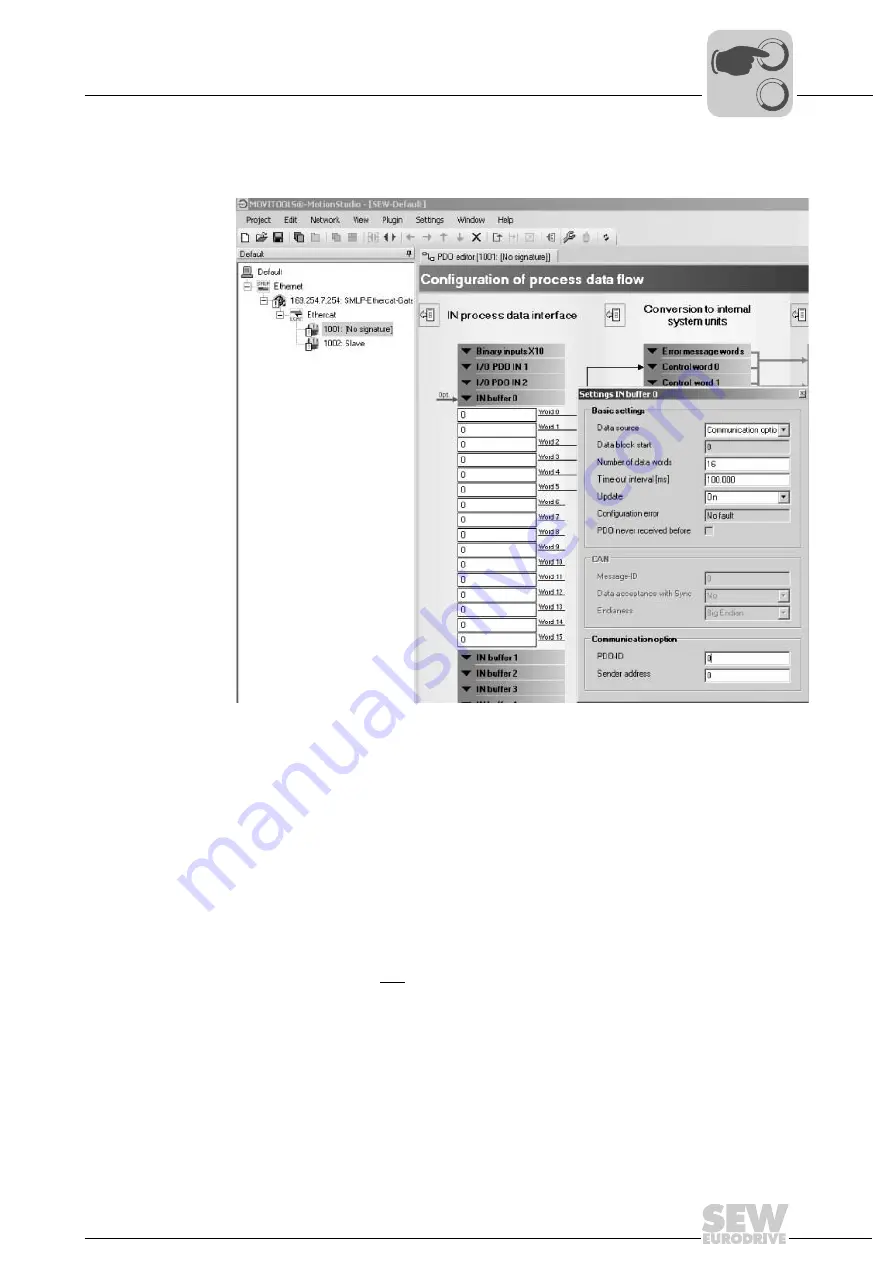
Manual – XFE24A EtherCAT Fieldbus Interface
23
5
Settings on the MOVIAXIS® servo inverter using the example of single-axis
EtherCAT Configuration and Startup
Manual settings
Manual setting of the communication and PDO configurations:
• Start the PDO Editor.
• For operation with an EtherCAT bus system, a free "IN buffer" (e.g. IN buffer 0) must
be configured:
• Number of data words:
16
for firmware status 21
1 ... 16
for firmware status 22 and higher
EtherCAT with MOVIAXIS
®
always transfers 16 data words.
"Number of data words" determines how many data words are used of the 16 that
are transferred.
• Time-out interval
Here, you can set the monitoring time for the "IN buffer". If the process data commu-
nication exceeds the set time, error message 67 "Error PDO timeout" is issued.
Setting range 0 ... 100....100000 ms (0 ms corresponds to deactivated, standard is
100 ms).
• Update:
On
Updating the process data.
11658AXX
Figure 8: Manual settings
0
0
I
Summary of Contents for 1821 2492
Page 2: ...SEW EURODRIVE Driving the world...
Page 66: ......