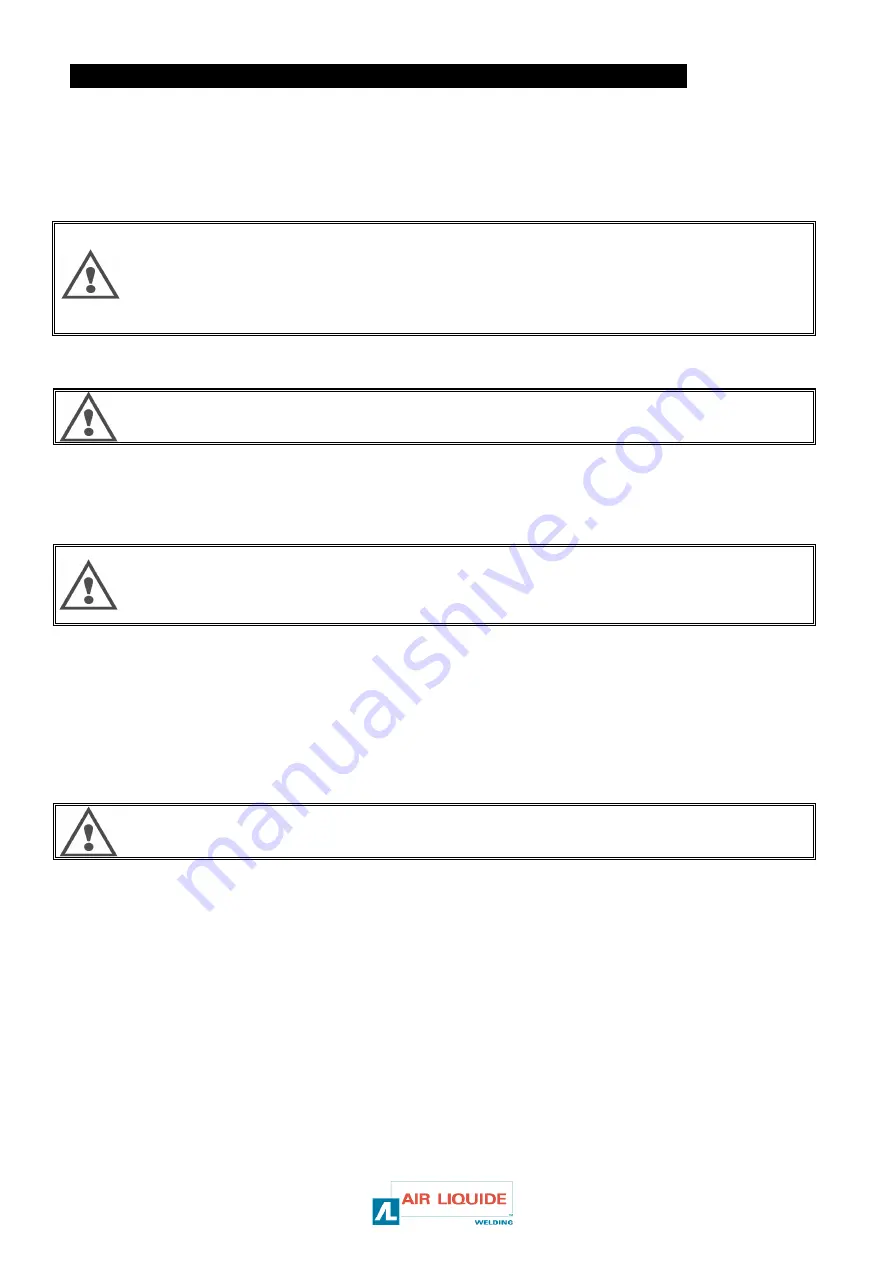
EN
DIGIWAVE
III
7
2 - STARTING UP
2.1. ELECTRICAL CONNECTIONS TO THE MAINS
DIGIWAVE III
is a 400 V 3-phase welding set.
If your mains supply corresponds to requirements, connect the "three-phase + ground" plug to the end of the power cable.
WARNING
: Provided that the public low voltage system impedance at the point of common coupling is
lower than :
98,2 m9 for the DIGIWAVE III 420
20,6 m9 or the DIGIWAVE III 520
This equipment is compliant with IEC 61000-3-11 and IEC 61000-3-12 and can be connected to public lowvoltage systems. It is the
responsibility of the installer or user of the equipment to ensure, by consultation with the distribution network operator if necessary, that
the system impedance complies with the impedance restrictions.
2.2. CONNECTION OF THE WIRE FEEDER UNIT
WARNING:
This must be carried out with the power source power off. The power plugs must be well tied up their tightening must be regularly
controlled, in particular after the moving of an installation.
2.3. CONNECTION OF THE TORCH AND COOLING UNIT
The MIG welding torch is connected to the front of the wire feeder, after ensuring it has been properly outfitted with the wear parts corresponding to the
wire used for welding.
If you use a WATER-COOLED
torch, make sure to connect your cooling unit to the rear of the power source, as well as to the "water" harness.
WARNING
:
Use exclusively the liquid provided by Air Liquide Welding to fill up the cooling unit.
Configuration on the interface is needed to ensure a good working of the cooling unit, cf § 6.1.
No-load operation of the cooling unit while unconnected to a torch may damage it.
2.4. GAS INLET CONNECTION
The gas hose is linked to the harness connecting the power source to the wire feeder. Simply connect it to the pressure-regulator outlet of the gas
cylinder.
☞
Place the gas cylinder on the trolley at the rear of the power source and fasten the cylinder
using the strap.
☞
Open the cylinder valve slightly to allow existing impurities to escape and then reclose it.
☞
Mount the pressure regulator/flow meter
☞
Connect the gas hose supplied with the wire feeder harness to the regulator's outlet
☞
Open the gas cylinder.
During welding, the gas flow rate (l/min) should correspond to the diameter of the nozzle (mm).
WARNING
Make sure the gas cylinder is properly secured on the trolley by attaching the safety strap.
For optimal use, the welding installation must respect the following positioning constraints for correct cooling.