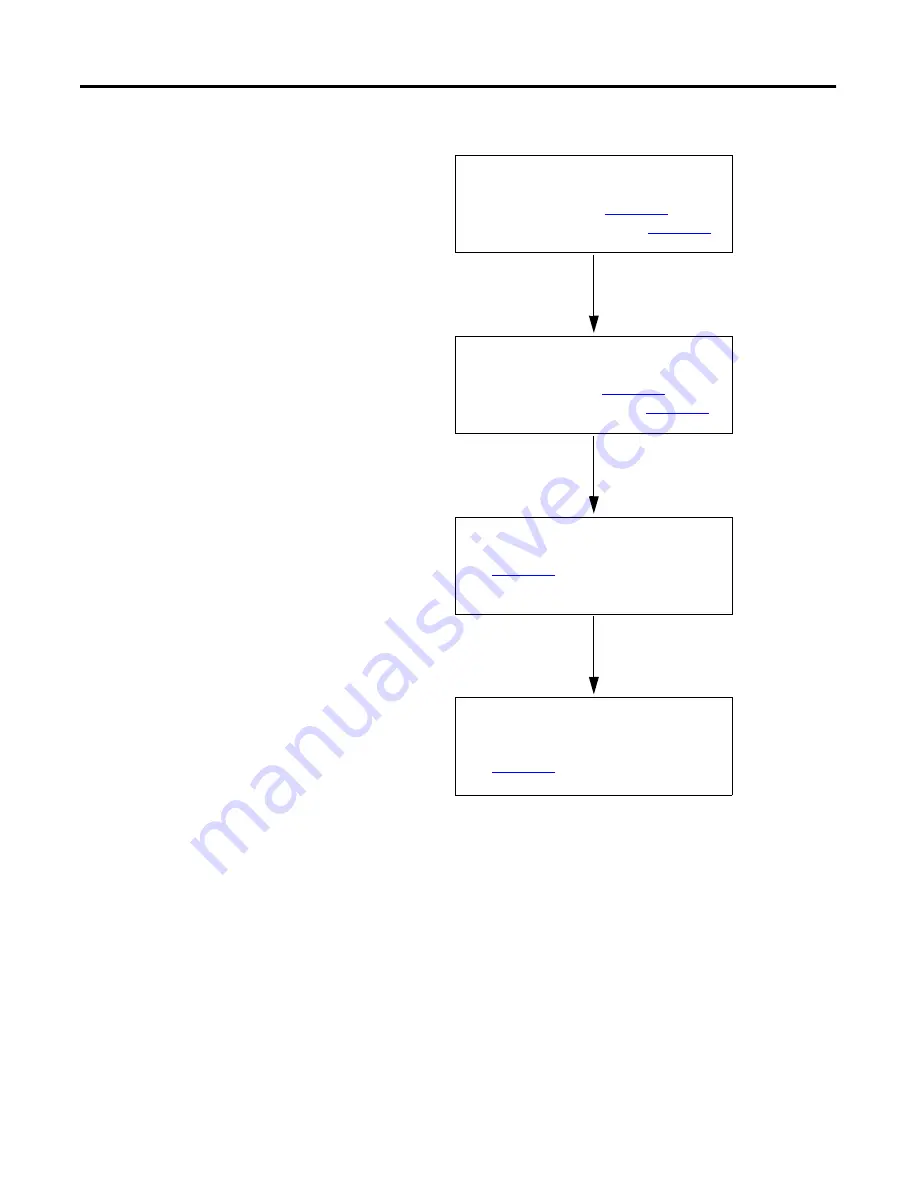
Publication 1734-UM015A-EN-E - November 2009
Introduction
13
Quick Start - Prepare the
Modules to work on
EtherNet/IP and ControlNet
Mount the Module
For POINT I/O, see
For ArmorPOINT I/O, see
.
Wire the Module
For POINT I/O, see
.
For ArmorPOINT I/O, see
.
Add Module to RSLogix 5000
See
Write the DeviceLogix Program in
RSNetworx for DeviceNet
See
Summary of Contents for 1734-8CFGDLX
Page 6: ...Publication 1734 UM015A EN E November 2009 4 Table of Contents Notes ...
Page 10: ...Publication 1734 UM015A EN E November 2009 8 Preface Notes ...
Page 16: ...Publication 1734 UM015A EN E November 2009 14 Introduction Notes ...
Page 109: ...Publication 1734 UM015A EN E November 2009 Peer Data Maps 107 Notes Allen Bradley HMIs ...
Page 110: ...Publication 1734 UM015A EN E November 2009 108 Peer Data Maps Notes ...
Page 111: ...Allen Bradley HMIs ...