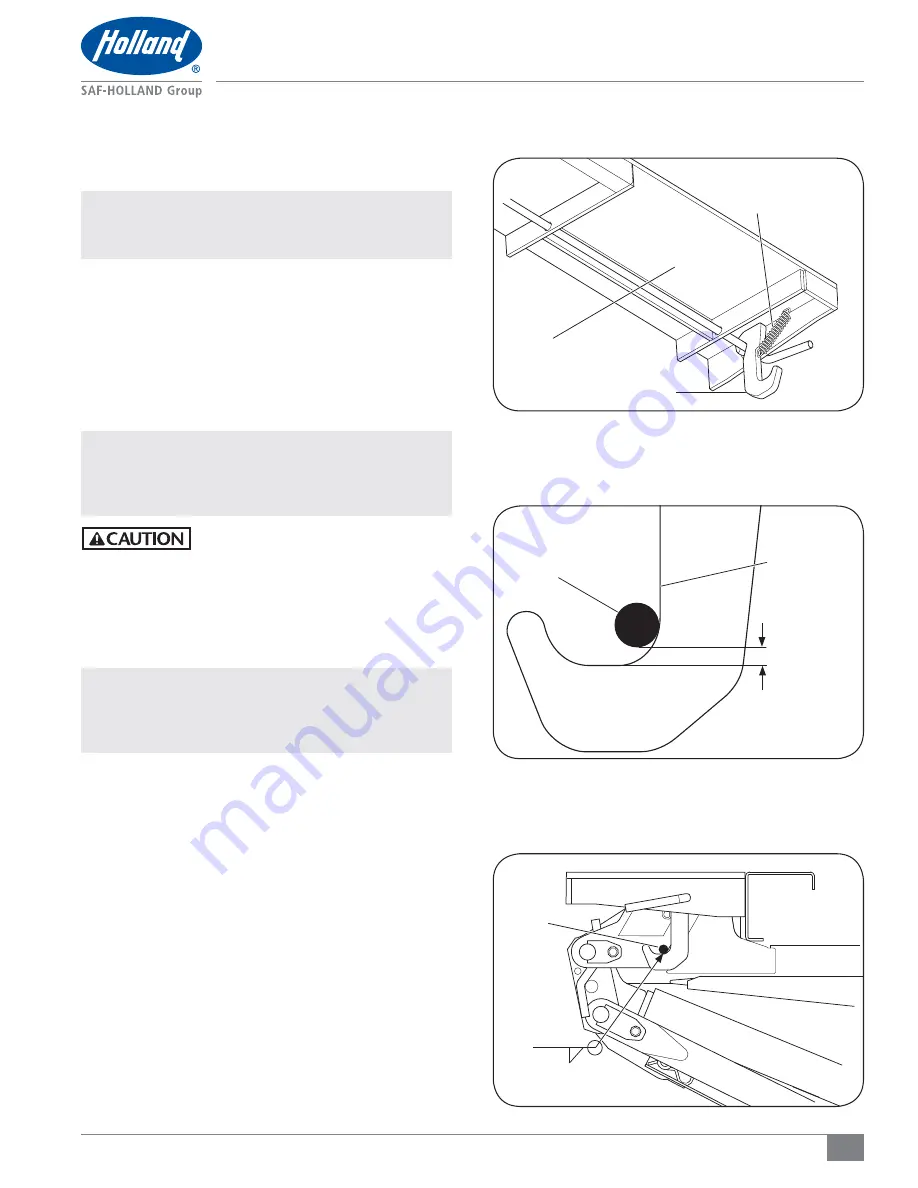
25
XL-TG10153BM-en-US Rev A · 2013-06-27 · Amendments and Errors Reserved · © SAF-HOLLAND, Inc., SAF-HOLLAND, HOLLAND, SAF,
and logos are trademarks of SAF-HOLLAND S.A., SAF-HOLLAND GmbH, and SAF-HOLLAND, Inc.
Return Spring and Latch Pin Installation
Figure 47
SPRING
DECK EXTENSION
LATCH HOOK
Figure 49
LATCH PIN
Figure 48
LATCH PIN
1/4" (6 mm)
CLEARANCE
ENSURE LATCH
IS VERTICAL
12. With the platform in the “UP” position use the platform
adjusting bolts to establish an incline of 1"-2" (25-50 mm)
from platform base to platform tip
(Figure 46)
.
IMPORTANT:
Ensure that the hydraulic hoses do not
interfere with the moving parts. Stretch or
kink while the liftgate is in operation.
13. Fold the platform in accordance with the operating
instructions and check the clearances under the vehicle
during the complete travel until the liftgate is fully stored.
14. Return Spring Installation
1. Install one (1) return spring to each latch hook
(Figure 47).
15. Latch Pin Installation
NOTE:
When welding is required, ensure that the battery
ground cable is disconnected and that all electrical
equipment is completely electrically isolated
before welding is initiated.
Failure to isolate electrical equipment
from ground prior to welding could result
in overload which, if not avoided, could
result in property damage.
1. After verifying that the liftgate installation is proper,
sound, and safe, install the two (2) latch pins that
ensures safety when in the storage position.
IMPORTANT:
When folded and fully raised, the liftgate
MUST contact the rear doorsill or another
rigid structural part of the vehicle, but not
the extension plate.
2. With the liftgate folded and fully raised, position the
roadside and curbside latch pins
(Figure 48)
.
3. After the latch pins are in the correct position, prep the
vehicle frame by grinding off any paint or galvanizing to
within 1"-4" (25-101 mm) of the weld surface.
4. Weld the latch pin to the liftgate
(Figure 49).
5. Touch up paint as required. For galvanized liftgates, touch
up in accordance with the most recent release of ASTM
A 780: Standard Practice for Repair of Damaged and
Uncoated Areas of Hot Dip Galvanized Coatings, which
specifies the use of zinc-rich paints.
1/4"