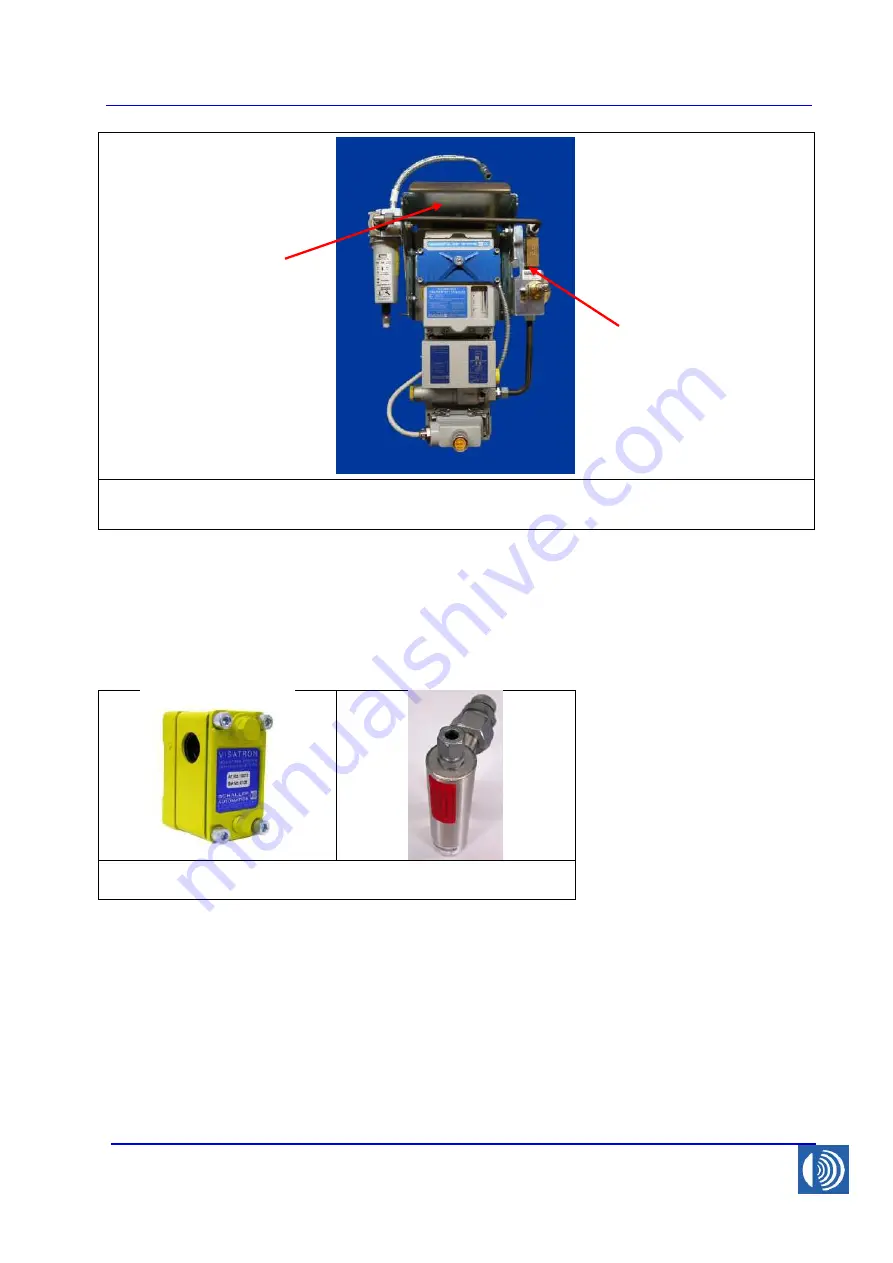
Operation Manual VISATRON® VN115/87plus EX
06/2016
Page 12
SCHALLER AUTOMATION
D-66440 Blieskastel / Saarland / Germany / Industriering 14 / P.O Box 1280
Industrielle Automationstechnik GmbH & Co. KG
Tel. +49(0)6842-508
-
0
/ Fax -260 / eMail: [email protected] / www.schaller.de
Figure 2:
VISATRON® VN115/87plus EX oil mist detector with protection cover
and pressure regulator unit
The suction system always requires a so called 'suction funnel' (see page 20,
) at each suction point. This prevents the system against incoming splash oil.
During normal operation mode of an engine the OMD sucks out a small
concentration of oil mist which was generated by blow-by or mechanical spraying.
This oil mist may fall out in the suction pipes and must be drained out the pipes.
Ideally, drainage flow back ends inside the
engine’s
crankcase.
Figure 3:
Optional Siphon block VN180 optional Pipe siphon
The best method on a VN115/87plus EX installation to drain the system is to use
pipe siphons. Also recommended is the use of siphon blocks.
On 2-stroke engines the crankcase and the combustion chambers are separated by
stuffing boxes, which let the crankcase be nearly free of blow-by. Therefore it's also
possible to use the suction funnel as draining device. In this case it is necessary to
mount the suction pipes with an inclination of greater than 6°.
It is not allowed to blow the air into the engine room!
Protection cover
Pressure
regulator unit