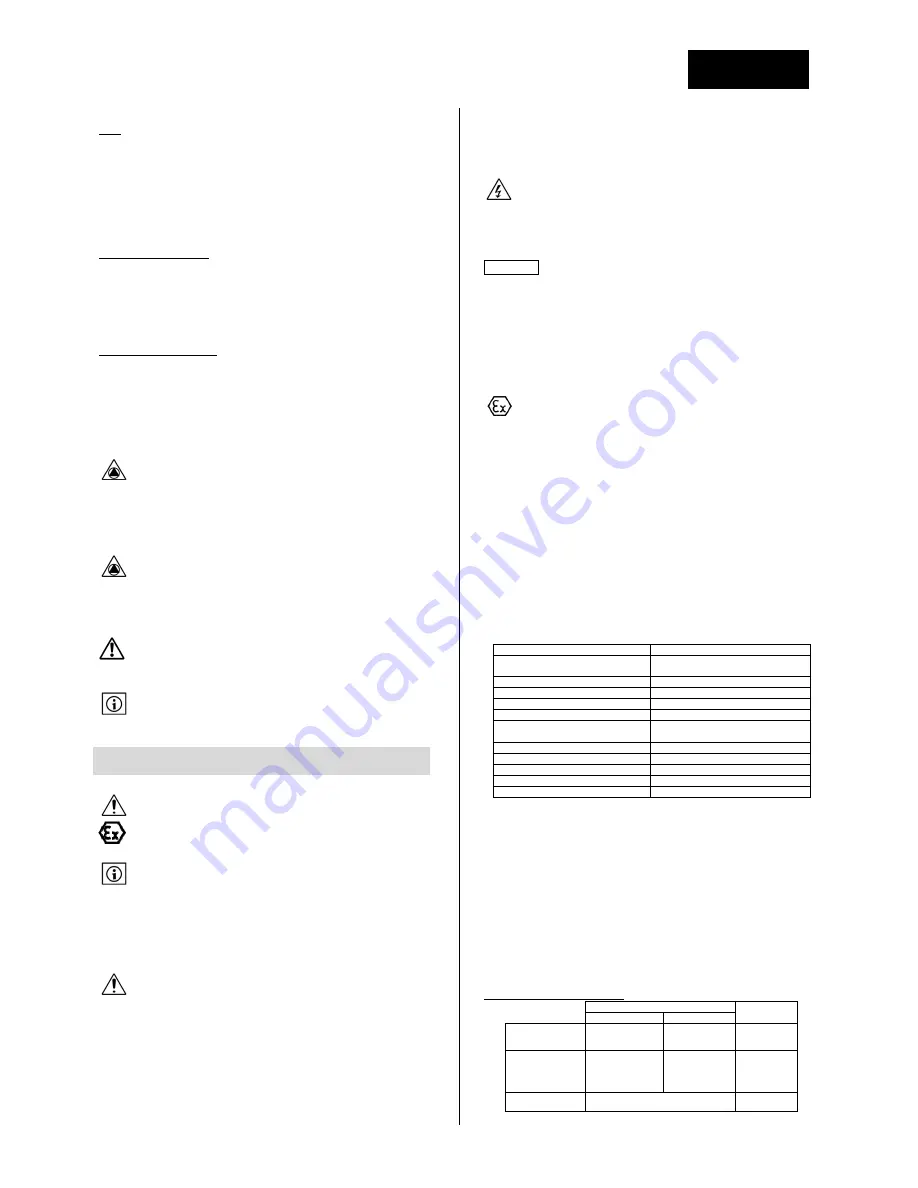
ENGLISH
15
Other
impeller
diameters
:
P
suction
+
P
differential
+
0,5
bar
Flow
:
Delivered
flow
should
be
between
0,1
and
0,2
m
3
/h
Quench
:
Max
Pressure
=
4
bar
Heating
:
Max
pressure
=
4
bar
with
water
vapor
at
140°C
Gland
packing
assembly
:
A
small
leakage
of
packing
gland
is
necessary
to
ensure
proper
lubrication
of
the
packing
rings
(20
to
40
drops
per
minute
is
acceptable).
If
there
is
not
enough
leakage
then
packing
ring
will
be
destroyed
rapidly.
Check
that
the
external
liquid
supply
of
the
gland
packing
is
turned
on
before
starting
‐
up
the
pump
(if
applicable).
Mechanical
seal
assembly
:
For
pumps
equipped
with
a
quench,
external
flushing,
or
a
heating
system,
check
that
the
external
liquid
supply
is
turned
on
before
starting
‐
up
the
pump.
In
any
case
the
mechanical
seal
should
have
time
to
cool
down
between
two
starts.
8.5
SHUTDOWN
Before
the
pump
is
stopped
close
the
discharge
isolating
valve.
Ensure
that
the
pump
runs
in
that
condition
no
more
than
few
seconds.
When
the
pump
has
come
to
a
standstill
:
close
the
suction
isolating
valve.
If
the
pump
is
equipped
with
auxiliary
systems
such
as
a
quench,
heating
system,
flushing,
external
lubrication,
etc
…
it
must
be
closed
at
the
last
step.
If
temperature
is
likely
to
drop
below
freezing
point,
pump
casing
and
auxiliary
connected
systems
should
be
completely
drained
or
otherwise
protected.
For
prolonged
shut
‐
downs
an
adapted
rust
protective
coating
should
be
applied
to
the
inside
and
outside
of
the
pump.
Pumping
explosive,
toxic
or
polluting
fluids
:
make
sure
that
all
necessary
actions
were
taken
to
avoid
the
creation
of
a
hazard
for
people
or
environment
during
drainage
operations.
Products
which
are
sent
back
to
Salmson
must
be
drained
and
cleaned.
Pumped
fluid
should
be
completely
removed
from
the
pump.
9
MAINTENANCE
9.1
GENERAL
INFORMATION
Only
properly
trained
and
skilled
staff
should
undertake
maintenance
operations.
Only
authorized
personnel
should
undertake
maintenance
on
ATEX
certified
equipments.
Make
sure
to
avoid
creation
of
explosion
hazard
while
proceeding
to
maintenance
in
a
ATEX
zone.
All
technical
documents
delivered
with
the
pump
should
be
known
and
should
be
available
near
the
pump.
The
maintenance
crew
should
be
informed
about
the
risks
linked
to
the
use
of
the
pump
and
to
the
pumped
fluids
before
they
can
start
working
on
the
equipment
(dangerous
products,
fluid
and
pump
temperature,
pressurized
parts,
…).
They
should
be
equipped
with
all
appropriated
individual
safety
protections
(glasses,
gloves,
…)
and
should
respect
local
industrial
and
security
rules.
Pump
contains
a
part
of
pumped
fluid
even
when
it
is
at
a
standstill.
Drain
and
flush
pump
casing
with
care
before
starting
pump
disassembly.
Appropriate
lifting
devices
should
be
available
to
help
personnel
moving
heavy
loads.
The
maintenance
area
must
be
clearly
identified.
Install
warning
boards
with
the
words
«
WARNING
:
machine
under
repair
!
»
on
the
pump
and
on
the
control
cabinet.
Any
work
on
the
machine
must
be
performed
when
pump
is
stopped.
Prior
to
any
maintenance
or
repair
work
the
motor
should
be
electrically
isolated
and
secured
against
uncontrolled
start.
Lock
the
main
switch
open
and
disconnect
circuit
breaker.
Withdraw
the
fuses
if
any.
WARNING
:
electrical
equipments
that
must
be
powered
on
during
the
maintenance
work
or
pressurized
equipments
must
be
clearly
identified.
End
of
maintenance
operations
:
all
protective
parts
that
were
removed
before
maintenance
should
be
reinstalled
and
all
security
devices
should
be
reactivated.
Pump
surrounding
area
should
be
cleaned.
9.2
MAINTENANCE
AND
PERIODIC
INSPECTIONS
SCHEDULE
It
is
recommended
to
build
up
a
maintenance
and
inspection
plan
to
ensure
a
reliable
use
of
pump
and
to
reduce
malfunctions
hazards.
Following
check
points
should
be
included
in
this
maintenance
plan
:
Check
state
and
working
of
securities
and
auxiliary
systems,
Check
and
adjust
gland
packing
(if
any)
for
visible
leakage,
Check
for
any
leaks
from
pump
gaskets
and
flanges
seals,
Check
lubricant
level
and
aspect
of
oil
(oil
lubricated
bearings)
in
bearing
bracket,
Check
running
time
and
replacement
frequency
of
lubricants
/
ball
bearings,
Check
the
bearing
bracket
housing
surface
temperature
on
ball
bearings
area,
Check
dirt
and
dust
is
removed
from
pump
and
motor
,
Check
coupling
alignment
(depending
on
pump
variant),
Check
if
there
is
unusual
noises
(cavitations,
hissing,
purring,
…)
or
excessive
vibrations.
Check
point
Periodicity
State
of
the
auxiliary
systems
Depends
on
equipment
type.
See
dedicated
equipment
IOM
Motor
See
manufacturer
IOM
Shaft
sealing
Weekly
Leaks
from
gaskets
Weekly
Oil
level
and
grease
quantities
Daily
/
Weekly
/
Monthly
Lubricants
(ball
bearings)
Replacement
frequency
according
ball
bearing
type
and
shaft
speed
Bearings
surface
temperature
Monthly
Cleaning
Twice
a
year
Alignment
and
coupling
wear
Twice
a
year
Noise,
vibrations
Monthly
Anchoring
quality
Yearly
Those
frequencies
are
given
for
information
only.
They
could
be
used
as
a
basis
to
the
creation
of
a
maintenance
plan
when
starting
a
new
installation.
Depending
on
installation
conditions
and
use,
the
periodicity
will
be
shortened
or
prolonged.
9.2.1
LUBRICATION
Bearing
bracket
sizes
25,
35
and
45,
are
fitted
with
lifetime
lubricated
ball
bearings
as
a
standard.
Bearing
brackets
sizes
55
and
65,
are
fitted
with
grease
lubricated
ball
bearings
and
greasing
nipples
as
a
standard
on
motor
side
and
impeller
side.
These
pumps
are
available
upon
request
with
oil
lubricated
ball
bearings.
Recommended
oil
lubricants
:
Bracket
temp.
<
80°C
Amb
Temp.
<
0°C
1500
RPM
>
1500
RPM
Type
acc.
to
DIN
51517
CL68
CL46
CL22
Kinematic
viscosity
@
50°C
[mm²/s]
61,2
to
74,8
41,8
to
50,8
19,8
to
24,2
Corresp.
Oil
type
SAE
20
et
20W
SAE
10W
Summary of Contents for NOLH series
Page 2: ...NOLH INSTALLATION ET MISE EN SERVICE FRAN AIS N M S n 4086805 Ed 3 10 13...
Page 27: ...FRAN AIS 27 Avec palier roulements lubrifi s bain d huile Montage presse toupe tresses...
Page 32: ...FRAN AIS 32 13 DECLARATION CE...
Page 33: ......
Page 34: ...NOLH INSTALLATION AND OPERATING INSTRUCTIONS ENGLISH N M S n 4086805 Ed 3 10 13...
Page 35: ...2...
Page 59: ...ENGLISH 26 Oil lubricated ball bearings Stuffing box arrangement...