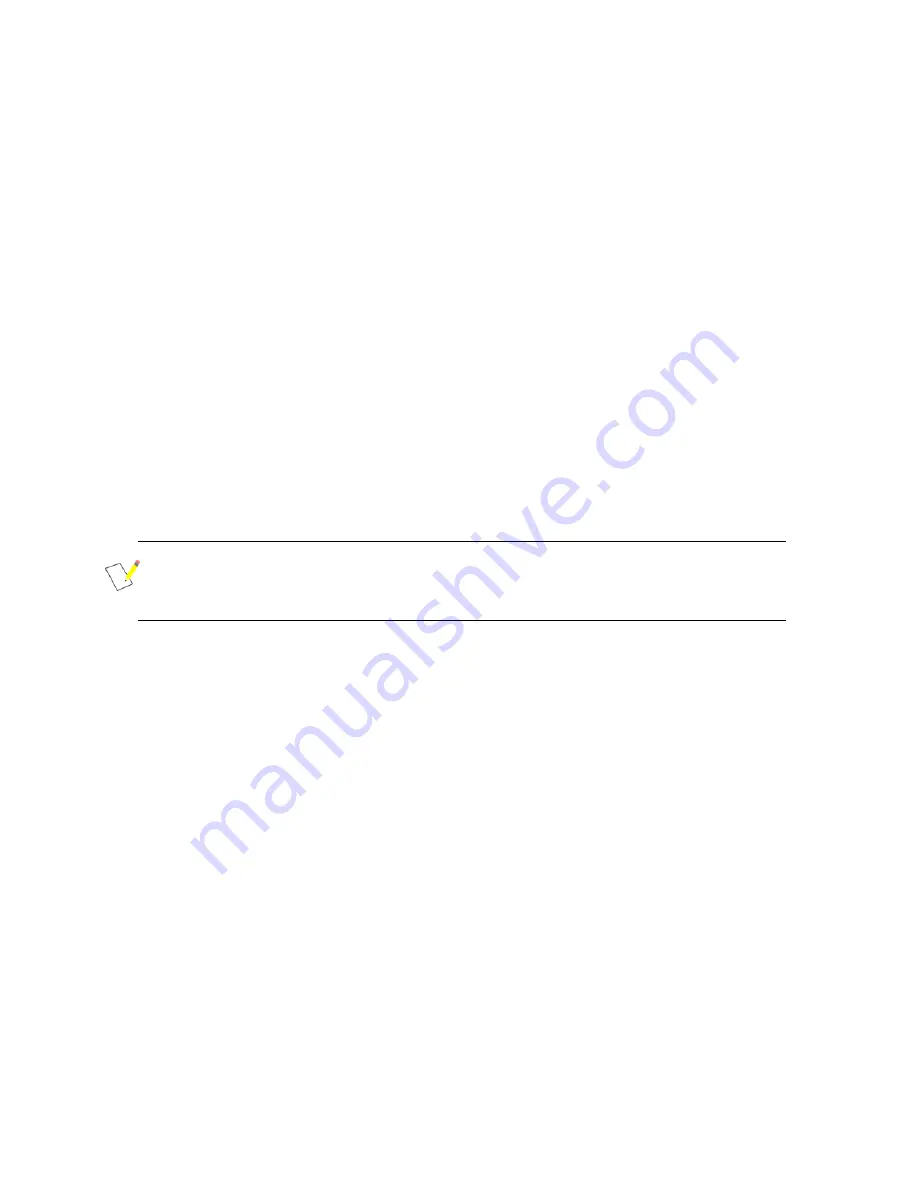
About the Gen4
Doc. # 177/52701
Rev. 3.3
2-5
Principles of operation
Functional description
The main function of Gen4 is to control the power to 3-phase squirrel-cage AC induction or
PMAC motors in electric vehicles. Four-quadrant control of motor torque and speed (driving and
braking torque in the forward and reverse directions) is allowed without the need for directional
contactors. Regenerative braking is used to recover kinetic energy which is converted into
electrical energy for storage in the battery.
In a traction application control commands are made by the driver using a combination of digital
controls (direction, foot switch, seat switch, etc.) and analogue controls (throttle and foot brake).
The controller provides all the functions necessary to validate the driver’s commands and to
profile the demand for speed and torque according to stored parameters.
Throttle inputs can be configured as speed or torque demands with throttle-dependent speed
limits: in either case, a torque demand is continually calculated to take account of pre-set limits
on the level and rate-of-change of torque. The torque demand is used to calculate current
demands; that is, the controller calculates what currents will be required within the motor to
generate the required torque.
There are two distinct components of the current, known as the d-q axis currents, which control
current flow in the motor. The d-axis current is responsible for producing magnetic flux, but does
not by itself produce torque. The q-axis current represents the torque-producing current.
NOTE: When a vehicle is ready to drive, but no torque is being demanded by the driver, the
d-axis or magnetizing current will be present in the motor so that the vehicle will respond
immediately to a torque demand. To save energy the magnetizing current is removed if the
vehicle is stationary and no torque has been demanded after a set period.
Measured phase currents and current demands i
d
and i
q
, the d-q axis currents, are used as part
of a closed-loop control system to calculate the necessary voltage demands for each phase of
the motor. Voltage demands are then turned into PWM demands for each phase using the
Space Vector Modulation (SVM) technique. SVM ensures optimum use of the power
semiconductors.
Power conversion section
The power conversion section of Gen4 employs a 6-switch MOSFET bridge operating at an
effective frequency of either 16 kHz or 24kHz ( equates to a PWM switching frequency of 8kHz
or 12kHz and is set via object 5830
h
). Excellent electrical and thermal efficiency is achieved by:
Minimization of thermal resistances.
Use of the latest MOSFET technology
Internal thermal protection (if temperatures are excessive, output torque is reduced).
Overcurrent protection using device characteristics.
Internal measurement of output current.
Overvoltage trip in the event of regenerative braking raising battery voltage to unsafe levels.
Summary of Contents for Gen4
Page 1: ...Gen4 Applications Reference Manual Document no 177 52701 Rev 3 3 ...
Page 9: ...Chapter 1 Introduction ...
Page 13: ...Chapter 2 About the Gen4 ...
Page 25: ...Chapter 3 Installation ...
Page 45: ...Chapter 4 Specification ...
Page 53: ...Specification Doc 177 52701 Rev 3 3 4 9 Dimensions Size 2 models Size 4 models ...
Page 54: ...4 10 Size 6 models ...
Page 55: ...Chapter 5 System design ...
Page 60: ...5 6 Single traction wiring diagram Figure 13 Single traction wiring diagram ...
Page 63: ...System design Doc 177 52701 Rev 3 3 5 9 On board fuse See On board fuse mounting on page 3 11 ...
Page 64: ...5 10 Figure 15 Dual traction wiring diagram ...
Page 70: ......
Page 71: ...Chapter 6 Configuration ...
Page 110: ......
Page 111: ...Chapter 7 Monitoring Gen4 ...
Page 122: ......