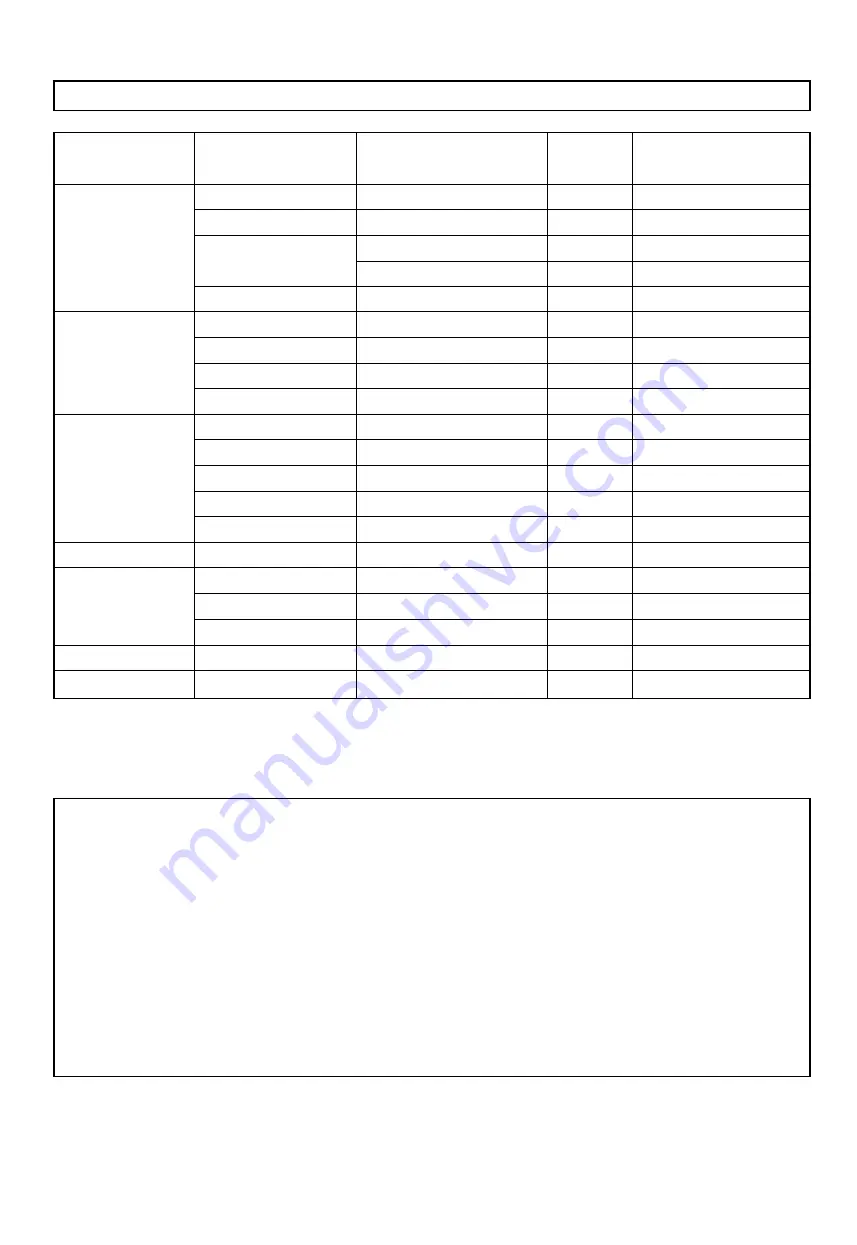
3.
PERIODICAL MAINTENANCE
System or
Mechanism
Part name
Periodical replacement
maintenance parts
Replacement
period
Remarks
1. Brake system
Master cylinder
Seals (rubber parts)
2 years
Adopted machines only
Wheel cylinder
Seals (rubber parts)
2 years
*
Brake piping parts
Brake hose
2 years
1
Air hose
2 years
Adopted machines only
Operating parts
Cable
4 years
*
2. Steering system
Orbitrol
Seals (rubber parts)
2 years
Hydraulic piping parts
Hydraulic hose
2 years
Steering cylinder
Seals (rubber parts)
2 years
Hydraulic pump
Seals (rubber parts)
4 years
3. Power transmission
system
(inclusive of axle)
Axle
Seals (rubber parts)
4 years
Adopted machines only
Travel pump
Seals (rubber parts)
4 years
*
Travel motor
Seals (rubber parts)
4 years
*
Hydraulic piping parts
Hydraulic hose
4 years
*
Isolation rubber
Isolation rubber itself
4 years
*
4. Fuel system
Piping parts
Fuel hose
4 years
5. Engine related
Engine mounting parts
Isolation rubber
4 years
Seals (rubber parts)
Packing and others
4 years
I
Drive parts
V-belt
2 years
6. Cooling system
Piping parts
Radiator hose
2 years
7. Control related parts
Cable
Cable
4 years
Adopted machines only
CAUTION ________________________________________________________
•
With a new machine, change the engine oil after 50 hours of operation for the
first time only.
•
When trouble occurs in the location indicated by the indicator lamp on the
monitor display, sensor will work and corresponding lamp comes on. If this
occurs, conduct necessary service regardless of the periodical service interval
recommendation.
1) The hydraulic filter (line filter) warning lamp
E
>
Replace elements
•
Check the electric wiring at a regular interval not exceeding one month:
1) Damage to the wire harness and loose clamps
2) Loose sockets
3) Function of electrical systems
—
52
—