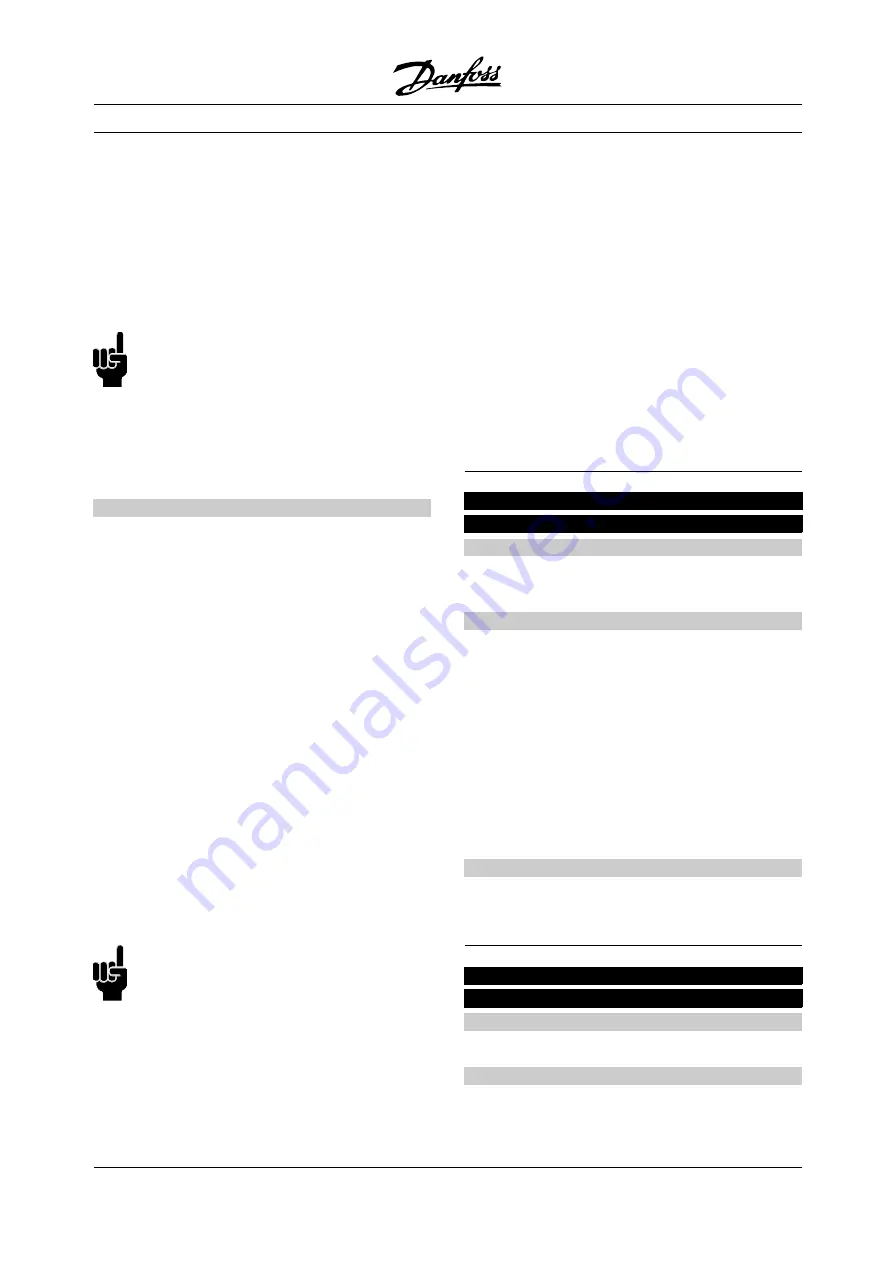
VLT
®
8000 AQUA
for small motors, depending on the rating of
the motor used (the time for a 7.5 HP motor,
for example, is approx. 4 minutes).
-
Alarms and warnings will be shown in the display
if faults occur during motor adaptation.
-
AMA can only be carried out if the rated motor
current of the motor is min. 35% of the rated
out-put current of the AFD.
NOTE
Some motors (such as motors with 6 or
more poles) may be unable to run Automatic
Adaptation. Limited AMA or use of parameters
123 and 124 is a procedure which can be effective
in such cases since procedure measures motor
’
s
stator and effects of cable length. Multiple motor
applications cannot use any form of AMA.
Description of choice:
Select
Automatic adaptation
[1] if the AFD is to carry
out a complete automatic motor adaptation. Select
Limited AMA
[2] if an LC-filter has been placed between
the AFD and the motor, or for six or more pole motors.
Procedure for automatic motor adaptation:
1. Set the motor parameters in accordance with
the motor nameplate data given in parameters
102-106
Nameplate data
.
2. Connect 24 V DC (possibly from terminal 12)
to terminal 27 on the control card.
3. Select Automatic adaptation [1] or Limited AMA [2] in
parameter 107
Automatic motor adaptation
, AMA.
4. Start up the AFD or connect terminal 18 (start)
to 24 V DC (possibly from terminal 12).
If the automatic motor adaptation is to be stopped:
1. Press the [OFF/STOP] key.
After a normal sequence, the display
reads: AMA STOP
1. The AFD is now ready for operation.
NOTE
[RESET] key must be pressed after AMA is
completed to save results into drive.
If there is a fault, the display reads: ALARM 22
1. Check for possible causes of the fault in
accordance with the alarm message. See
list of warnings and alarms.
2.
Press the [RESET] key to clear fault.
If there is a warning, the display reads:
WARNING 39-42
1. Check for possible causes of the fault in accordance
with the warning. See
list of warnings and alarms
.
2. Press the [CHANGE DATA] key and select
"Continue" if AMA is to continue despite the
warning, or press the [OFF/STOP] key to stop
the automatic motor adaptation.
108 Variable Torque Starting Voltage
(VT START VOLT)
Value:
0.0 - parameter 103
Motor voltage, U
M,N
✭
depends on par. 103
Motor voltage, U
M,N
Function:
This parameter specifies the start-up voltage for
VT characteristics at 0 Hz. It is also used for
motors connected in parallel.
The start-up voltage represents a supplementary
voltage input to the motor. By increasing the start-up
voltage, motors receive a higher start-up torque. This
is used especially for small motors (< 4.0 kW/5 HP)
connected in parallel, as they have a higher stator
resistance than motors above 5.5 kW/7.5 HP. This
function is only active if
Variable torque
[1], [2] or [3] has
been selected in parameter 101
Torque characteristics
.
Description of choice:
Set the start-up voltage at 0 Hz. The maximum voltage
depends on parameter 103
Motor voltage, U
M,N
.
109 Resonance damping
(RESONANCE DAMP.)
Value:
0 - 500 %
✭
100 %
Function:
High-frequency electric resonance problems between
the AFD and the motor can be eliminated by
adjusting the resonance damping.
✭
= factory setting. () = display text [] = value for use in communication via serial communication port
MG.80.A7.22 - VLT is a registered Danfoss trademark
96
Rosewood STP ST42 General (Operation and Maintenance Manual - Part 4:
Section 6.3 Manufacturers Manuals 6.3.33 Danfoss VLT Aquadrive 8000) Vendor Manual
QP Id: VM207
Active: 03/09/2013
Page 102 of 208