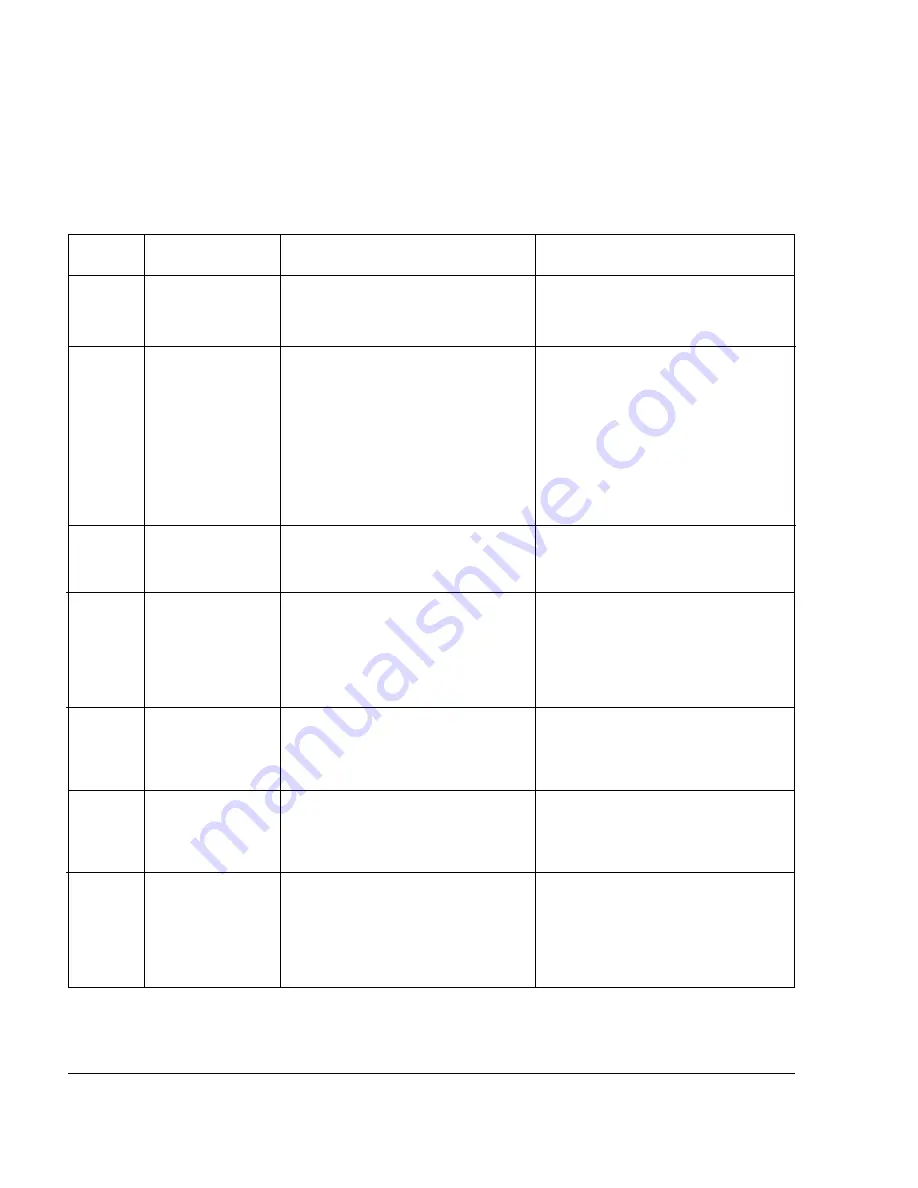
5-2
GV3000/SE 230 VAC Drive, Software Reference Version 6.04
Corrective Action
Verify that P.011 is set correctly.
Check that the analog input source
supply is
≥
4 mA.
Increase the deceleration time in P.002,
P.018.
Install optional snubber resistor braking
kit.
Verify that the AC input is within
specification. Install an isolation
transformer if required.
Check the actual line voltage against
U.018.
Allow identification procedure to finish.
Press keypad STOP/RESET to cancel
identification procedure if desired.
Proceed with V/Hz identification
procedure, start drive and allow
procedure to begin. Display will change
to I-Ac when drive is started.
Change H.020 to OFF to cancel
identification and clear I-En if desired.
Adjust line voltage parameter (H.021 or
U.018) to match actual AC line voltage.
Allow vector self-tuning procedure to
finish.
Press keypad STOP/RESET to cancel
vector self-tuning procedure if desired.
Proceed with vector self-tuning, start
drive and allow self-tuning procedure to
begin. Display will change to S-Ac
when drive is started.
Change U.008 to OFF to cancel
self-tuning and clear S-En if desired.
5.1. Identifying Alarm Codes and Recovering
GV3000/SE drive alarm codes are shown in table 5.1. Note that the alarm code will
only be displayed for as long as the problem exists. Once the problem has been
corrected, the alarm code will disappear from the display.
Table 5.1 - List of Alarm Codes
Alarm
Description
Analog input signal
loss
High DC bus voltage
V/Hz identification
procedure active
V/Hz identification
procedure enabled
Low AC input line
Vector self-tuning
active
Vector self-tuning
enabled
Code
Aln
HIdc
I-Ac
I-En
LIL
S-Ac
S-En
Alarm Cause
P.011 = 8, 9, 10, or 11 and the 4 to
20 mA input is below 2 mA.
The DC bus is charged above the trip
threshold. (DC bus is above 371 VDC.)
V/Hz identification procedure is
enabled and in progress.
H.020 = On; V/Hz identification
procedure has been enabled but
not started.
AC input line is low.
For SVC, indicates DC bus is being
regulated. No corrective action is
required.
Vector self-tuning is enabled and in
progress.
U.008 = On; vector self-tuning has been
enabled but not started.