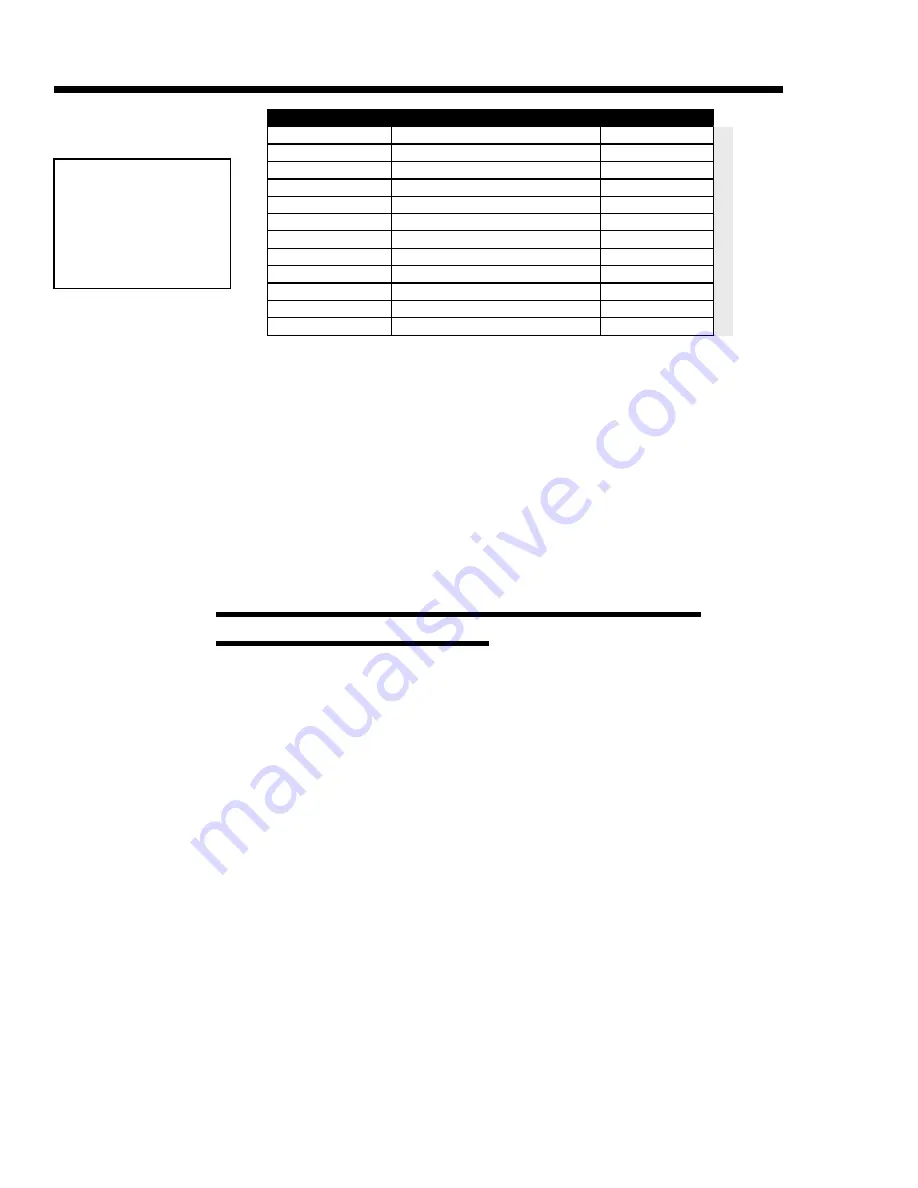
40
Model 4688-IR / 4679-IR
Operation & Maintenance Manual
Manual #087-0007G, 10/2003
Coil address
Description
Suggested Tag
353
STS, relay 1 (1 = energized)
RL1
354
STS, relay 2 (1 = energized)
RL2
355
STS, fault relay (1 = energized)
RLF
356
STS, alarm indicator 1 (1 = active)
AL1
357
STS, alarm indicator 2 (1 = active)
AL2
358
STS, fault alarm indicator (1 = active)
ALF
359
STS, maint indicator (1 = active)
MNT
360
STS, inhibit indicator (1 = active)
IHB
361
STS, concentration units (1 = %v/v)
VOL
362
STS, temperature units (1 = ºC)
DGC
363
STS, lock indicator (1 = active)
LCK
364
STS, remote function failure (1 = fail)
RFF
RE
AD O
N
L
Y
Likewise, how parameter data is accessed also improves efficiency. The use
of coils to read/write data to the instrument increases the quantity of
transactions required to obtain parameter data (Coil addressing is typically
used in applications where PLCs are used). For instance, to obtain data for 3
parameters a separate 8-bit transaction is required to occur (even though the
coil is only 1 bit) for each transaction [query]. However, when using a register
a "
range"
of data
(data high/data low)
can be specified within the query. This
allows the master device to request data for more than one parameter in a
single transaction rather than the high overhead required by accessing
individual coils.
Accessing Parameter Data - The ABC's
of Reading & Writing
To write a parameter into the instrument's nonvolatile memory, the data
element within the application layer must specify the appropriate instructions
by directing values to the appropriate address registers.
Each parameter's
data type, address, and parameter number are specified within the
tables provided in the "Instrument Navigation & Parameter Reference".
Appendix 1 provides Modbus
®
Register Address locations and
Appendix 2 Command Function descriptions.
The basics of writing a value to a parameter is summed up in 4 steps:
1.
Write the input data to the appropriate data registers according to its
data type (i.e. write an alarm setpoint [32-bit] value to RDR1 [register
40015]).
2.
Write the Parameter Number to the parameter select register (PSR).
Note: This step is only required for command functions 1, 2, and 4.
3.
Write the "command" function code to the FSR (see Appendix 2 for
command function code descriptions).
4.
Read the Transmitter Status Register (STS) RFF bit register to verify
success: a 1 indicates the command/adjustment has failed (note: this
step is not required, but is recommended).
The instrument continuously scans the FSR and, upon finding non-0 value,
uses the data in the PSR and the data registers to perform the appropriate
function (afterwards resetting the FSR to 0). This process enables the
instrument to check the validity of data sent and provide real-time feedback.
Refer to Appendix 1
Refer to Appendix 1
Refer to Appendix 1
Refer to Appendix 1
Refer to Appendix 1
for a complete
for a complete
for a complete
for a complete
for a complete
description of
description of
description of
description of
description of
MODBUS™
MODBUS™
MODBUS™
MODBUS™
MODBUS™
Registers & Coil
Registers & Coil
Registers & Coil
Registers & Coil
Registers & Coil
Addressing
Addressing
Addressing
Addressing
Addressing
Artisan Technology Group - Quality Instrumentation ... Guaranteed | (888) 88-SOURCE | www.artisantg.com