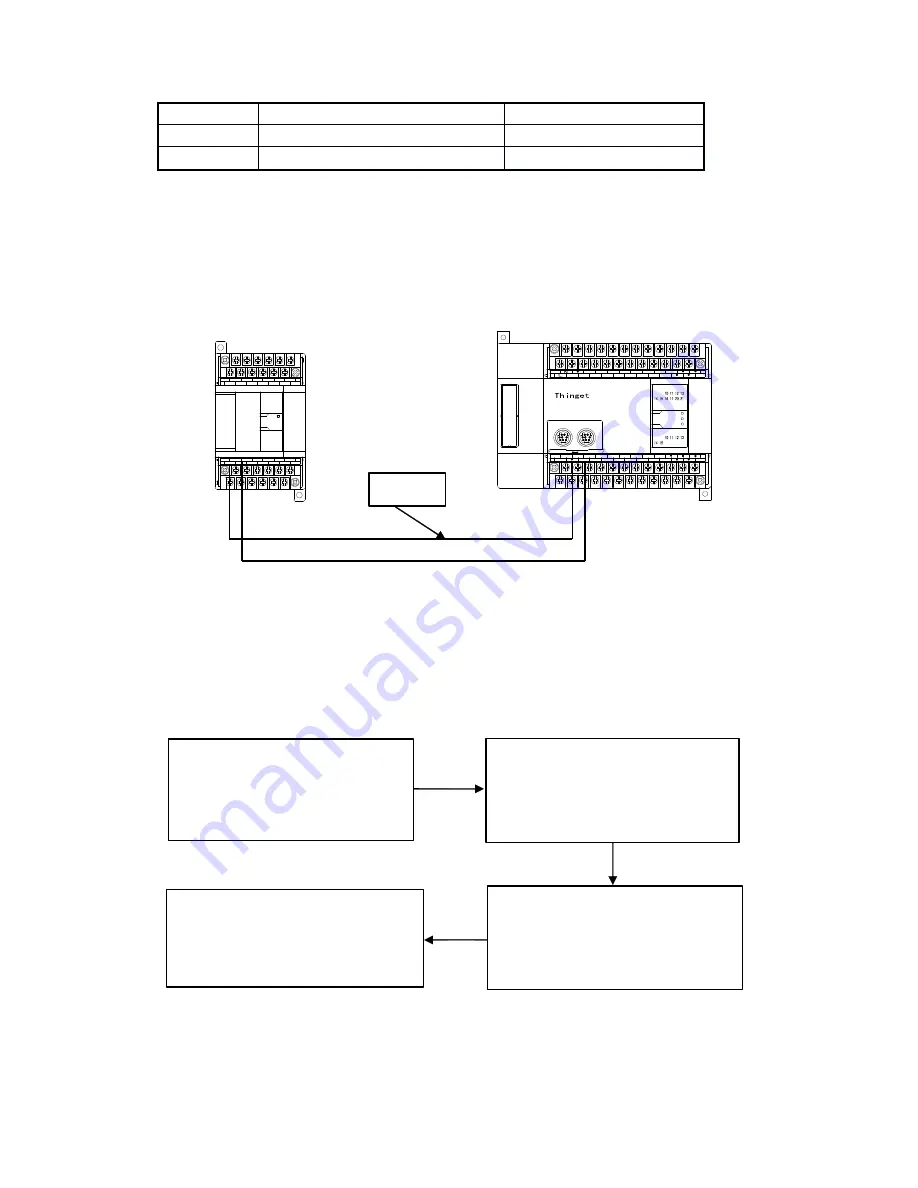
10.5
10.5
10.5
10.5 Application
Application
Application
Application example
example
example
example
This example is based on the communication between the PLC and MA-6TC to do the PID self-
study process.
(1) Hardware connection: connect the RS485 com port A, B of MA-6TC and the PLC.
FG
COM
COM
X0
X1
X2
X3
X4
X5
X6
X7
X15
X14
X13
X12
X11
X10
PWR
Y
X
PORT1
PORT2
COM3
Y5
Y7
Y6
Y11
Y10
Y4
Y3
COM2
Y2
COM1
Y1
COM0
Y0
A
B
24V
0V
1
0
4 5
3
2
RUN
ERR
XC3-24R-E
6 7
7
6
2 3
5
4
0 1
PWR
MA-6TC-P
AO
TC2+
TC3-
TC4+
TC3+
24V
0V
TC5+
TC5-
COM1
COM2
Y1
Y4
Y5
Y3
AO
Y0
Y2
TC1+
TC0+
TC0-
TC1-
TC2-
TC4-
B
A
RS485
(2) Communication parameter setting: baud rate is 19200bps, module station number is 1.
For MA-6TC: baud rate 19200bps, set switch 1-OFF, 2-OFF;
Station number 1, set switch 1-OFF, 2-OFF, 3-OFF, 4-OFF.
For the PLC: com2 baud rate 19200bps, write into the PLC and restart.
(3) The whole process:
(4) Corresponding address
4x179
Channel 3 Temperature difference
Unit: 1ºC
4x120
Channel 4 Temperature difference
Unit: 1ºC
4x121
Channel 5 Temperature difference
Unit: 1ºC
Transfer the data via communication
instruction, the data include PID
parameters,
set
temperature,
temperature control period.
Set on PID control bit and sign bit of
the
module,
read
the
current
temperature.
When the current control process can
not meet the requirement, start the self-
study process and monitor if it is
completed.
After completing the self-study, read
current PID value and reset related
control bits.