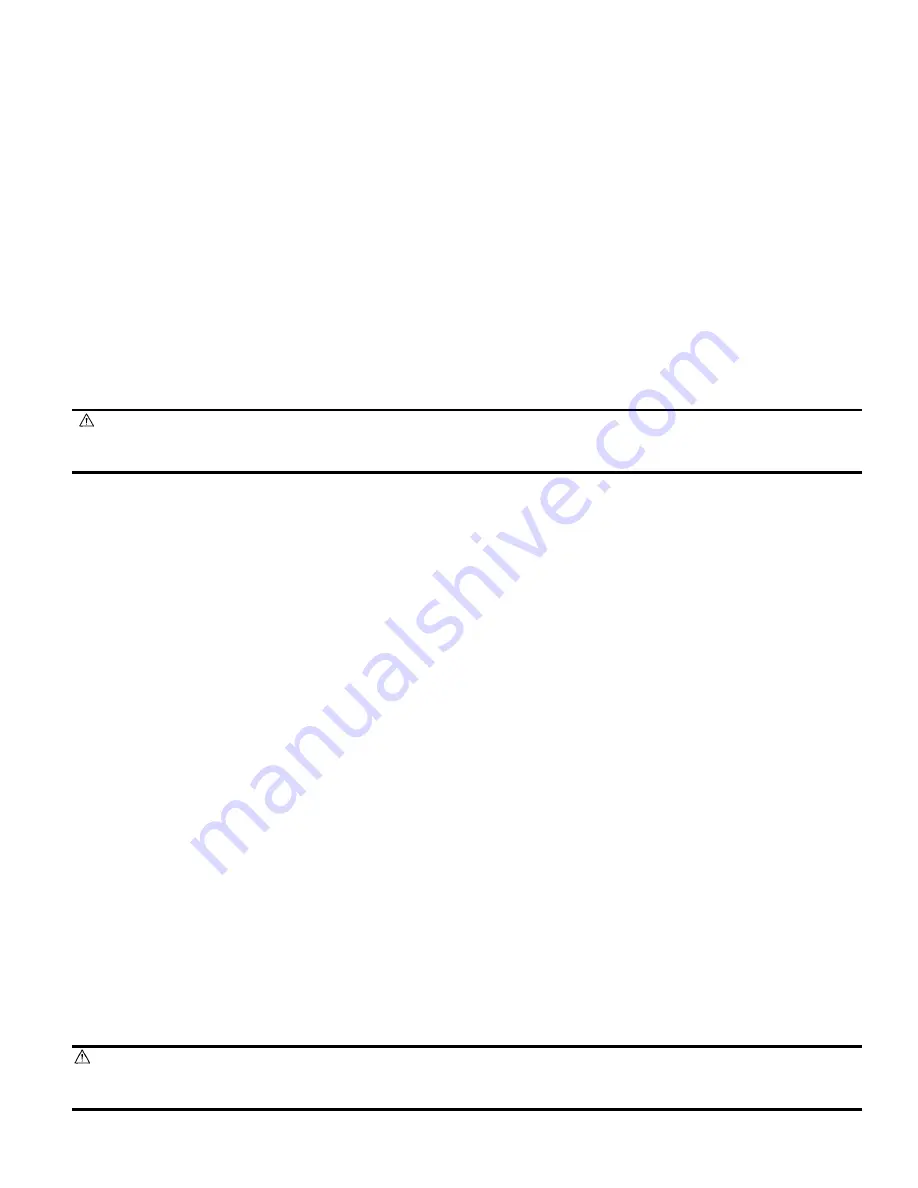
The blower reverts to continuous operation after the heating cycle is completed.
When the thermostat "calls for cooling," the blower operates on cooling speed. When the thermostat is satisfied, the blower operates an
additional 90 sec before reverting back to continuous operation on heating speed.
4. Heat pump mode
When installed with a heat pump, the furnace control automatically changes the timing sequence to avoid long blower off time during
demand defrost cycles. When the W-Y or W-Y-G thermostat inputs are received at the same time, the control changes the blower to heating
speed or starts the blower if it was off, and begins a heating cycle. The blower remains on until the end of the prepurge period, then shuts
off until the end of the ignition warm up and trial for ignition periods (a total of 24 sec). The blower then comes back on at heating speed.
When the W input signal disappears, the control begins the normal inducer post-purge period and the blower changes to cooling speed after
a 1-sec delay. If the W-Y-G signals disappear at the same time, the blower remains on for the selected heating blower off delay period and
the inducer goes through its normal post-purge period. If the W-Y inputs should disappear, leaving the G signal input, the control goes into
continuous blower and the inducer remains on for the normal post-purge period.
Anytime the control senses false flame, the control locks out of the heating mode. This occurs because the control cannot sense the W input
due to the false flame signal and, as a result, sees only the Y input and goes into cooling mode blower off delay. All other control functions
remain in standard format.
NOTE:
EAC-1 terminal is energized whenever blower operates. HUM terminal is only energized when gas valve is energized.
C.
Start-up Procedures
1. Purge gas lines—After all connections have been made, purge the lines and check for leaks.
WARNING: Never purge a line into a combustion chamber. Never use matches, candles, flame or other sources of
ignition to check for gas leakage. Use a soap-and-water solution to check for gas leaks. Failure to follow this warning could
result in fire, explosion, personal injury, or death.
2. Component test—The furnace control allows all components, except gas valve, to be run for a short period of time.
This feature helps diagnose a system problem in case of a component failure. To initiate component test procedure, short (jumper) the TEST
1/4-in. quick connect terminal on control board (adjacent to diagnostic light) and the C terminal on thermostat connection block for
approximately 2 sec. (See Fig. 11.)
NOTE:
Component test feature will not operate if any thermostat signal is present at control center.
Component test sequence is as follows.
a. Momentarily jumper TEST and C terminals until LED goes off.
b. LED will display previous fault 4 times.
c. Inducer motor operates for 10 sec, then stops.
d. Hot surface ignitor is energized for 15 sec, then de-energized.
e. Blower motor operates on cooling speed for 10 sec, then stops.
f. Blower motor operates on heating speed for 10 sec, then stops.
3. To operate furnace, follow procedures on operating instruction label attached to furnace.
4. With furnace operating, set thermostat below room temperature and observe that furnace goes off. Set thermostat above room temperature
and observe that furnace restarts.
D.
Adjustments
1. Set gas input rate.
There are 2 methods of adjusting the gas input rate. The preferred method is by using Table 7 and following instructions in item a. The
second method is by clocking the gas meter and following instructions in item b.
The gas valve regulator has been nominally set at 3.5-in. wc for natural gas. When adjusting input rate, do not set manifold pressure above
3.8-in. wc or below 3.2-in. wc.
a. Check gas input rate using Table 7.
(1.) Obtain average yearly heat value for local gas supply.
(2.) Obtain average yearly specific gravity for local gas supply.
(3.) Verify furnace model. Table 7 can only be used for model GB3AAV Furnaces.
(4.) Check and verify orifice size in furnace. NEVER ASSUME THE ORIFICE SIZE. ALWAYS CHECK AND VERIFY.
CAUTION: DO NOT redrill burner orifices. Improper drilling (burrs, out-of-round holes, etc.) can cause excessive
burner noise and misdirection of burner flames. This can result in flame impingement of the burners and heat exchangers,
causing failure.
(5.) Find natural gas heat value and specific gravity in Table 7.
—15—
→