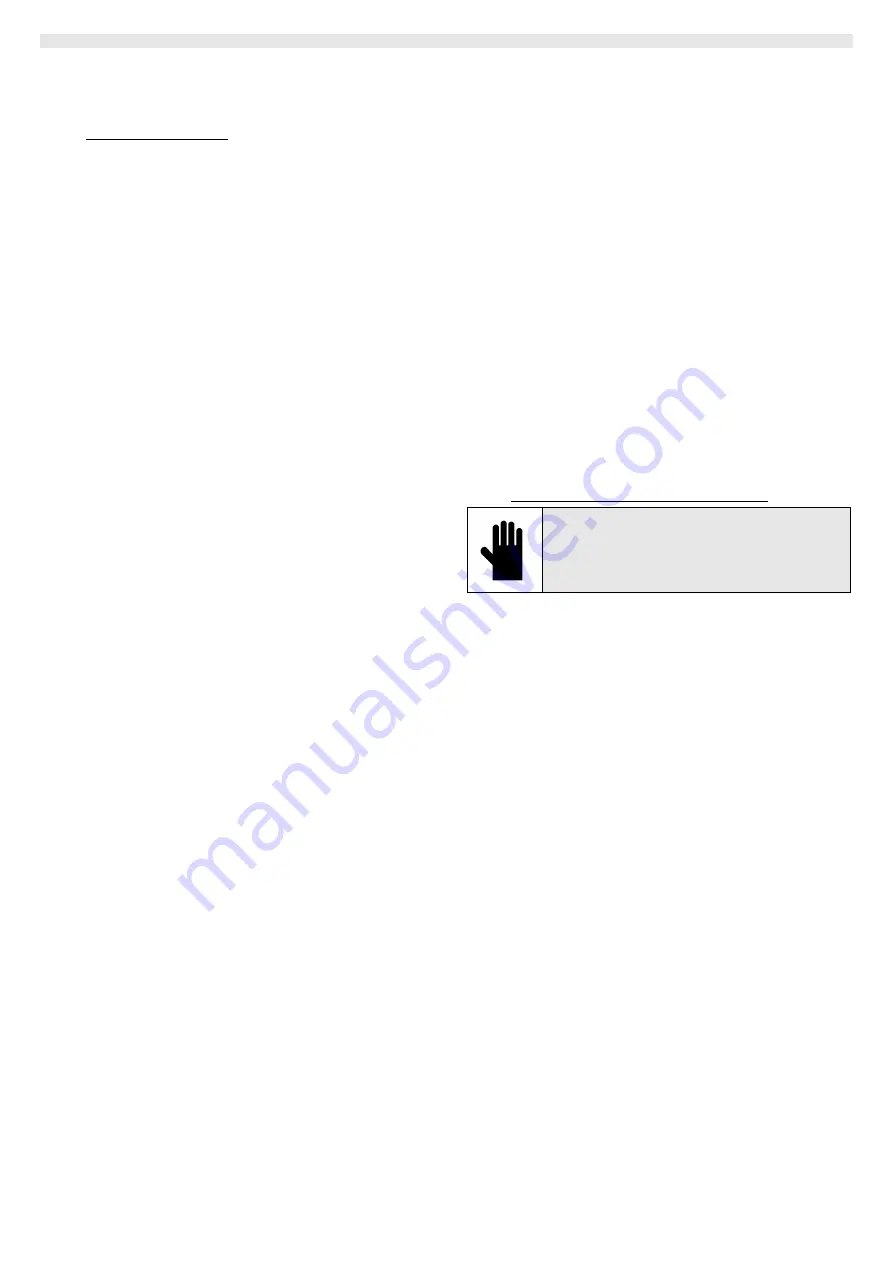
SECTION II: INSTALLATION AND MAINTENANCE
28
II SECTION II: INSTALLATION AND
MAINTENANCE
II.1 UNIT
DESCRIPTION
II.1.1 CONSTRUCTION
FEATURES
○
Peraluman load bearing structure and panels, zinc-plated steel bed,
soundproofed compressor compartment.
○
1 x hermetic Scroll rotating compressor complete with internal
thermal protection and internal safety valve.
○
Water-side plate type heat-exchanger in brazed stainless steel
complete with antifreeze element, insulation in expanded polyurethane
and air bleed valve inside the machine.
○
Air-side copper-pipe and aluminium-finned coil heat exchanger,
complete with protection grille.
○
Directly coupled, centrifugal type motor-driven fan, fitted with internal
thermal protection, vertical condensation and evaporation air delivery
and complete with protective grilles.
○
Male threaded hydraulic connections.
○
Differential pressure switch to protect the unit from possible
interruptions in water supply.
○
Refrigerant circuit made from annealed copper piping (EN 12735-1-
2) complete with: drier filter, load connections, safety pressure switch
with manual reset on high pressure side, bleed valve (30barg), pressure
switch with automatic reset for pressure control on low side,
liquid/humidity indicator, thermostatic expansion valve (x 2 for THCE),
cycle inversion valve (for THCE), liquid receiver with safety valve (for
THCE) and non-return valves (x 2 for THCE).
○
The T version is complete with storage tank, expansion vessel
calculated for the quantity of water present inside the machine
(maximum working pressure 3 bar, pre-charge 1 bar, capacity 7l),
safety valve 3 bar, drainage valves (provided, to be installed), manual
bleed valve, pump (121 T-126 T), circulating pump (114 T-117 T) or
high static pressure pump (114 H-117 H).
○
Unit complete with:
•
condensation collection tray (for THCE);
•
R407C refrigerant charge;
II.1.2 ELECTRIC
PANEL
○
Electric panel accessible by removing the upper left-hand side cover;
can be opened and closed with a suitable tool, in compliance with
current IEC norms
○
Complete with:
•
electrical wiring arranged for power supply
400V-3ph+N-50Hz;
•
auxiliary power supply 230V-1ph-50Hz drawn from the main power
supply;
•
general isolator, complete with door interlocking isolator;
•
Automatic compressor protection switch;
•
protection fuse for auxiliary circuit;
•
Fan protection fuse
•
Integral compressor protection fuse (121-126).
•
compressor power contactor;
•
remote unit control.
○
Programmable electronic board with microprocessor, controlled by
the keypad installed on the machine. This electronic board performs the
following functions:
•
Regulation and management of the inlet water temperature set
points; of cycle reversal (for THCE); of the safety timer delays; of the
circulating pump; of the compressor and pump hour-run meter; of the
defrost cycles (for THCE); of the electronic anti-freeze protection which
cuts in automatically when the machine is switched off; and of the
functions which control the operations of the individual parts making up
the machine;
•
complete protection of the unit, automatic emergency shutdown and
display of the alarms which have been activated;
•
compressor protection phase sequence monitor;
•
unit protection against low or high three-phase power supply
voltage;
•
display of programmed set points, of inlet/outlet water temperatures
and of alarms, on the display; of cooling/heating mode (for THCE) by
LED; of the electrical voltage values present in the three phases of the
power circuit that powers the unit;
•
self-diagnosis with continuous monitoring of the functioning of the
unit;
•
user interface menu;
•
alarm history management (if KTR accessory present, menu
protected by manufacturer password). The following is memorized for
each alarm:
•
date and time of intervention (if the KSC accessory is present);
•
alarm code and description;
•
inlet/outlet water temperatures when the alarm intervened;
•
the condensation pressure values when the alarm intervened (if the
KFI accessory is present);
•
alarm delay time from the switch-on of the connected device;
•
status of the compressor and fan when the alarm intervened (if the
KFI accessory is present, the analogue output status is displayed);
○
Advanced functions:
•
configured for serial connection (KRS 485, KFTT10, KRS232 and
KUSB accessory);
•
configured for management of time bands and operation
parameters with the possibility of daily/weekly operating programs (KSC
accessory);
•
check-up and monitoring of scheduled maintenance status;
•
testing of the units assisted by computer;
•
self-diagnosis with continuous monitoring of the functioning of the
unit.
II.2
SPARE PARTS AND ACCESSORIES
IMPORTANT!
Only use original spare parts and accessories.
RHOSS
S.p.A. shall not be held liable for damage
caused by tampering or work carried out by
unauthorised personnel or malfunctions caused by
the use of non-original spare parts or accessories.
KSA
- Rubber anti-vibration mountings.
KFI
- Low ambient control for pressurized and continuous regulation of
the fan rotation speed down to an external air temperature of -9°C in
cooling mode, and up to an external air temperature of 30°C in heat-
pump mode.
KTR
- Remote keypad for remote control, with rear illuminated LCD
display.
KSC
- Clock card for displaying date/time and regulating the machine
with daily/weekly start/stop time bands, with the possibility to change
the set-points. The settings can be made using the remote keypad
(KTR) or by the supervisor.
KRS485
- RS485 serial interface for logical dialogue with building
automation and supervision systems (Protocols supported: proprietary
protocol; Modbus
®
RTU).
KFTT10
- FTT10 serial interface for connection to Lonworks
®
compatible protocol supervision systems.
KR S232
- RS485/RS232 serial converter for connection to supervision
systems, to be combined with one or more KRS485 serial interface
modules if the units are managed on a centralised basis.
KUSB
- RS485/USB serial converter for connection to supervision
systems, to be combined with one or more KRS485 serial interface
modules if the units are managed on a centralised basis.
KAA
– Storage tank anti-freeze heating element (factory fitted )
US
– Horizontal condensation/evaporation air delivery (factory fitted)
KRAS
– Inlet anti-vibration connection.
KRMA
– Outlet anti-vibration connection.
Description and fitting instructions are supplied with each
accessory.
Summary of Contents for MICROSYSTEM TCCE 114 H Series
Page 109: ...NOTE 109 NOTE...
Page 110: ...NOTE 110 NOTE...
Page 111: ...Codice Variante Data emissione Modifica H50804 09 11 05 Nuova edizione...