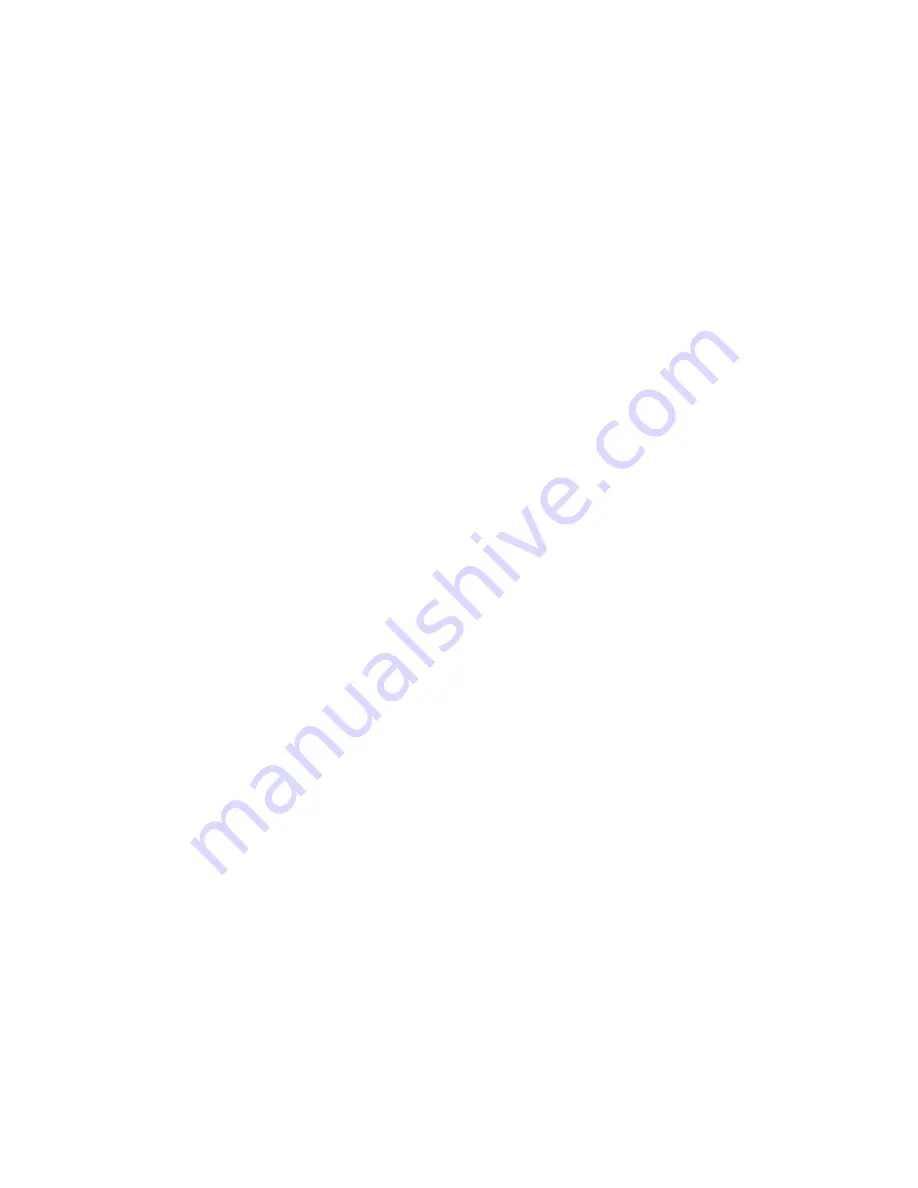
Doc. # 177/52701
Rev3
6-32
General Setup
Configure the pump features at 2A00
h
:
Inhibit pump when BDI drops below cut-out level. If already operating when the cut-out
occurs, the pump will continue to operate until all pump inputs are inactive.
Drive Enable switch and/or Seat switch input disables pump.
Ignore Line Contactor state. Allows the pump to operate if it is not connected to the battery
through the line contactor. Should be set if the pump also supplies power steering and the
power steer is required to operate when the line contactor is open.
Use Power Steer target velocity as pump input, if pump also supplies power steering.
Enable minimum pump speed. Enable this to force the pump to run at minimum speed
(2A01
h
, 2) even when there is no trigger. Can be used to maintain minimum pump pressure.
Pump to stop on Low Battery. Enable to force pump to stop immediately on low battery
condition.
Use power steer demand to minimum pump speed. Enable this to force the pump to use
power steer demand as a minimum speed. Can be used to maintain minimum pump
pressure for power steering.
Set the pump minimum and maximum speed, maximum torque, acceleration and deceleration at
2A01
h
. The pump speed is calculated as the value from the inputs multiplied by the maximum
speed.
Priority/additive inputs
Each pump input can be configured as a priority input or an additive input. When calculating the
pump demand, the controller selects the demand from the highest priority active input, and then
adds the demand from all the active additive inputs.
Configure priority/additive levels in 2A10
h
and 2A11
h
, and 2A20
h
to 2A26
h
.
Pump throttles
There are 2 pump throttle inputs, which can be configured independently at 2A10
h
and 2A11
h
.
The pump throttles allow proportional control of the pump speed.
Configure inputs as priority or additive and set the voltage levels in the same way as the traction
throttle. The pump throttles must be mapped to analogue inputs.
Pump switches
There are 7 pump switch inputs. Configure each input as priority or additive and assign it a value
at 2A20
h
to 2A26
h
. The pump switches must be mapped to digital inputs.
Pump Driveability Profiles
Pumps have configurable driveability profiles. Profiles are triggered by pump driveability select
switches (2152
h
and 2153
h
). One or more of these switches must be mapped to enable pump
profiles.
Each profile allows the installer to reduce acceleration and deceleration rates, throttle and switch
values and maximum torque.
Set pump driveability profiles at 2A30
h
and 2A31
h
Summary of Contents for Gen4
Page 1: ...Gen4 Applications Reference Manual Document no 177 52701 Rev 3 3 ...
Page 9: ...Chapter 1 Introduction ...
Page 13: ...Chapter 2 About the Gen4 ...
Page 25: ...Chapter 3 Installation ...
Page 45: ...Chapter 4 Specification ...
Page 53: ...Specification Doc 177 52701 Rev 3 3 4 9 Dimensions Size 2 models Size 4 models ...
Page 54: ...4 10 Size 6 models ...
Page 55: ...Chapter 5 System design ...
Page 60: ...5 6 Single traction wiring diagram Figure 13 Single traction wiring diagram ...
Page 63: ...System design Doc 177 52701 Rev 3 3 5 9 On board fuse See On board fuse mounting on page 3 11 ...
Page 64: ...5 10 Figure 15 Dual traction wiring diagram ...
Page 70: ......
Page 71: ...Chapter 6 Configuration ...
Page 110: ......
Page 111: ...Chapter 7 Monitoring Gen4 ...
Page 122: ......