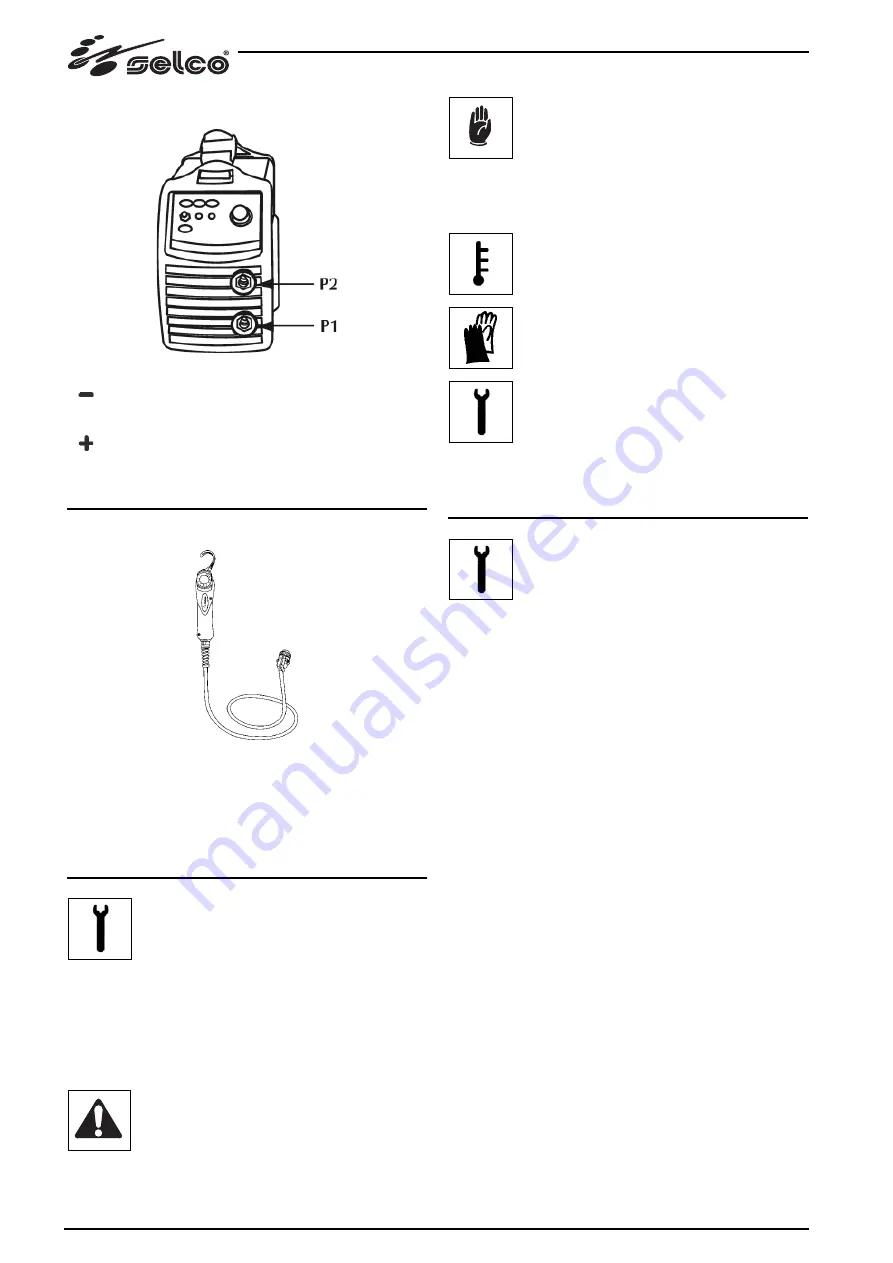
22
3.4 Sockets panel
P1: negative power socket.
For connection of earth cable in electrode welding or
torch in TIG.
P2: positive power socket.
For connection of electrode torch in MMA or earth
cable in TIG.
4 ACCESSORY
4.1
RC18 remote control
This remote control unit allows to ,change linearly the ouput
current without interrupting the welding process.
Operation of the remote control is activated when connected
to the Selco power sources. This connection can be made also
with the system powered on.
5 MAINTENANCE
Routine maintenance must be carried out on the
system according to the manufacturer’s directives.
Any maintenance operation must be performed by qualified
personnel only.
When the equipment is working, all the access and operating
doors and covers must be closed and locked.
Unauthorized changes to the system are strictly forbidden.
Prevent conductive dust from accumulating near the louvers
and over them.
Disconnect the power supply before every opera-
tion!
Carry out the following periodic controls on the
power source:
- Clean the power source inside by means of low-
pressure compressed air and soft bristel brushes.
- Check the electric connections and all the con-
nection cables.
For the maintenance or replacement of torch component,
electrode holder and/or earth cables:
Check the temperature of the component and
make sure that they are not overheated.
Always use gloves in compliance with the safety
standards.
Use suitable wrenches and tools.
Missing the above named maintenance will invalidate all
warranties and exempt the manufacturer from all liability.
6 TROUBLESHOOTING
The repair or replacement of any parts in the
system must be carried out only by qualified
personnel.
The repair or replacement of any parts in the system by
authorized personnel shall cause the product warranty to
become null and void.
The system must not be modified in any way.
The manufacturer declines any responsibility in case the user
not follow these instructions.
The system fails to come on (green LED off)
Cause
No mains voltage at the socket.
Solution
Check and repair the electrical system as needed.
By use qualified personnel only.
Cause
Faulty plug or cable.
Solution
Replace the faulty component.
Contact the nearest service centre to have the sys-
tem repaired.
Cause
Line fuse blown.
Solution
Replace the faulty component.
Cause
Faulty main switch.
Solution
Replace the faulty component.
Contact the nearest service centre to have the sys-
tem repaired.
Cause Faulty
electronics.
Solution
Contact the nearest service centre to have the sys-
tem repaired.
No output power (the system does not weld)
Cause
The system has overheated (thermal alarm - yellow
LED on).
Solution
Wait for the system to cool down without switching
it off (yellow LED off).
Summary of Contents for Genesis 1100
Page 14: ...14...
Page 26: ...26...
Page 38: ...38...
Page 62: ...62...
Page 86: ...86...
Page 98: ...98...
Page 110: ...110...
Page 122: ...122...
Page 134: ...134...
Page 137: ...1 1 1 10 C 40 C 25 C 55 C 50 40 C 90 20 C 2000m 6500 1 2 NR10 137...
Page 138: ...138 1 3 1 4 11 35 1 5 1 6...
Page 139: ...139 8 1 7 EN IEC 60974 10 B A A EN60974 10 A Point of Commom Coupling PCC...
Page 140: ...1 8 IP S IP23S 12 5 mm 60 2 2 1 2 2 10 2 3 230V 15 15 15 2 1 5 140...
Page 142: ...142 3 3 1 I1 O I 3 4 P1 TIG P2 TIG 4 4 1 RC18 RC Selco 5...
Page 143: ...143 6 Reset...
Page 144: ...144 7 7 1 MMA...
Page 145: ...145 Hot Start Arc Force antisticking...
Page 150: ...150 GENESIS 1500...
Page 151: ...151 GENESIS 1500 RC...
Page 153: ...153 GENESIS 1500 RC...
Page 156: ...156 55 02 030 GENESIS 1500...
Page 158: ...158 55 02 032 GENESIS 1500 RC...
Page 166: ...166...