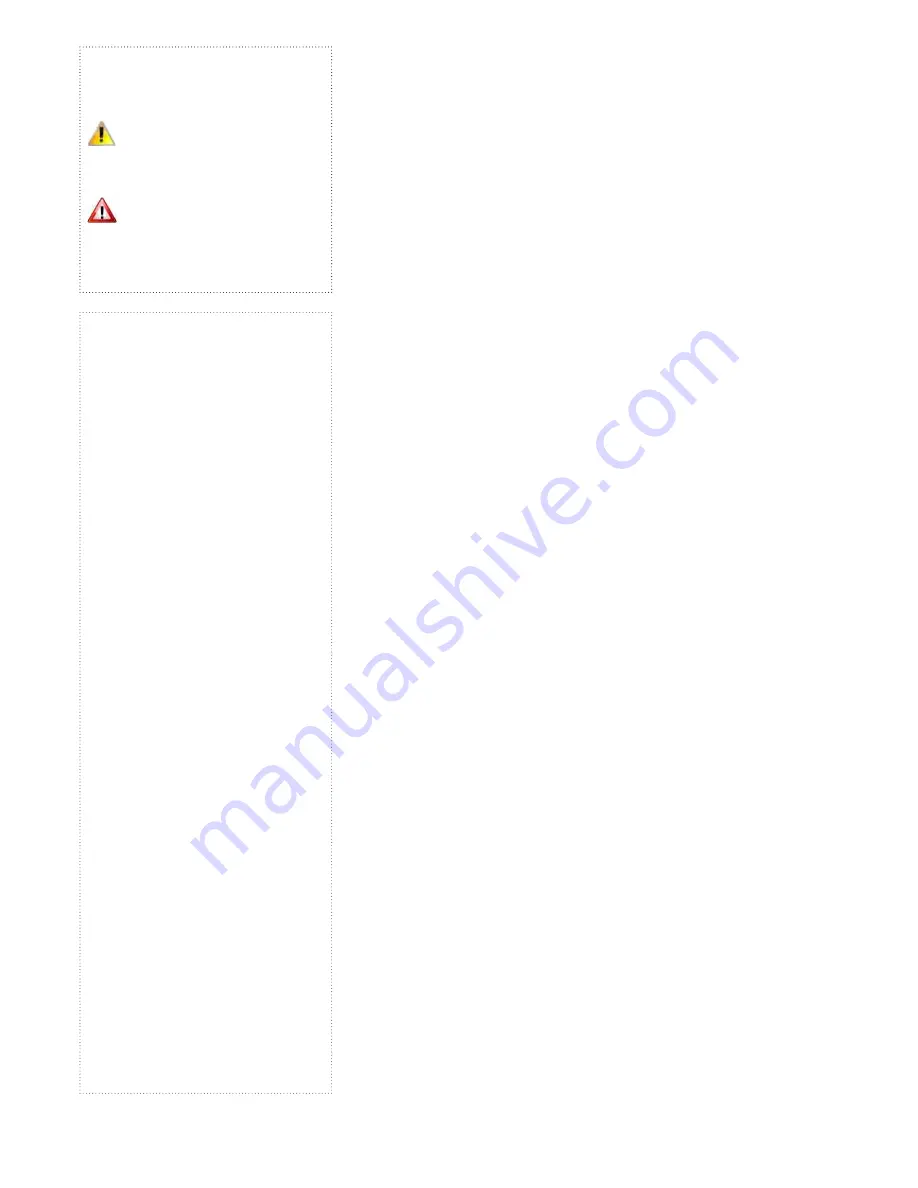
1.2 Compliance notices
The Warm Air Heater range detailed here-
with are manufactured within a strictly
controlled quality environment within the
parameters of ISO 9001.
These instructions are only valid if the
following country code is on the appliance
GB. IE. If this code is not present on the
appliance, it is necessary to refer to the
technical instructions which will provide
the necessary information concerning the
modification of then appliance to the condi-
tions of use for the country.
The manufacturer has taken reasonable and
practical steps to ensure that all heaters are
safe and without risk when properly used.
These heaters should therefore only be used
in the manner and purpose for which they
were intended, and in accordance with the
recommendations detailed herewith. The
manufacturer supports all new products
being supplied to their customers with
a comprehensive information pack; this
clearly defines mandatory instructions for
the safe installation, use, and maintenance,
of the appliance(s).
Where proprietary items are incorporated
into any of the Heaters, detailed information
and instructions are also provided as part of
the information pack. It is the responsibility
of the installer, owner, user, or hirer of Warm
Air Heater to ensure that they are familiar
with the appropriate information/manu-
als supplied by the manufacturer and the
safety instructions. In addition, operators
must be suitably trained in the use of the
appliance so as to ensure its continued safe
and efficient use.
The manufacturer has a commitment to
continuous improvement and therefore
reserve the right to amend or change the
specification of Warm Air Heater subject to
compliance with the appropriate European,
national and local regulations
1.3 Warranty
The heater is supplied with a 1 year parts
and labour warranty and a further year on
all parts excluding consumables.
The warranty commences from the date
of dispatch from the manufacturer, and
is subject to the terms detailed within the
Manufactures ‘conditions of business’.
Note:
The warranty may be invalidated if:
• The installation is not in accordance with
the general requirements of this manual.
• The flue arrangement and air supply for
the heater are not in accordance with the
manufacturers recommendations, codes of
practice, or similar standards.
• Air flow through the heater is not in
accordance with the manufacturers
technical specifications.
• Internal wiring on the heater has been
tampered with or unauthorised service or
repairs undertaken.
• The main electrical supply input to the
heater has been interrupted during the
heating mode.
• The heater has been subject to and affected
by the ingress of water in any form.
• The heater is not operated at the rating(s)
laid down in the manufacturers technical
specifications.
• The heater has not been operated or used
within the normal scope of its intended
application.
• The manufacturer’s recommended
minimum service requirements have not
been complied with.
Note:
All warranty claims must contain the following
info to enable processing to take place.
• Heater model
• Heater serial number
• Order reference/date of order, together with
full installation details (name and address)
• Details or symptoms of fault
• Installers name and address
• Commissioning and service records
Faulty parts must be returned to the supplier,
the address of which is provided at the rear
of this manual. Any such parts will undergo
inspection to verify the claim. Replacement
parts supplied prior to this may be charged,
and a credit supplied upon subsequent vali-
dation of the warranty claim. Consumable
items are specifically not included within
the scope of the warranty.
Note:
Notification is required the immediate moment a
fault is suspected.
The manufacturer will not accept respon-
sibility for any additional damage that has
been caused, expense incurred, or conse-
quential loss resulting from any failure of
the heater(s).
The Warm Air Heater range conforms to the
following standards:
EN 292-1
Safety of Machinery - Basic Concepts, General Prin-
ciples for Design Basic Terminology Methodology
EN 292-2
EN 292-2
Safety of Machinery - Basic Concepts, General
Principles for Design Technical Principles and
Specifications
EN 60204-1
Safety of Machinery - Electrical Equipment for
Machines Specification for General Requirements
EN 60335-1
Safety of Household and Similar Electrical Appli-
ances General Requirements
EN 50165
Electrical Equipment of non-electric heating appli-
ances for household and similar purposes, safety
requirements
EN 55014
Limits and methods of measurement of radio distur-
bance characteristics of electrical motor-operated
and thermal appliances for household and simi-
lar purposes, electrical tools and similar electric
apparatus
EN 1020
Non-domestic forced convection gas-fired air heaters.
Machinery Directive
(2006/42/EC)
Low Voltage Directive
(2014/35/EU)
Electromagnetic Compatibility Directive:
(2014/30/EU)
Regulation (EU)
2016/2281
Gas Appliance Regulations
(EU) 2016/426
Contained within the text of the manual,
the words ‘
Caution
’ and ‘
Warning
’ are used
to highlight certain points.
CAUTION
Caution is used when failure to follow or
implement the instruction(s) can lead to
premature failure or damage to the heater
or its component parts.
WARNING
Warning is used when failure to heed or
implement the instruction(s) can lead to
not only component damage, but also to
a hazardous situation being created where
there is a risk of personal injury.
5