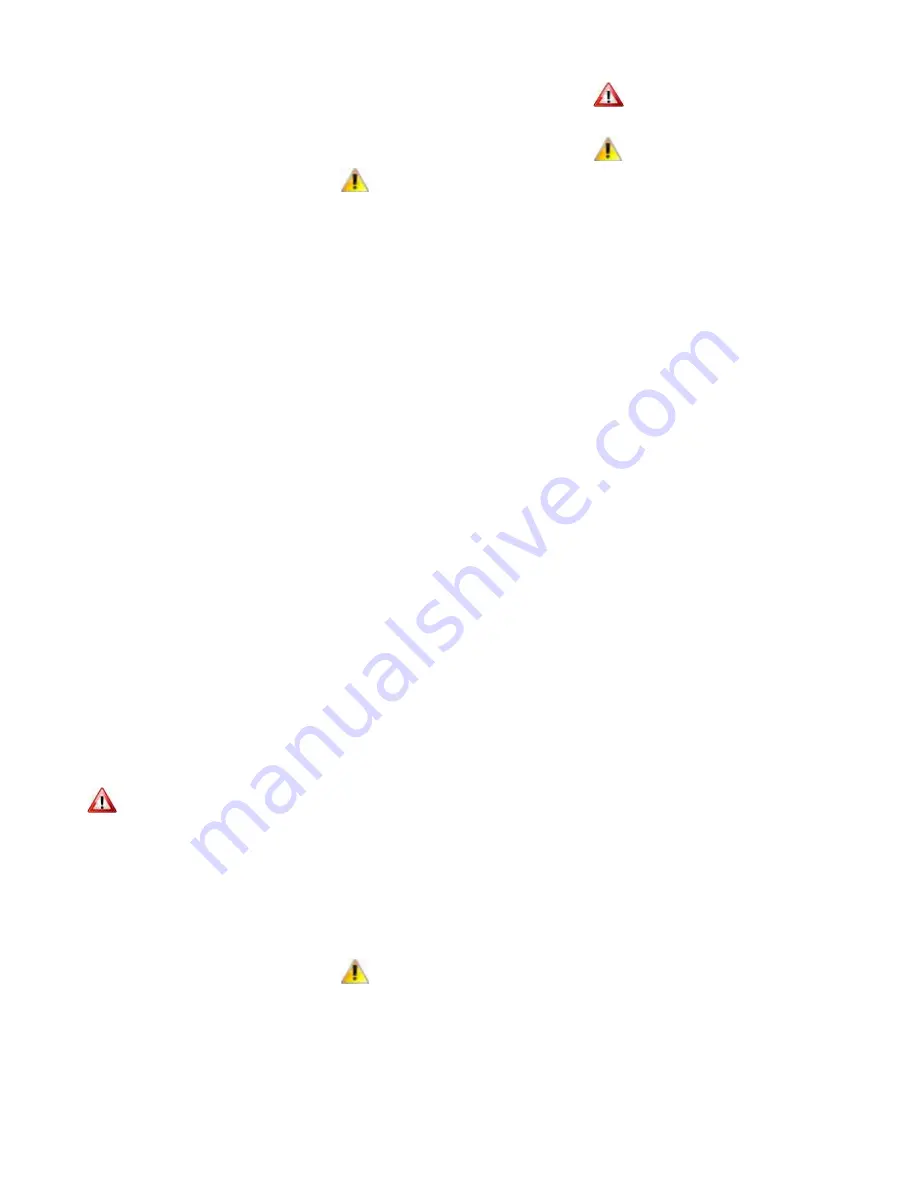
The inlet pump pressure must not exceed a
maximum of 0.4 bar, this is because beyond
this point gas is liberated from the oil.
2.12.1 Storage tank
An externally painted steel storage tank to
BS 799 part 5 or a medium density polyeth-
ylene oil tank OFTEC certified to OFS T-100
may be used. Local, national, European and
fire regulations must also be complied with
and must include:
• A fuel level gauge (not made from glass) a
vent pipe with a diameter greater than that
of the filler and featuring a weatherproof
termination.
• A sludge valve.
• An outlet valve situated at the opposite end
of the tank to the sludge valve.
• A filler pipe connection situated at the
opposite end to the outlet valve.
The size of the storage tank must take
account of the estimated consumption and
any quantity price breaks offered by the oil
supplier. It is preferable to install the tank
outside, however, if this is not practicable
and the tank has to be installed indoors
advice must be sought about its siting, espe-
cially so far as fire regulations are concerned.
If a separate fire resistant chamber cannot be
provided for indoor installations, a catch-
ment pit with a capacity 10% greater than
that of the storage tank must be provided
storage tanks can if necessary be sited on a
roof, but this is subject to special regulations
as well as local authority approval and
compliance with fire regulations, refer-
ence to BS 5410 part 2 & part 1 is strongly
suggested.
It is advisable to leave the tank unpainted
on the inside, but to paint the outside with
a proprietary grade of anti-corrosive paint.
WARNING
A galvanised or open topped tank is strictly
not allowed. All oil storage tanks require
a bund.
The Control of Pollution Regulation (Oil
Storage) 2001 should be consulted prior to
installation.
Single pipe system (gravity feed)
For installations where the oil tank is
200mm or more above the level of the fuel
pump the principle of gravity feed may be
used. The draw off point for the supply to
the burner must not be positioned any lower
than 100mm above the bottom of the tank.
Where a return valve is fitted this must
be tamper proof to prevent inadvertent
operation.
CAUTION
If the valve is closed when the pump is
running the oil pressure can be increased
sufficiently so as to cause damage to the
seals within the pump.
The return oil should be discharged (pref-
erably) through an elbow onto a tank plate
situated within the tank, this should be
positioned so as not to introduce air or air
bubbles into the draw off pipe.
Two pipe system
This is used where the oil storage tank is
lower than the pump.
Access for the fuel feed to the burner should
be via a suitable tapping made in the top
of the tank, and the fuel feed pipe should
extend to not less than 100mm above the
bottom of the tank. A none return valve
with a metal to metal seat should be fitted,
especially if the return pipe work is termi-
nated at a level above the draw off tube. The
non- return valve must be removable for
service and maintenance purposes, and the
return pipe from the pump must therefore
be extended down into the tank to the same
level as the suction pipe.
The presence of a tamper proof isolating
valve fitted within the return pipe is only
required if there is a risk that oil will siphon
out of the tank if the return pipe is discon-
nected at the pump during maintenance or
servicing and if the none return valve has
been omitted.
Pressurised ring main system
This system is used to supply a number of
units from a common storage tank. A booster
pump is used to provide the pressure to
push the oil around the ring main and back
to the tank.
Pressure reducing valves should be fitted on
the delivery pipe to each heater to ensure
that the pressure at the burner pump is less
than 6 psi.
CAUTION
The internal by-pass plug must be removed
from the burner pump when used in a
pressurised ring main application.
2.13 Pipe work and fittings
WARNING
Galvanised or plastic pipe work and fittings
must not be used. (See BS 5410 Part 1)
CAUTION
All joints must be sealed properly, if neces-
sary using PTFE tape or other approved
sealing media. The pipe work must be
effectively sealed so as to prevent the
ingress of air. The fire check valve must be
operated by way of a fusible link posi-
tioned so that it is above the burner.
Note:
It is advisable to check all pipe work prior to
installation to ensure that there is no loose debris or scale
present. The oil feed to each heater must be fitted with
a fire check valve and isolating valve.
Black iron pipes can be hammered to assist
in the removal of these contaminants.
15