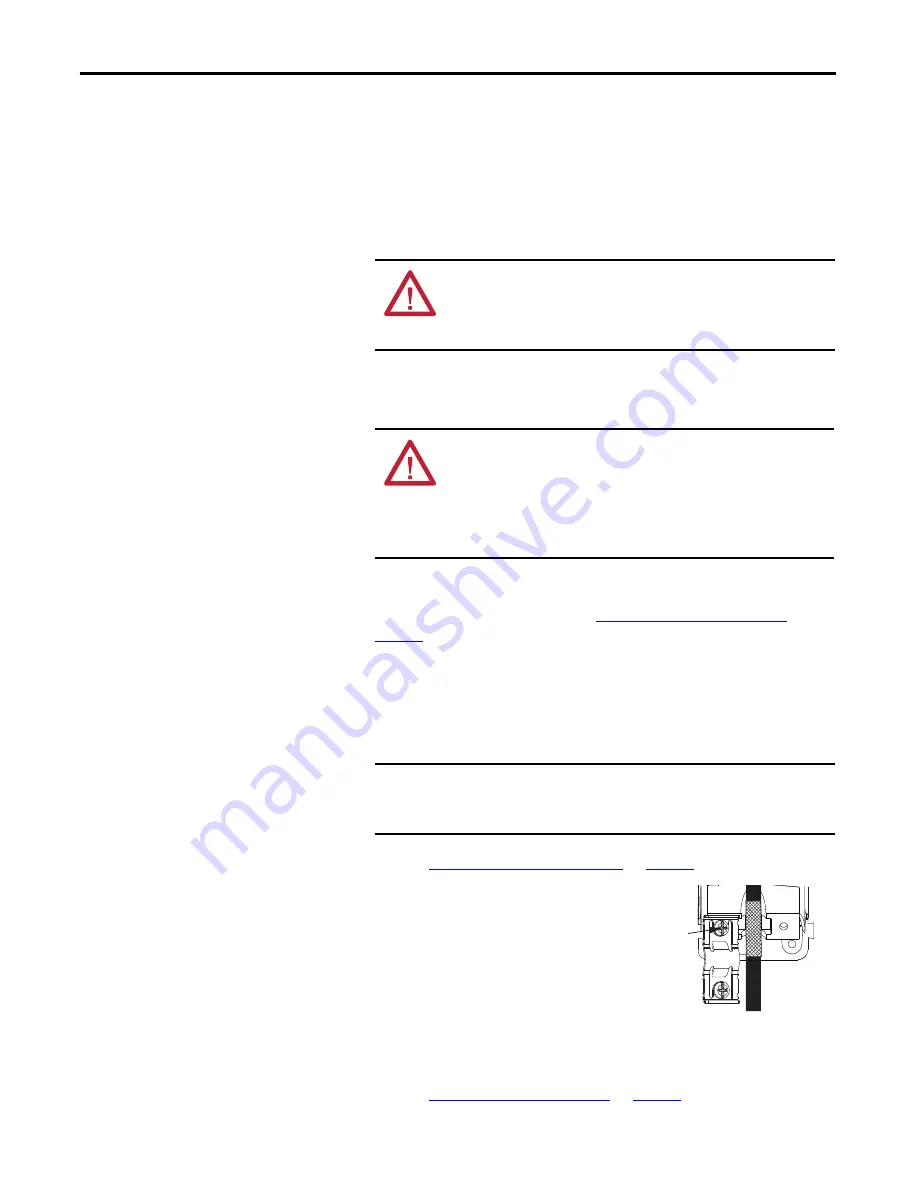
154
Rockwell Automation Publication 2198-UM001D-EN-P - May 2014
Chapter 8
Removing and Replacing Servo Drives
Remove and Replace
Kinetix 5500 Servo Drives
Follow these steps to remove and replace servo drives from the panel.
Remove Power and All Connections
1.
Verify that all control and input power has been removed from the system.
2.
Wait five minutes for the DC bus to discharge completely before
proceeding.
3.
Label and remove all wiring connectors from the drive you are removing.
To identify each connector, refer to
on
.
4.
Remove the shared-bus input wiring connectors, T-connectors, and bus-
bars from the drive you are removing.
Refer to
.
5.
Use a screwdriver to loosen the
two cable clamp screws,
removing the one on the right.
6.
Remove the single motor cable from the cable shield clamp.
7.
Remove the ground screw and braided ground strap.
Refer to
.
ATTENTION:
To avoid shock hazard or personal injury, assure that all
power has been removed before proceeding. This system can have
multiple sources of power. More than one disconnect switch can be
required to de-energize the system.
SHOCK HAZARD:
This product contains stored energy devices. To avoid
the hazard of electrical shock, verify that voltage on capacitors has
been discharged before attempting to service, repair, or remove this
unit. Do not attempt the procedures in this document unless you are
qualified to do so and are familiar with solid-state control equipment
and the safety procedures in publication NFPA 70E.
TIP
You do not need to remove the shunt (RC) connector, unless there is an
external shunt wired to it.
IMPORTANT
DC bus T-connectors latch on both sides when inserted into the drive.
To remove the DC bus T-connector, at least one latch must be pried
away with a non-conductive probe.
Retention Screw
(loosen, do not remove)
Motor Cable