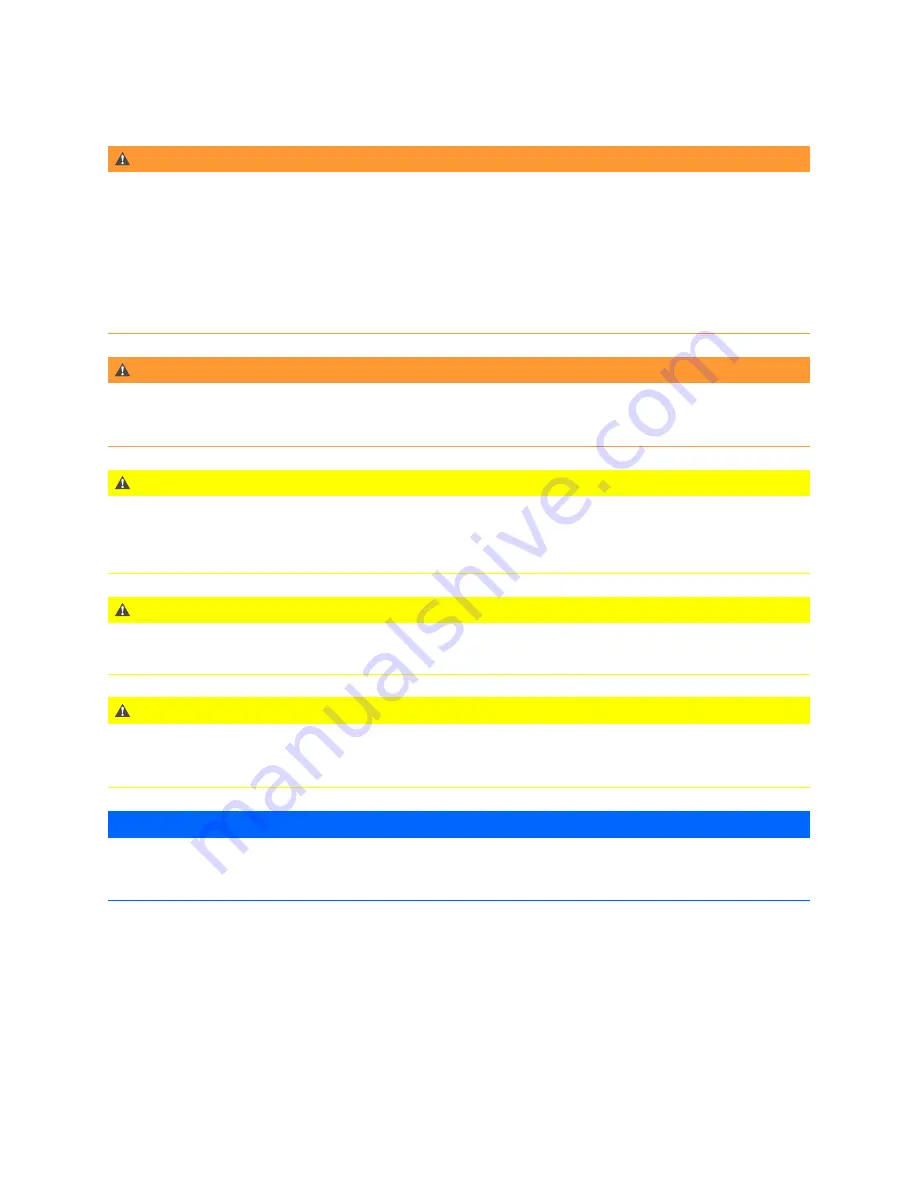
WARNING!
On completion of any maintenance and/or modifications, make sure:
•
All tools and equipment are removed.
•
No contamination (water/dust) is in the compartments.
•
The detector is wiped clean.
•
Vents are clear and not obstructed.
•
The system is in a safe state for operation.
Failure to follow this warning could cause a potentially hazardous situation, which if not avoided, could result in death or serious
injury.
WARNING!
TRANSPORTATION HAZARD
Use safety approved lifting equipment. Ensure that the equipment is tested, meets the lifting ratings for the weight of the
equipment, and is in good operational condition. Failure to verify that equipment meets the lifting ratings and is in good operational
condition may injure personnel or damage the detector.
CAUTION!
EQUIPMENT DAMAGE
Always follow the startup procedure. Damage to the detector may result from a failure to follow this procedure.
Failure to perform pre-system startup checks may cause damage to equipment.
CAUTION!
EQUIPMENT DAMAGE
Always follow the shutdown procedure. Damage to the detector may result from a failure to follow this procedure.
CAUTION!
EQUIPMENT DAMAGE
Ensure that the local power voltage where the unit is to be installed corresponds to the unit’s nominal voltage as given on the name
plate label.
NOTICE
As a general principle, if any optical component other than the cell assembly, the laser modules, and the detectors is unserviceable,
Emerson
TM
must repair the detector. This is because the repair, replacement, and alignment of the optical components requires the use of
special optical testcalibration equipment and procedures. When an item is unserviceable, and no replacement procedure is given in this
manual, Emerson
TM
must repair the fault.
Summary of Contents for CT4215
Page 1: ...Reference Manual 00809 0100 4245 Rev AB July 2018 Rosemount CT4215 Leak Detection System ...
Page 12: ...Contents ii Rosemount CT4215 ...
Page 28: ...Installation 16 Rosemount CT4215 ...
Page 30: ...Startup 18 Rosemount CT4215 ...
Page 44: ...Operation 32 Rosemount CT4215 ...
Page 50: ...Maintenance 38 Rosemount CT4215 ...
Page 54: ...Troubleshooting and diagnostics 42 Rosemount CT4215 ...