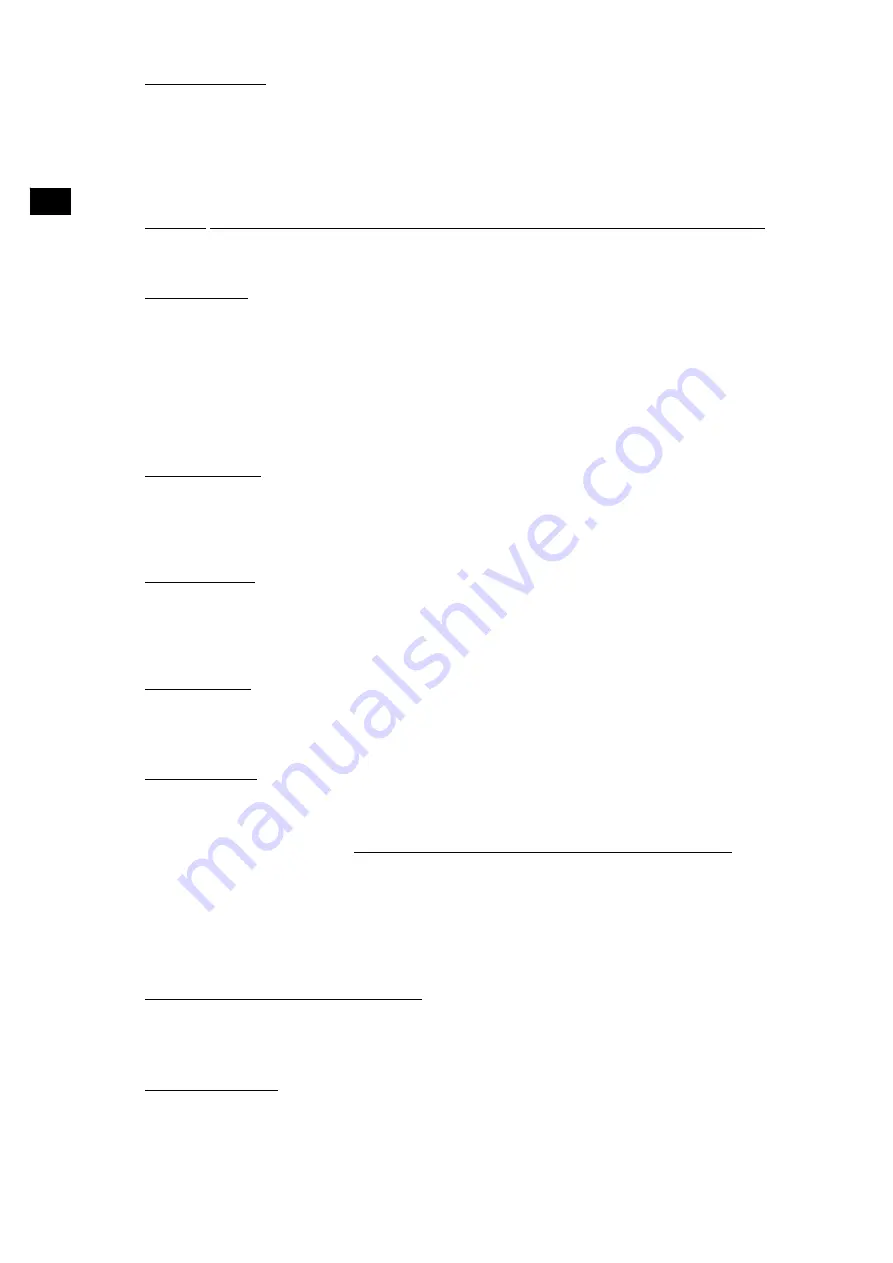
MH TH
Pag. 18
REV. 08 11/07
UK
5. 6
Refrigerant charge
After the vacuum-setting operation, the system must be loaded with the type of refrigerant stated on
the label or with one of the alternative types allowed. To charge the refrigerant correctly, we
recommend that, after setting the vacuum, you pump part of the refrigerant into the compressor to
“break the vacuum”. Then start the compressor so that it sucks up the residual part of the
refrigerant.
For the correct calculation of the gas charge, connect gauges to the pressure inlets (already fitted).
Pressure values must be compatible with the operating conditions of the machines.
Important:
mixtures of refrigerating gas must be charged into the system in their liquid state only.
Loading operations must be carried out by specialised technicians only.
For charging, recovering or checking the refrigerant, use gloves to protect against low temperatures.
5. 7
Leakage checks
A system can operate correctly over time and for the entire duration of the compressor only if all
instructions for a correct installation are followed. These include the absence of refrigerant leaks. It
has been estimated that leaks of 10% of the refrigerant load during 15 years of compressor
operation still guarantee a good level of operation of the refrigerating system. With the new types of
gas (R134a, R404a and mixtures) the possibilities of refrigerant leaks through welding or
connections that have not been carried out correctly increase because of the reduced molecular
dimensions of these gas. For these reasons, it is very important that welding is checked for leakage
using methods and equipment that are suitable for the type of refrigerant in use.
5. 8
Crankcase heater
Whenever the compressor operates in ambient temperatures of less than +5°C, it is compulsory to
use a crankcase heater in order to avoid the build-up of liquid in the lower side of the compressor
during stoppages. Furthermore, it is necessary to choke the condenser, for example, by reducing its
air capacity (i.e.: by means of a speed regulator).
5. 9
Operating cycles
•
The system has to be sized so as not to have more than 5 on/off cycles per hour.
•
The intervention of the Thermal/Amperometric protection device switches off the compressor,
which will be started again after the time required for the protection device contacts to be
connected.
5. 10
Operating times
•
The systems must be sized for max. 80% of standard compressor operation.
•
100% compressor operation only occurs in special overload and ambient temperature conditions
that are outside of the normal permitted operating limits.
5. 11
Pressure switches
•
All machines are equipped with HBP safety pressure switches set at max. 28 bar.
•
LBP safety pressure switches are set according to the gas in use and the compressor application.
We recommend using the value stated in the following table:
Gas
°C=[bar]
Set
Differential
LBP Application MBP
R404A
-25°C=1.5 bar
3 bar
1.5 bar
(medium
temp.)
R407C
-25°C=0,8
bar
2.3
bar
1.5
bar
LBP Application LBP
R404A
-46°C=0 bar
3 bar
3 bar
(low temp.)
5. 12
Pressure relief valves on the liquid receiver
•
The machines in risk “category 0” are not equipped with pressure relief valves.
•
The machines in risk “category
≥
1” are equipped with pressure relief valves.
The risk category of each model is stated on its identification label.
5. 13
Electrical installation
The electrical installation must be performed by qualified staff with the relevant technical skills
according to the requirements of the country where the machine is installed.
•
Fit a thermomagnetic switch with a type-C intervention curve (10-15 In) between the power
supply line and the machine-board electrical panel (optional item) and make sure that the mains
Summary of Contents for MH-HT
Page 2: ...MH TH Pag 2 REV 08 11 07 ...
Page 67: ...MH TH Pag 67 REV 08 11 07 ...
Page 69: ...MH TH Pag 69 REV 08 11 07 ...
Page 70: ...MH TH Pag 70 REV 08 11 07 ...
Page 71: ......