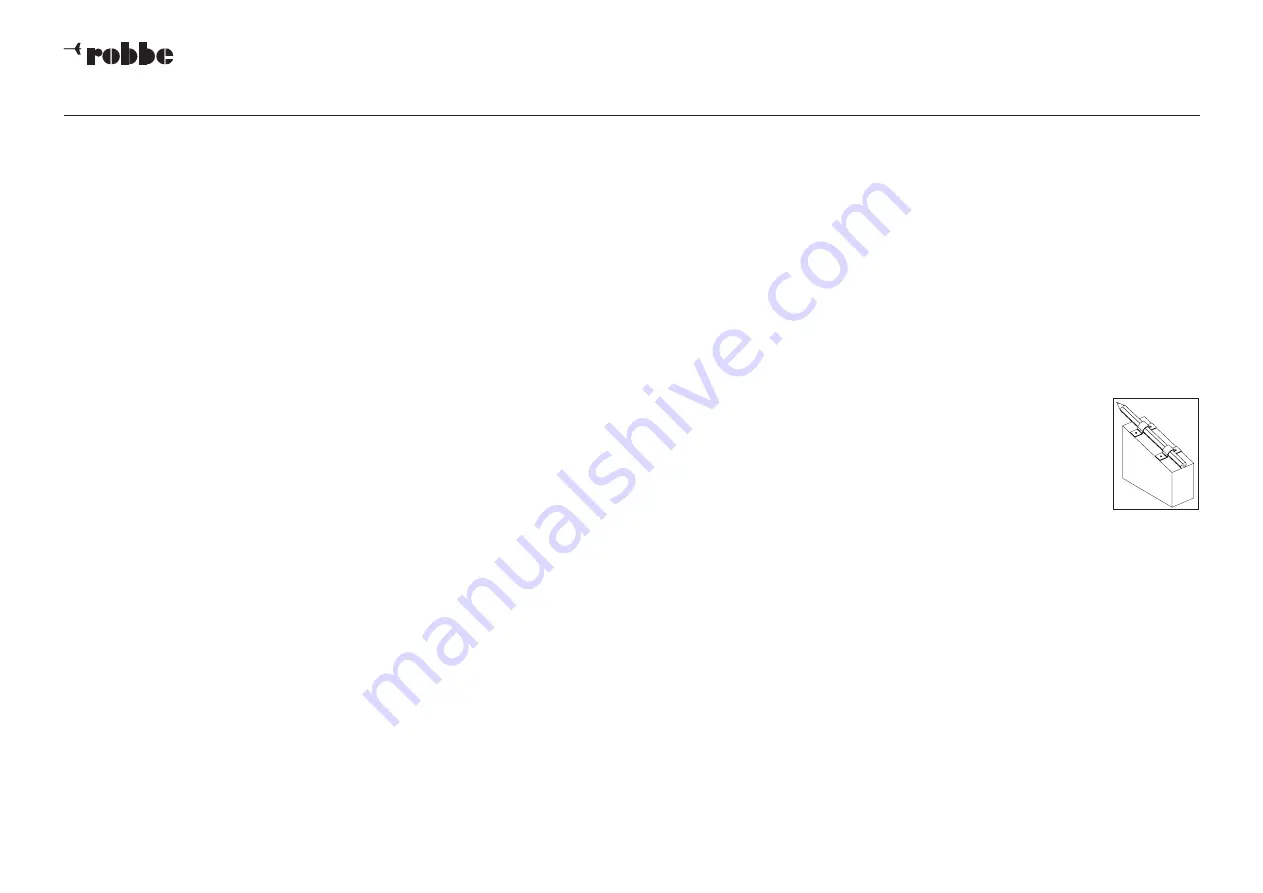
3
to paint areas of different colour separately. This means: every
individual component which is to be a different colour should
first be trimmed to fit on the boat, then painted, and only then
glued or screwed to the model.
If any part is to be painted in multiple colours, then the different
areas should be masked out using Tesafilm (clear adhesive
tape) or PVC tape - don't use paper masking tape. The tape
must be removed again when the new paint is just dry to the
touch.
Where painted parts are to be glued to the model, sand the
painted surface before applying glue.
For painting this model we recommend acrylic-based or syn-
thetic enamel paints exclusively.
If you wish, you can finish the model in the colour scheme
shown in the kit box illustrations.
Marking the waterline, painting the model
Since the Construction Water Line (CWL)
also represents the dividing line between the
upper hull and the lower hull colours, it must
be marked on the hull before painting.
It is best to prepare the jig shown in the draw-
ing for marking the waterline.
The position of the waterline is stated in the drawing.
Place the hull in the boatstand and weight it down to prevent
it shifting.
Now pack up the boatstand so that the CWL points marked at
the bow and stern are the same height above the bench; it is
best to check this with a steel ruler. Set the jig to the correct
height, and move it round the hull to mark the waterline all
round.
Radio control system
A two-channel radio control system is all you need to operate
the model.
We recommend that you install the specified RC components.
Study the instructions supplied with the equipment before
using it for the first time.
Electrical connections must be secured inside the hull in such
a way that they cannot come into contact with any water which
penetrates the model.
Wait until glued joints have set hard before filling exposed
joints and sanding smooth.
Glued joints
Use the recommended adhesives only.
Always observe the instructions provided by the adhesive ma-
nufacturers.
All parts must be trial-fitted “dry” (without glue) before you re-
ach for the adhesive.
When using Stabilit-Express, spread the adhesive out thinly
rather than applying thick beads of glue.
All glued joints involving the hull at which there is a danger
of water penetration (rudder bush, stern tube etc.) must be
sealed carefully with a fillet of Stabilit-Express.
Hold parts together with clamps or strips of adhesive tape after
applying the glue.
Small quantities of cyano-acrylate can be applied using a pin
or a length of thin wire.
Soldering
When soldering joints involving the railing stanchions and simi-
lar parts, always use a hot iron and apply it for the minimum of
time, otherwise there is a danger of heat-damage to the adja-
cent plastic parts (superstructure, platforms etc.). An alternati-
ve method is to prepare a simple jig for bending and soldering
the individual railing sections.
Clean up all soldered joints carefully. All metal parts must be
rubbed down with fine abrasive paper and de-greased before
they are painted. Use heat-shrink sleeves to insulate soldered
joints involving connectors and cables.
Painting the model
It is left up to the builder to decide when to paint the individual
components.
Any gaps between individual plastic parts can be made good
using a plastic filler paste, e.g. robbe rostuff-micro. Sand filled
areas smooth when dry.
When plastic parts are to be painted, clean the surfaces with
white spirit (not cellulose thinners), and then avoid touching
them again. Before painting the hull we recommend giving it
a coat of primer and rubbing down with fine abrasive paper.
If you wish to obtain a neatly delineated paint job, it is essential
General notes on construction
The vacuum-moulded parts
Use abrasive paper to sand the cut edges smooth after trim-
ming the vacuum-moulded parts.
Drill holes in the vacuum-moulded parts at the marked points,
and in the positions indicated in the illustrations.
The parts in the machine-cut sheets
This kit contains machine-cut sheets containing model com-
ponents.
The parts are joined to the sheets by small lugs, to prevent
them falling out in transit. They can easily be removed using a
chisel or a sharp balsa-knife.
It is best to leave the parts in the sheets until you need them for
the stage in hand; this makes it easier to identify the remaining
parts.
These instructions include an A4 sheet showing reduced-scale
drawings of the machine-cut sheets and the stage numbers for
which they are needed.
The machining process produces "radii" (rounded areas) on
internal corners. In some cases it is necessary to remove the-
se rounded corners using a needle file or a sharp knife. These
areas are indicated by an exclamation mark (!) in the drawings.
The individual sub-assemblies from each stage should be trial-
fitted “dry” (no glue) beforehand, both to check that the parts
are correctly positioned, and that they fit together neatly.
As most of the curved shapes require fine adjustment, the
projecting tongues are designed to have a little play in the
matching slots. This is useful when completing complex sub-
assemblies, but does mean that you have to be very accurate
when aligning external contours.
This method of construction inevitably leaves small gaps; the-
se can be used to tack the parts together with small quantities
of cyano.
When joining parts at an angle to each other, it is important to
ensure that their contact surfaces mate accurately, as errors
are cumulative, and the result may be that it is difficult to install
subsequent sub-assemblies in the correct position.
The sequential numbering of the stages of assembly is inten-
ded to help you when installing the parts. This is not always
100% true, but still forms a useful guideline.
Building instructions - PAULA IV
No. 1198
Notice de construction PAULA IV
réf. 1198
Istruzioni di montaggio PAULA IV
No. 1198