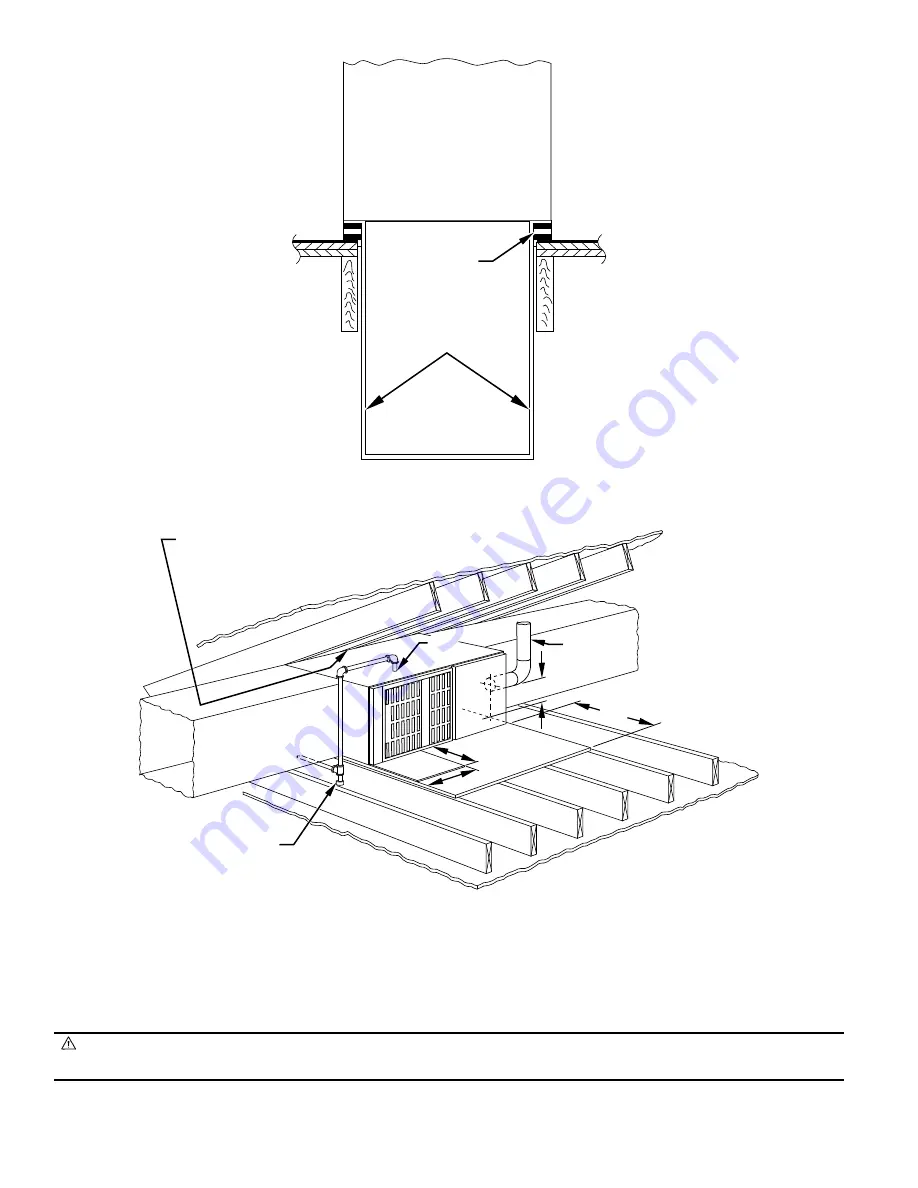
PROCEDURE 6—FILTER ARRANGEMENT
WARNING: Never operate unit without a filter or with filter access door removed. Failure to follow this warning could
result in fire, personal injury, or death.
The 2 factory-supplied filters are shipped in the blower compartment. After the return-air duct has been connected to the furnace, install the filters
in a V-formation inside the return-air plenum. See Fig. 8 and Table 4 for horizontal applications. Horizontal filter retainers must be field supplied.
See Fig. 9 for downflow applications.
Fig. 6—Furnace, Plenum, and Subbase Installed on a Combustible Floor
A78651
DOWNFLOW
SUBBASE
SHEET METAL
PLENUM
FURNACE
(OR COIL CASING
WHEN USED)
Fig. 7—Typical Attic Installation
A82178
30-IN. MIN
WORK AREA
6
″
MIN
FLUE VENT
GAS
ENTRY
24
″
24
″
SHEET
METAL
SEDIMENT TRAP
LINE CONTACT ONLY PERMISSIBLE BETWEEN
LINES FORMED BY INTERSECTIONS OF
THE TOP AND TWO SIDES OF THE FURNACE
JACKET AND BUILDING JOISTS,
STUDS, OR FRAMING.
—8—