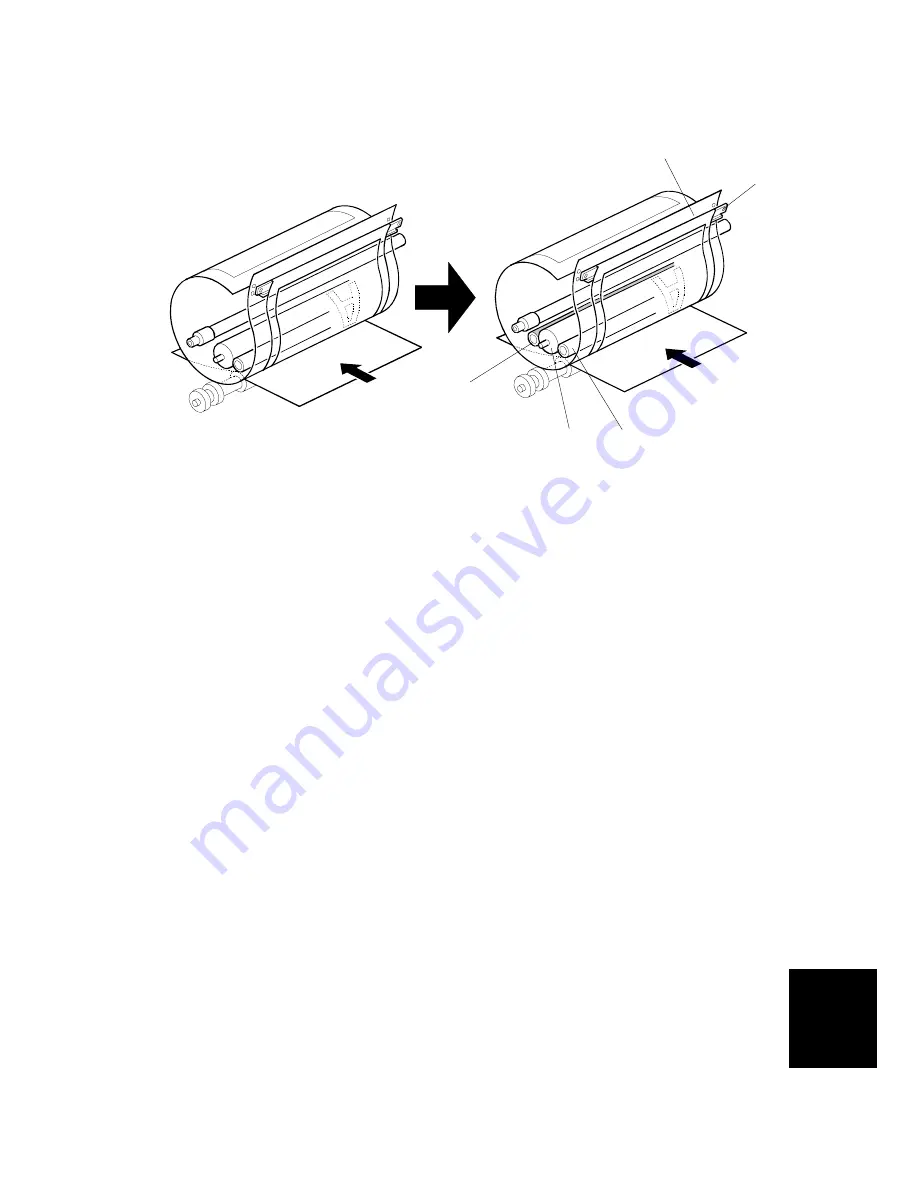
DRUM
SM 6-31 C264
C26
4
6.6 DRUM
6.6.1 OVERVIEW
•
The drum idling roller [C] ensures that the first print has sufficient ink density if
the machine was not used for a long time.
Procedure
Ink is supplied inside the drum, through the drum shaft.
↓
The ink roller [A] and the doctor roller [B] spread the ink evenly on the screens.
The drum idling roller [C] supplies ink to the screens and master before and after
printing.
↓
Ink passes through the metal screen [D].
↓
Ink passes through the cloth screen [E].
↓
Ink passes through the holes in the master that were made by the thermal head.
↓
Ink reaches the paper.
NOTE:
1) The drum is driven by the main motor and turns only clockwise.
2) The main motor speed and the drum stop positions are controlled by
monitoring the motor encoder.
3) The ink pump, which is outside the drum, supplies ink from the ink
cartridge to the drum through the drum shaft.
[A]
[B]
[C]
[D]
[E]
Summary of Contents for C249
Page 1: ...C249 C264 SERVICE MANUAL 001780MIU...
Page 2: ......
Page 3: ...C249 C264 SERVICE MANUAL...
Page 4: ......
Page 5: ...C249 C264 SERVICE MANUAL 001780MIU...
Page 6: ......
Page 8: ......
Page 10: ......
Page 12: ......
Page 18: ...C249 C264 vi SM PRINTER SCANNER C624 SEE SECTION C624 FOR DETAILED TABLE OF CONTENTS...
Page 20: ......
Page 21: ...INSTALLATION...
Page 22: ......
Page 45: ...PREVENTIVE MAINTENANCE...
Page 46: ......
Page 49: ...REPLACEMENT AND ADJUSTMENT...
Page 50: ......
Page 96: ......
Page 97: ...TROUBLESHOOTING...
Page 98: ......
Page 114: ......
Page 115: ...SERVICE TABLES...
Page 116: ......
Page 145: ...DETAILED DESCRIPTIONS...
Page 146: ......
Page 208: ......
Page 209: ...SPECIFICATIONS...
Page 210: ......
Page 215: ...C264...
Page 216: ......
Page 224: ......
Page 239: ...INSTALLATION PROCEDURE SM 1 13 C264 C264 Installation Procedure 1 Remove the strips of tape...
Page 261: ...SCANNER SM 3 5 C264 C264 B SBU x 1 x 5 C Lamp stabilizer x 2 x 5 B C...
Page 322: ......
Page 354: ......
Page 358: ...MECHANISM OVERVIEW C267 6 4 SM 62 60 61 64 65 66 67 63 69 70 68 71 72...
Page 409: ...TIMING CHART SM 6 55 C264 C264 6 11 TIMING CHART 6 11 1 MASTER EJECTION...
Page 425: ...DOCUMENT FEEDER C600...
Page 426: ......
Page 428: ......
Page 446: ......
Page 447: ...PRINTER CONTROLLER C624 SERVICE MANUAL PARTS CATALOG...
Page 448: ......
Page 450: ......
Page 483: ...C624 PARTS CATALOG...
Page 484: ......