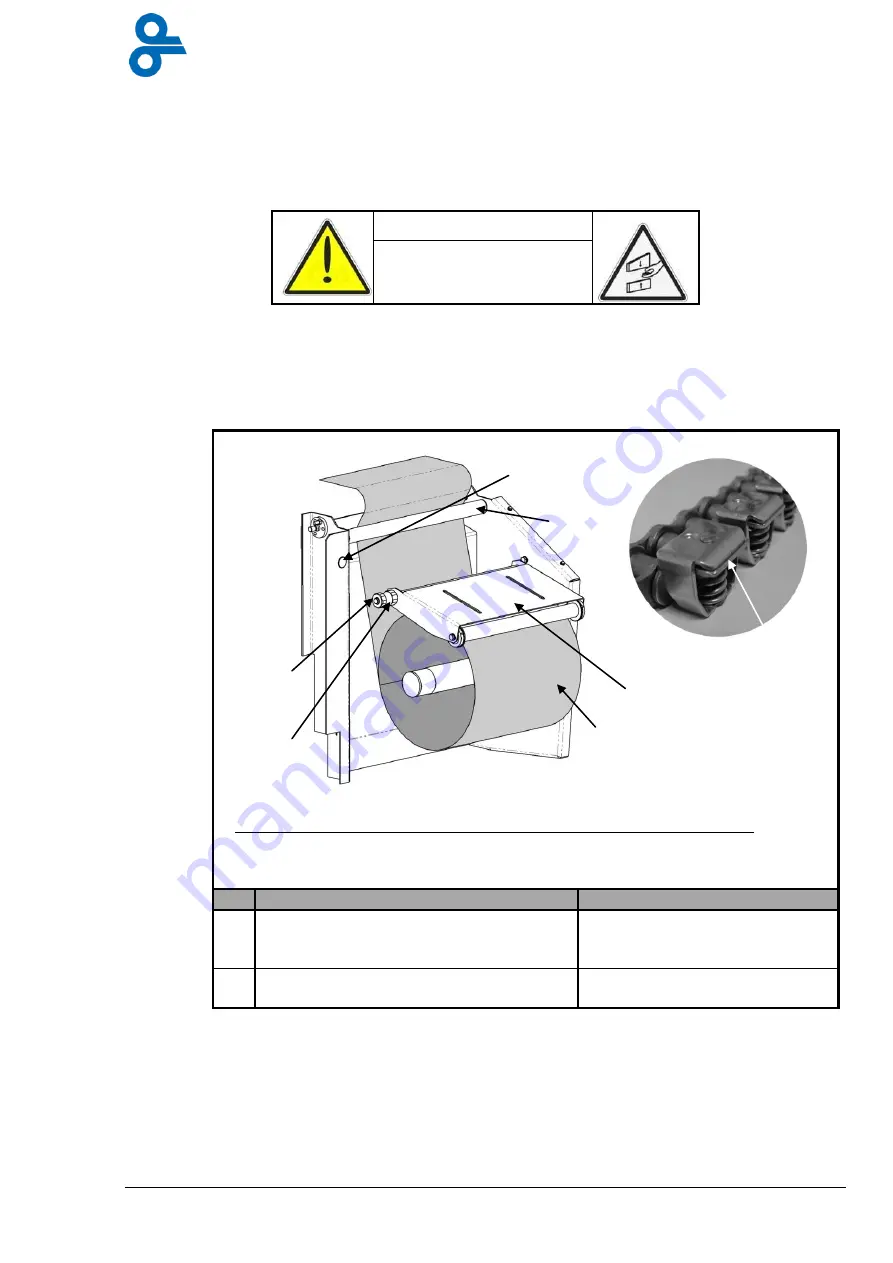
112
5.3
Fitting the rolls of film
The machine uses 2 rolls of film for packaging the products: a lower and an top film. First a
description is given of the step-by-step procedure for fitting the bottom film and then for fitting
the top film. During these procedures the cover plates must be fitted to the machine.
5.3.1 Bottom film
A step-by-step description of how to fit a new roll of bottom film is given in table 8. The main
switch must be turned on but no packaging process may be performed.
Table 8 Staged plan for fitting the bottom film
No. Action
Remark
1.
Makes sure you execute all steps
according to paragraph 5.2.3, put machine
in film infeed mode
Via the operator menu.
2.
Raise the film guide against the infeed
roller.
Make sure it does not fall back.
WARNING
At each stage take care not
to trap any body parts.
film chain
slow transport button
film guide
film roll
setting
button
lock nut
chain clips
in-feed
roller
Figure 5.5 Bottom film with film chain