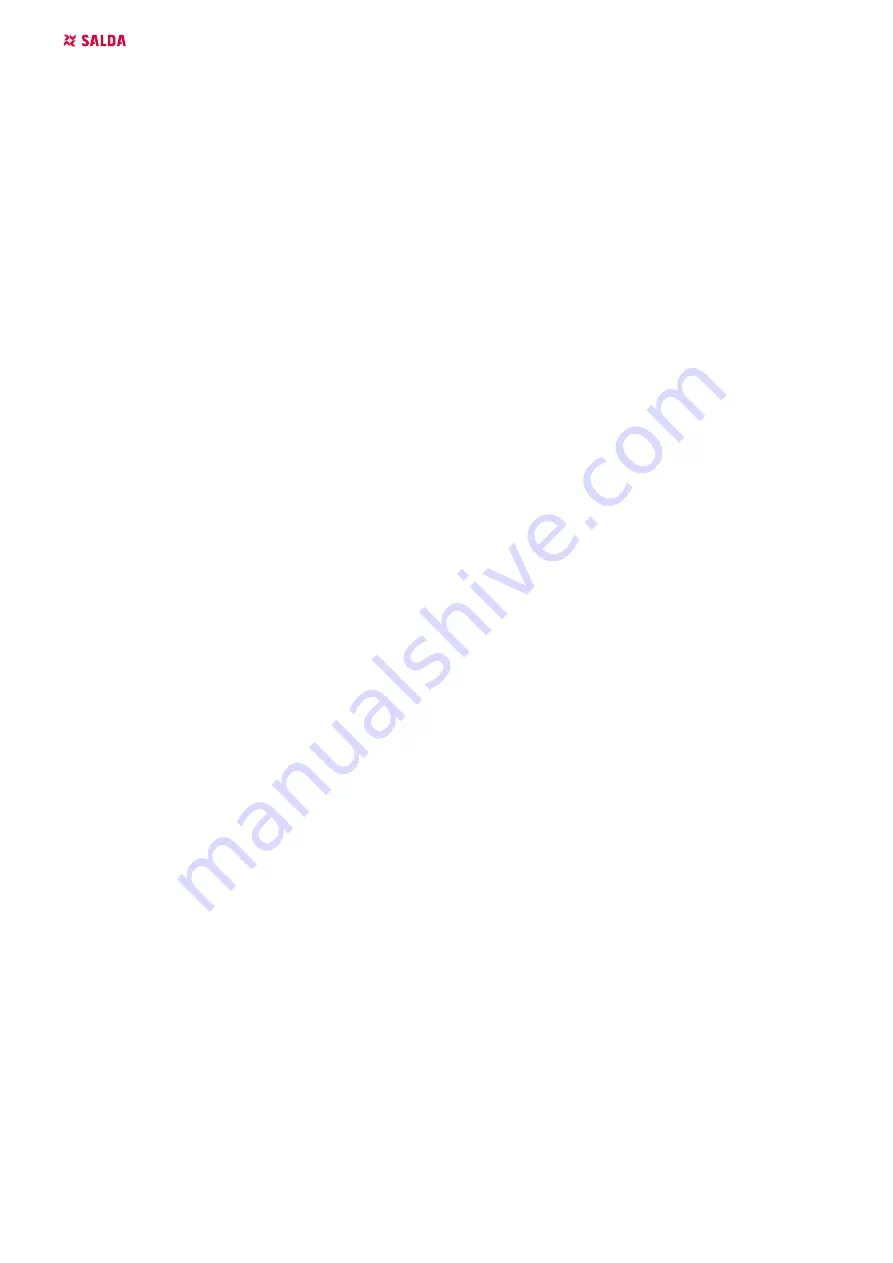
40
| EN
AMBERAIR COMPACT CX V v2019.04
6.4.17. HEAT EXCHANGER CONTROL
Cold - Heat Recuperation
Cold-heat recovery function is designed to control a heat exchanger. Its power is controlled by:
•
Using plate heat exchanger - bypass damper. When it is closed, the heat exchanger is operating at full capacity. Its power is reduced by opening
the damper.
•
Rotary heat exchanger power is controlled by changing its rotating speed or interval. When the rotor rotates at full speed, the heat exchanger
is used at full capacity. The power is reduced by slowing down the rotating speed or increasing the interval.
The heat exchanger can both heat and cool – it depends on air temperature. If it is colder outside than in the premises, the heat exchanger pre-
heats the outdoor air by using the room heat. If it is colder in the premises than outside, the heat exchanger cools down the outdoor air temperature
by room air. Its power is reduced to the minimum when the target supply air temperature is the same as outdoor one. The higher the difference
between the preferred and supply air temperatures, the higher heat exchanger power is used. When it is operating at maximum capacity, it is
allowed to activate other heating/cooling components.
For this function suitable heat exchanger type is indicated in the window
SERVICE › HEAT EXCHANGER
and PID controller coefficients – in the window
ADJUSTER
› PID CONTROLLERS ADJUSTING
.
PID controller output limits are set for rotor or bypass damper, at which their operation starts.
•
If rotor is controlled by 0..10 V signal, at low voltages it does not rotate, the motor heats up, thus the minimum control signal output is limited. If
On/Off rotary heat exchanger is used, PID percentage for activating the rotor is indicated in the window
SERVICE › HEAT EXCHANGER
.
•
If the bypass damper opens only a few percent, noise can occur, thus minimum opening is limited, which also applies when coming to the full
opening. If the plate heat exchanger with a 3-way bypass damper is used, the opening time of the bypass damper is indicated in the window
SERVICE › HEAT EXCHANGER
.
•
If a plate heat exchanger with segment valves is controlled by an external controller is used, then the type of the bypass damper “
REMOTE CONTROL-
LER
” is shown in the window “
SERVICE › HEAT EXCHANGER
”.
•
If a plate heat exchanger with segment valves connected to a controller is used, then the type of the bypass damper is shown in the window
“
SERVICE › HEAT EXCHANGER
” as either “
2 SEGMENTS
” or “
3 SEGMENTS
”. In the case of heat recovery control, segments are closed in sequence, i.e. if heat
recovery is not required, then all the segments are closed and the bypass damper is opened.
When the fans are switched on during the heating season, the heat exchanger runs for 10 minutes at full power, until the system stabilizes.
6.4.18. SYSTEM MONITORING
The service and adjuster environment have the window MONITORING where you can monitor operation of the entire system, i.e. see controller
input and output, CO
2
values, versions of connected modules, date and time, speed of fans, temperatures, pressure, etc. The amount of informa-
tion depends on the system configuration. This tool is designed for preventive maintenance of the system.
6.4.19. STAND-BY MODE BLOCKING
This function is designed to protect the system against the impermissible unit shutdown and it is recommended to limit the unit shutdown up to 1
hour within 12 hours during the winter season. Possible function modes:
•
Always allow shutdown;
•
Block shutdown;
•
Block shutdown in winter;
•
Block shutdown in summer.
It must be indicated for how long the shutdown is permissible within 12 hours. If it is blocked and the system is shut down, the system counts and
informs the user on the remaining time. This function is configured in the service environment (
SERVICE › MAIN › SYSTEM BLOCKING
).
If the time has expired and Stand-by mode is blocked, the user is informed by the function indication.
6.4.20. AIR FLOW ADJUSTMENT
Air-flows are adjusted in the adjuster environment window
ADJUSTER › AIR FLOWS ADJUSTING
. There are 4 of them in the system and they are dedicated to
specific modes:
• Building protection;
• Economy;
• Comfort;
•
Maximum power (BOOST function).
Air-flows are arranged in an ascending order, i.e. upon setting lower air-flow in
COMFORT
mode then in
ECONOMY
mode, the air-flow of the latter is re
-
duced automatically. With respect to the system configuration, air-flows are indicated in percentage, pressure or amounts of air. 100 % value of
air-flow is indicated in service environment window
SERVICE › FANS › FAN SPEED CONTROL
.
6.4.21. MANUAL CONTROL OF COMPONENTS
This function manually activates/deactivates the components controlled by digital and analogue outputs. The latter ones are controlled in percent-
age, and digital ones – by
ON/OFF
. Based on manufacturer’s parameters (by default) the status of all components is
AUTO
, which means that control
is based on air handling unit operating algorithm. Components are displayed by the system configuration. Settings must be saved so they remain
active after power loss.
The lowest power consumption is when the Stand-by mode is on, and position of components –
AUTO
.
Prior to using the manual control function, it is recommended to activate the force shutdown function, which blocks the air handling unit operating
algorithm.