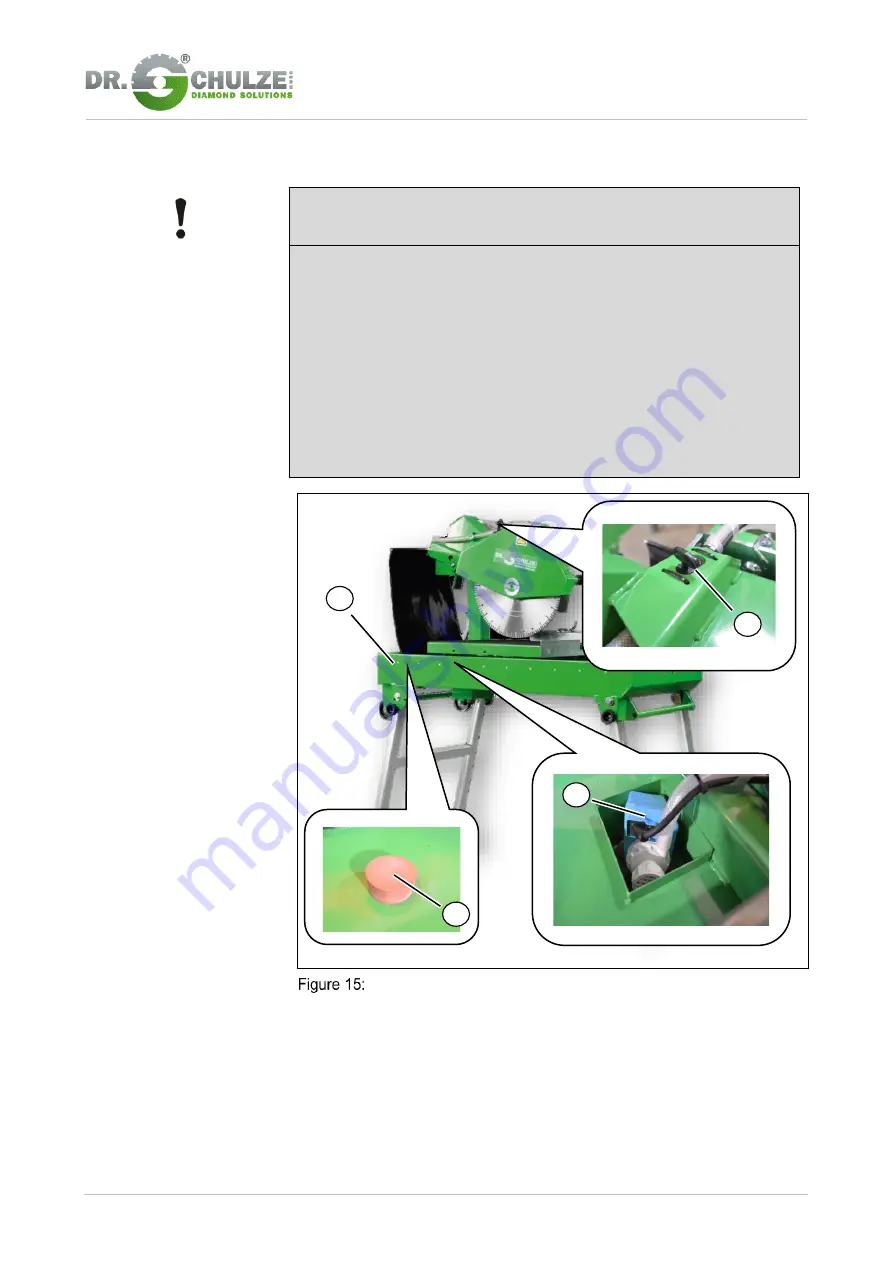
Operation
8
Filling the cooling water
8.3
Table saw BS-350 LST, BS-400 LST-E230, BS-400 LST-E400, BS-500 LST
47
/80
8.3
Filling the cooling water
Attention
If the cutting blade is not adequately supplied with cooling water during
wet cutting, overheating may occur, leading to premature wear, failure or
segment loss of the cutting blade.
−
The outlet nozzle of the water hose on the blade guard must not be
blocked.
−
The water pump must not run dry.
−
Check the level in the cooling water tank regularly and top up if neces-
sary.
−
If there is a risk of frost, drain the cooling water tub and open the shut-
off valve.
Water coolant tank with water pump
1.
Ensure that the rubber stopper (4) is inserted in the tank’s water outlet.
2.
Fill enough water into the water coolant tank (1) that that pump (2) can
always run.
3.
Check that the shut-off valve is set correctly for each cut:
−
Wet cutting: Shut-off valve opened.
−
Dry cutting: Shut-off valve closed.
1
2
3
4