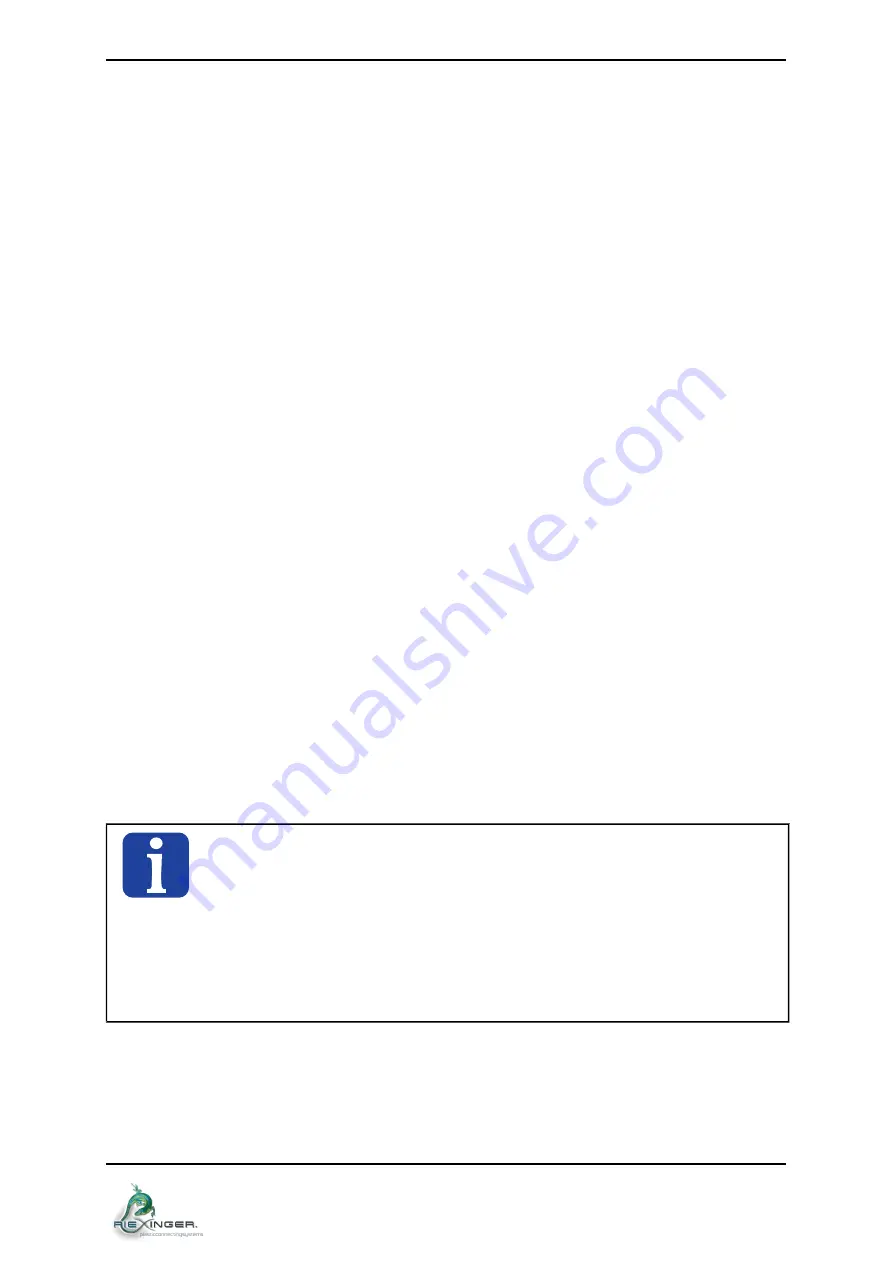
54
9. Maintenance
Saw band runs from diversion 1 wheel inwards
1) Loosen locking screws E
2) Turn the adjusting screws B and D a bit.
3) The plate tilts slightly.
4) Fasten locking screws E.
5) Turn diversion wheel 1 several times by hand to control the running behavior of the saw
band.
6) If necessary repeat the steps 1 to 5.
Sawband runs from diversion wheel 1 outwards
1) Loosen locking screws E
2) Turn the adjusting screws A and C a bit.
3) The plate tilts slightly.
4) Fasten locking screws E.
5) Turn diversion wheel 1 several times by hand to control the running behavior of the saw
band.
6) If necessary repeat the steps 1 to 5.
Sawband runs from diversion wheel 3 inwards
1) Adjust screws A and B.
Sawband runs from diversion wheel 3 outwards
1) Adjust screws C and D.
Information
l
Please note that the adjustments always have an interaction with the other
wheels. Most minimal changes are already successful.
l
After completing the adjustments always counter set screws and tighten
the fixing screws E.
l
To protect your machine check the running behavior always initially by
manually moving the saw blade.
BSM 630
Summary of Contents for BSM 630
Page 2: ...Status 11 2015 Eugen Riexinger GmbH Co KG...
Page 6: ......
Page 24: ......
Page 34: ......
Page 42: ......
Page 62: ...60 9 Maintenance Date Activity Next maintenance Name BSM 630...
Page 68: ...66 11 Annex BSM 630...
Page 69: ...11 Annex 67 11 4 Circuit diagram BSM 630...
Page 70: ......