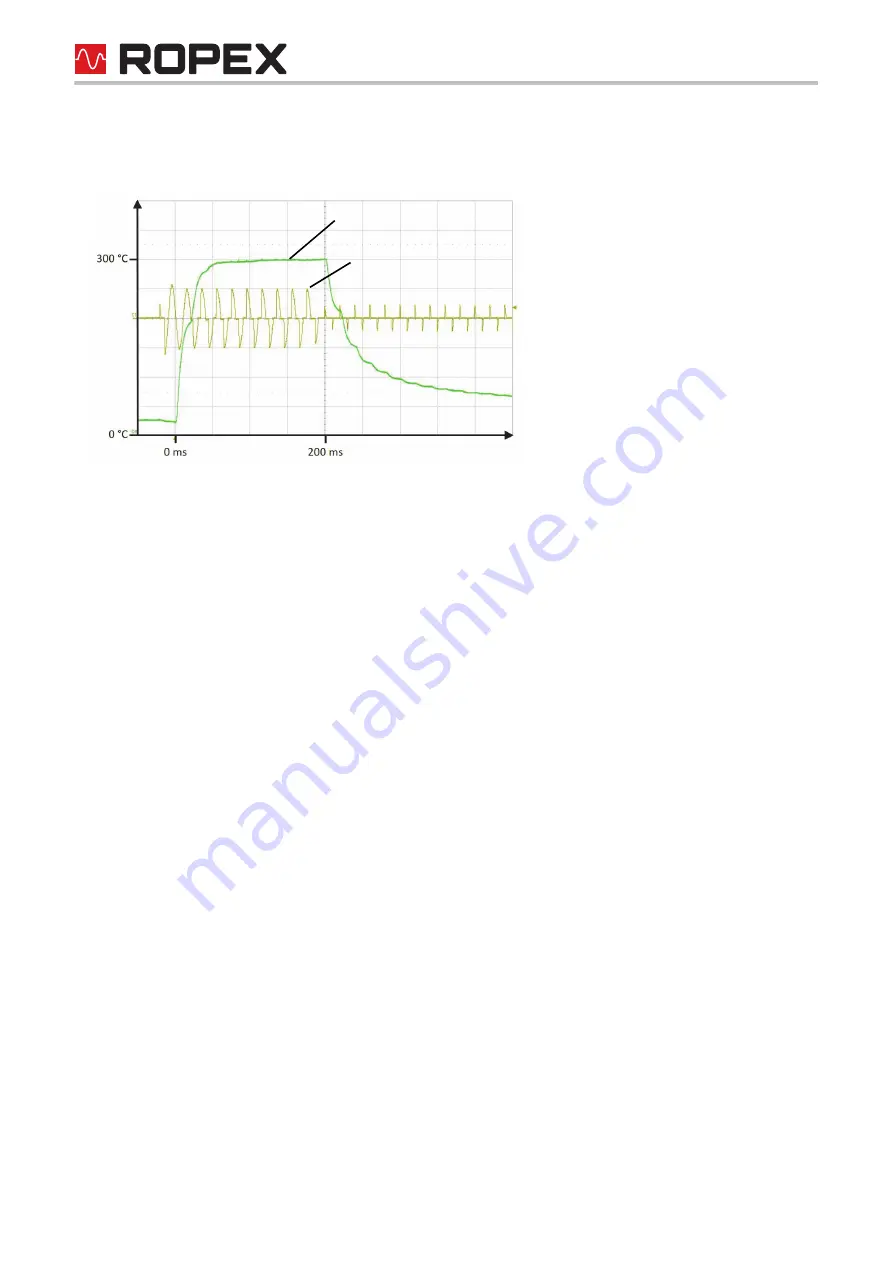
Device features
Seite 8
UPT-6010
Version 2
A highly dynamic thermoelectric control loop is established in this way because purely electrical variables are
measured in rapid succession and the heating layer of the UPT heating element has a small mass.
Thanks to the microprocessor based technology, the controller has an optimized control algorithm as well as
numerous functions tailored to specific tasks such as AUTOCAL, ALARM with error diagnosis etc. These are
described in detail below.
5
Device features
The CIRUS
®
temperature controller UPT-6010 is equipped with a PROFINET interface. Through this interface, all
functions and parameters can be parameterised by means of the higher level machine controller. In addition,
important controller information is queried and can be processed accordingly.
The ACTUAL temperature of the heating element is output through the PROFINET interface and through an ana-
logue output 0…10 VDC. The real heating element temperature can be visualised on an external display instru-
ment (e.g. ATR-x) or via the operating unit of the machine controller.
The UPT-6010 has an integrated error diagnosis that checks both the external system (heating element, wiring,
etc.) and the internal electronics. A differentiated error message is output through the PROFINET interface in case
of malfunction.
To increase operational security and immunity to interference, all PROFINET signals from the controller and
heating circuit are electrically isolated.
Adjustment for different heating element alloys and setting of the temperature range to be used (0…300 °C or
0…500 °C) can be made through coding switches on the temperature controller itself or through the PROFINET
interface.
The compact design of the CIRUS
®
temperature controller UPT-6010 as well as the plug-in connecting terminals
make mounting and installation easier.
An overview of the most important features and functions:
• Easy calibration of the heating element through AUTOCAL, the automatic zero-point setting.
• Eight channels permit switching of the calibration parameters during tool change.
• High flexibility: The AUTORANGE function covers a secondary voltage range of 0.4 V to 120 V and a current
range of 30 A to 500 A.
• Automatic adjustment to the network frequency in the range of 47 Hz to 63 Hz.
• Wide voltage range for flexible use from 110 VAC to 415 VAC
• Easy and convenient system diagnosis and process visualisation through the free, downloadable software
ROPEXvisual®
Temperature impulse
Current impulses
Time
Te
mp
era
tu
re/
Cu
rre
n
t