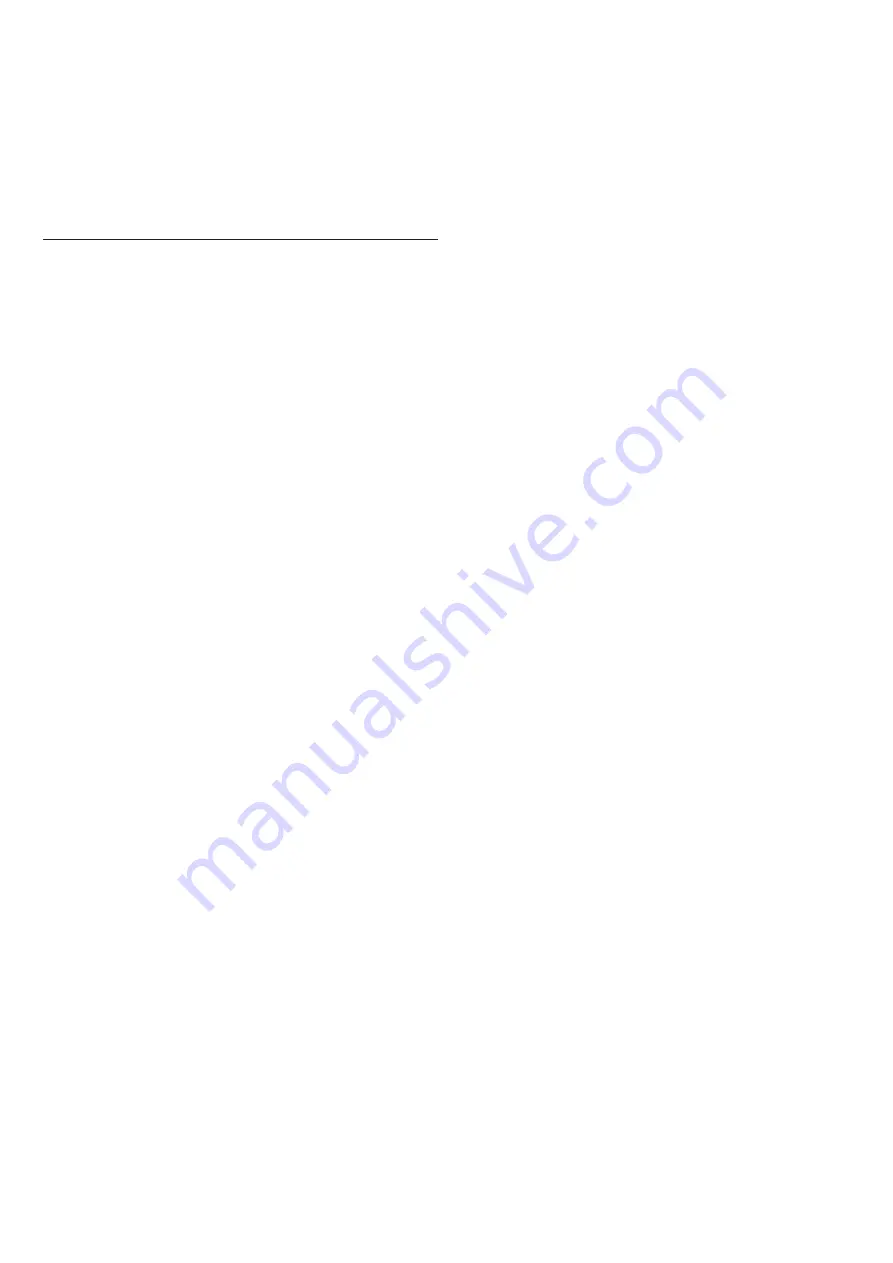
67
at 2.5Nm.
− Check the position of the electrode against the burner, as well
as the distance of the ignition electrode wires (refer to the
picture).
− Adjust the electrode gap if necessary.
Reassemble the burner door set on the heat exchanger
respecting a torque wrench of the four nuts at 5Nm.
13.4.5
Heat exchanger
MANDATORY:
Check that combustion chamber is free of deposits
and, proceed to clean.
9
WARNING:
before cleaning remove the siphon connection
pipe from the condensate drain connection of the exchanger
and connect a temporary collection pipe to it.
- Vacuum the combustion residue.
- Clean with a nylon brush.
9
WARNING:
use a nylon brush only. DO NOT use a metallic
brush, which can damage the heat exchanger.
− Vacuum the remaining residue.
− Rinse with water.
9
WARNING:
DO NOT rinse the insulation panel.
NOTICE:
in case of serious dirt build-up rinsing can be repeated
several times, spray white vinegar and wait about 3 to 5 minutes,
clean with a mechanical nylon brush and rinse with water.
9
WARNING:
DO NOT spray and rinse the insulation panel.
−
MANDATORY:
check the insulation panel and, if it is worn, it
must be replaced
9
WARNING:
the materials use in the heat exchanger do
not require individual protection devices but, for safety,
we recommend the use of a protective mask, gloves and
glasses.
9
WARNING:
during operation, protect the lower part of the
internal coils of the heat exchanger to avoid that dust and
parts of the insulation panel fall off within them.
To replace the insulation
− Use a blade to cut the insulation panel approximately 2 1/2”
(60 mm) from the circumference.
− Lift and remove the 2 panel pieces from the seat.
NOTICE:
The insulation panel is fixed by a central clip and six
radial clips; if during removal the clips detach, remove them
from the combustion chamber.
− Vacuum any material residue present on the exchanger coils
and panel support.
− Position the new insulation panel close its seat and insert it
completely by pressing on the central part.
−
MANDATORY:
Check the flue outlet gasket and, if it is worn, it
must be replaced.
− Reassemble the burner door set on the heat exchanger
respecting a tightening torque of the four nuts at 5Nm.
9
WARNING:
Ensure the burner door is sealed properly;
preventing flue gases from escaping. Failure to do so may
result in substantial property damage, severe injury or
death.
Summary of Contents for Family PRO 42 IS
Page 75: ...75 ...