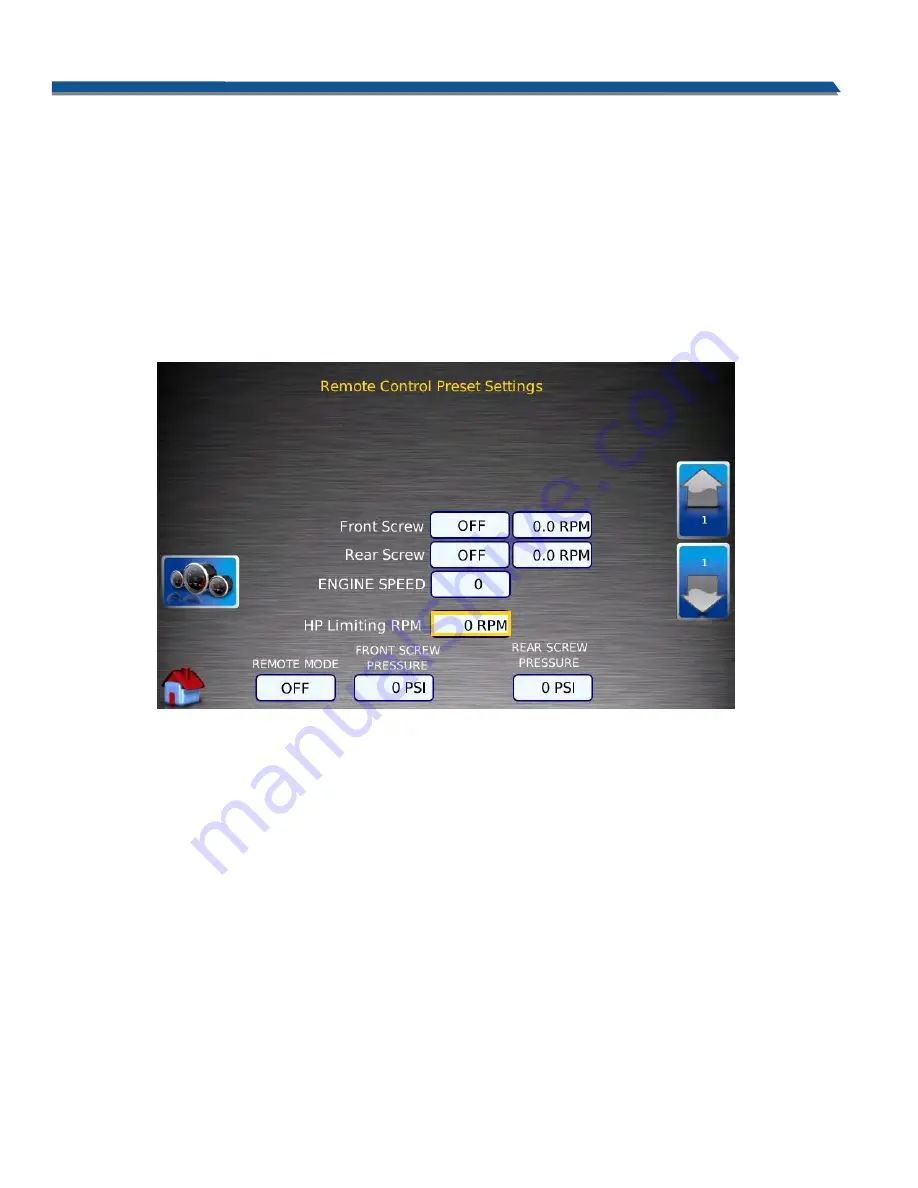
Page # 23
877 1st Ave. N.W. | Sioux Center, IA 51250 | Toll Free: 1.866.722.1488 | siouxautomation.com
OPERATION
REPLACEMENT PARTS
READ complete manual CAREFULLY
BEFORE attempting operation.
877 1st Ave. N.W. | Sioux Center, IA 51250 | Toll Free: 1.866.722.1488 | siouxautomation.com
OPERATION
REPLACEMENT PARTS
READ complete manual CAREFULLY
BEFORE attempting operation.
CONTROLS
Page | 4
On the User Settings Main Screen (Figure 4) there are three options – Remote Control Settings, User Settings, and
Home. By pressing the “Remote Control Settings” icon, the display will navigate to the Remote Control Settings
page (Figure 5). This screen allows the operator to program a horsepower limiting auger speed. Any changes
made to this screen are saved upon exit. Refer to the Machine Operation section of this manual for detailed
descriptions of settings.
By pressing the Up and Down icon keys, the operator can choose the auger RPM at which the mixer will operate at
when the pressure is too high. The value will keep changing until the key is released.
Figure 5
By pressing the gauge key, the display will navigate back to the Operation Screen. Pressing the Home icon will
return the display to the Home screen.
From the User Settings main screen (Figure 4), pressing the User Settings icon will bring up the display’s User
Settings (Figure 6). This screen allows the operator to choose display settings, brightness, units of measure,
language, and a background. Pressing the side buttons will navigate the selection box up or down to change the
setting. By pressing the upper left button, the display defaults are restored. The lower left button will navigate
back to the Home screen.
Summary of Contents for 3600 Series
Page 129: ...MAINTENANCE RECORD...
Page 130: ...MAINTENANCE RECORD...
Page 131: ...MAINTENANCE RECORD...
Page 134: ......