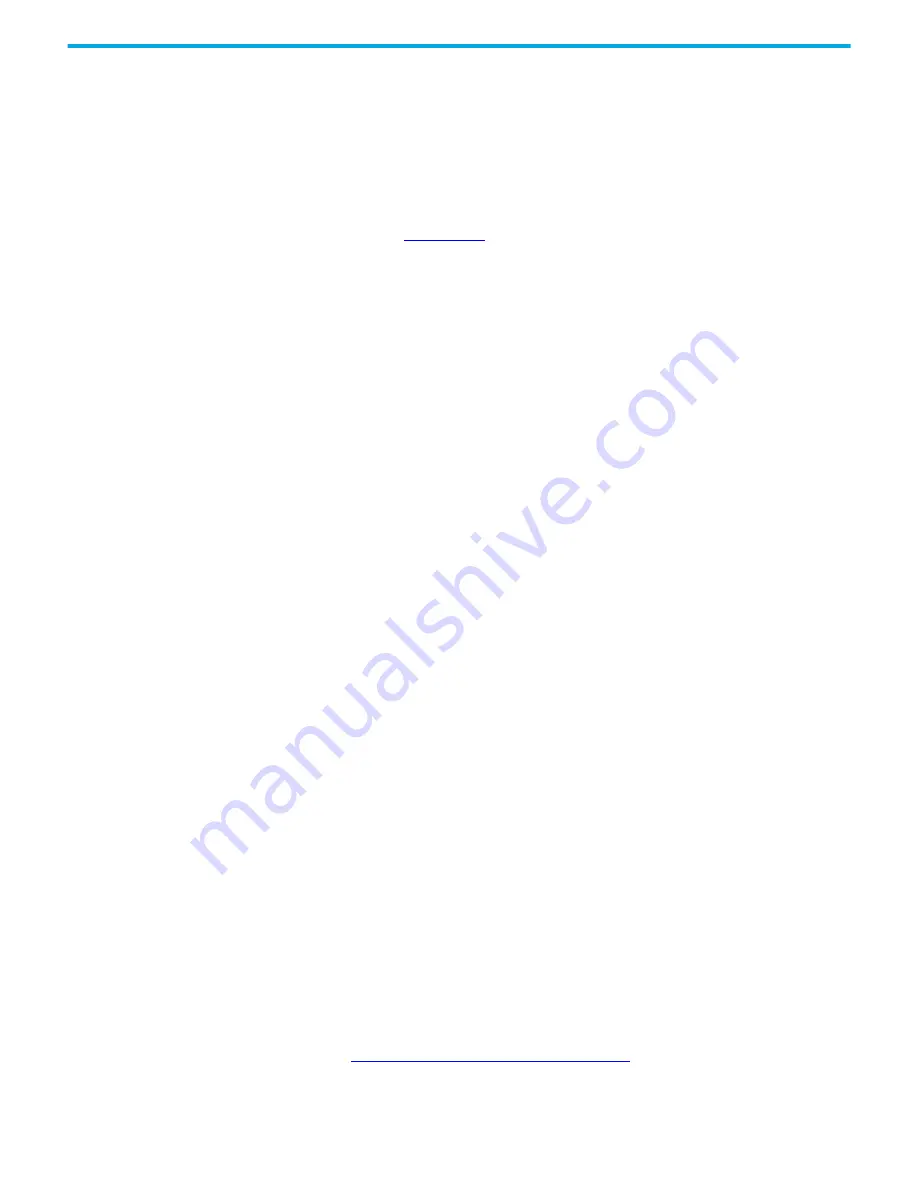
Rockwell Automation Publication 1766-UM001O-EN-P - September 2021
209
Appendix F MicroLogix 1400 Distributed Network Protocol
2. Click Apply and OK.
3. Perform a power cycle in order for the changes to take effect.
The controller does not allow any incoming EtherNet/IP connections
anymore. This means that you cannot use RSLogix 500/RSLogix Micro
over Ethernet port to monitor or change the configuration/user
program.
For more information about Ethernet Port Disable, see MicroLogix 1400
Programmable Controllers Instruction Set Reference Manual,
publication
DNP3 Slave Application
Layer
This section covers DNP3 Slave Application Layer Function Codes and Internal
Indications.
For details of Packet Formats for the request and response, see the DNP3
Protocol specifications.
Function Codes
FC_CONFIRM (FC Byte = 0x00)
00 – Confirm
A DNP3 master sends a message with this function code to confirm receipt of a
response fragment. In a general environment, the controller receives a
response with this function code. But the controller may generate a response
with this function code when a DNP3 Master sends a request with the CON bit
set in the application control header.
FC_READ (FC Byte = 0x01)
01 – Read
The READ function code is used by a DNP3 master to request data from the
controller.
FC_WRITE (FC Byte = 0x02)
02 – Write
The WRITE function code is used to write the contents of DNP3 objects from
the DNP3 master to the controller. This function code is used for clearing bit
IIN1.7 [DEVICE_RESTART], setting time in the controller and downloading
user programs to the controller.
FC_SELECT (FC Byte = 0x03)
03 – Select
The SELECT function code is used in conjunction with the OPERATE function
code as part of select-before-operate method for issuing control requests. This
procedure is used for controlling binary output (CROB) or analog output
(AOB) objects.
FC_OPERATE (FC Byte = 0x04)
04 – Operate
See
Summary of Contents for 1766-L32AWA
Page 10: ...10 Rockwell Automation Publication 1766 UM001O EN P September 2021 Table of Contents Notes ...
Page 302: ...302 Rockwell Automation Publication 1766 UM001O EN P September 2021 Glossary Notes ...
Page 308: ...308 Rockwell Automation Publication 1766 UM001O EN P September 2021 Index Notes ...