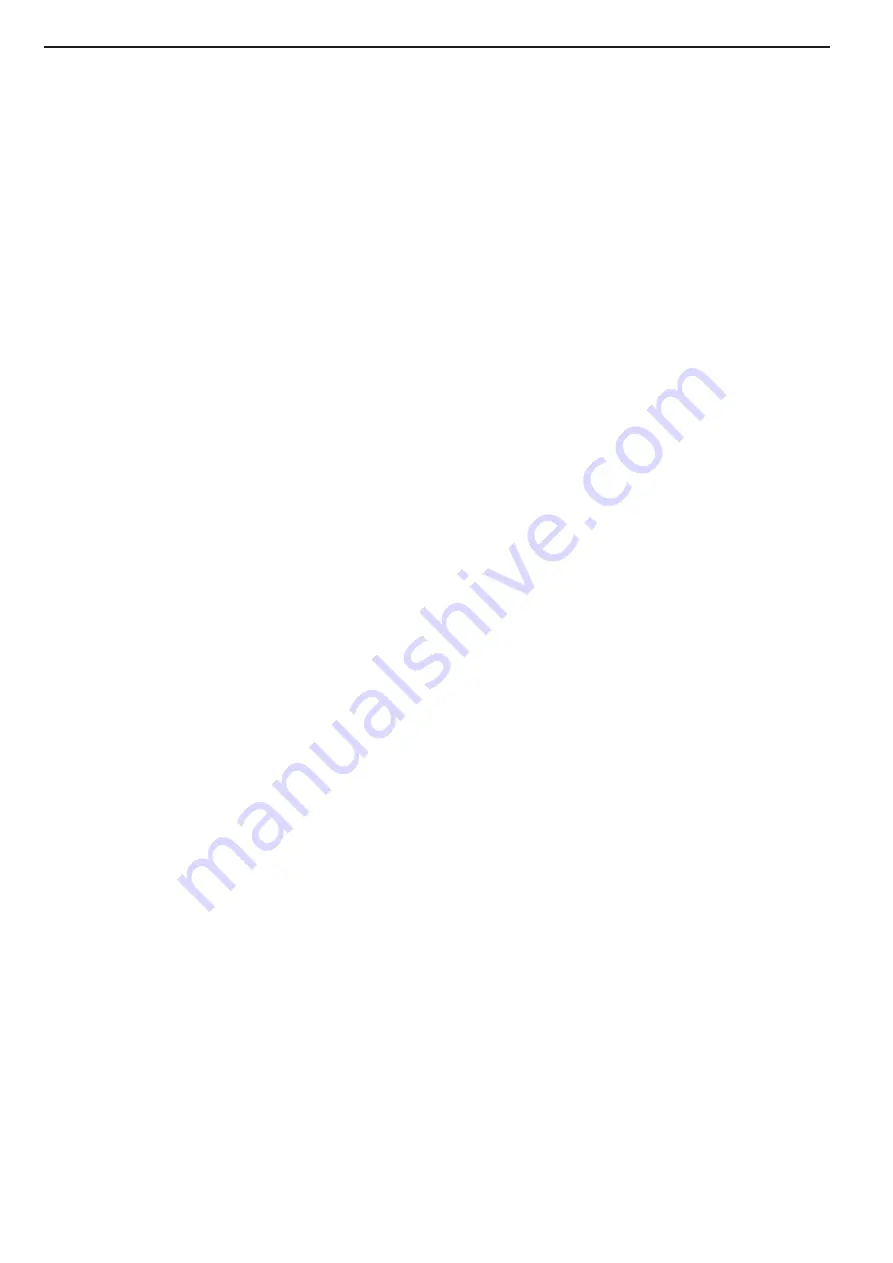
GBR
GBR
2.2. Electrical connection
Before connecting the machine to the power supply, check that the voltage spe-
cified on the rating plate complies with the mains voltage. The welder (5) is sup-
plied complete with its own connecting lead, so it also essential to check the
voltage on the rating plate for conformity with the mains.
2.3. Positioning the welder and facing cutter
The welding unit can be removed from every model in this series and used
as a hand-operated machine. In the case of the REMS SSM 160 R and
REMS SSM 160 K, it is installed the mounting (17) by the hand-grip (16),
while in the case of the REMS SSM 250 K and REMS SSM 315 RF, it is se-
cured with an additional plug.
Caution! When the appliance is hot, grasp it only by the hand-grip (16).
Never touch the heating element or metal components between the hand-
grip and heating element, otherwise a burn injury may result.
After the machine has been transported, the welder (5) must be centred.
For this purpose, release clamping lever (22) and pull back the retainer (17)
of the welder (5) on the sliding block (21) as far as it will go. Now re-tighten
the clamping lever (22).
Swivel out the welder (5) and facing cutter (6). Before moving the welder (5)
and facing cutter (6) sideways, slightly raise the handle (18) or (20), other-
wise the end-stop will apply a braking effect.
2.4. Electronic temperature control
According to DIN 15960 and DVS 2208, Part 1, the temperature of the heat-
ing element should be capable of being adjusted in fine stages. In order to
ensure that the heating element operates at the required constant tempe-
rature, these machines are equipped with a thermostat. DVS standard 2208,
Part 1 specifies a maximum differential of 3°C between the preset and ac-
tual temperatures. In practice, this degree of accuracy cannot be achieved
mechanically, but only by an electronic thermostat.
For this reason, therefore, welding machines operating at a fixed, preset tem-
perature or employing a mechanical thermostat may not be used for welding
operations as described in DVS 2207.
The temperature can be adjusted on all REMS welders. All models are sup-
plied with electronic thermostats. The butt welding unit is identified on the
welder rating plate by code letters, example of which is given below.
REMS SSG 180 EE: Adjustable temperature (E), electronic thermostat (E).
The preset temperature is adjusted to within ± 1°C, i.e. with a preset tem-
perature of 210°C (welding temperature for PE) the actual temperature will
fluctuate between 209°C and 211°C.
2.5. Preheating the butt welding unit
The welder connecting lead is plugged into the socket (23) at the rear of the
facing cutter housing. As soon as this lead is connected to the mains, the
machine is ready to operate and the heating element will begin to heat up.
The red power-on indicator lamp (24) and green temperature indicator lamp
(25) light up. The machine requires about 10 minutes to heat up. Once the
required preset temperature is reached, the built-in thermostat cuts out the
power supply to the heating element. The red indicator lamp continues to
glow. The green temperature indicator lamp of the electronic thermostat (EE)
will light up intermittently, indicating the repeated switching on and off of the
power supply. After a further 10 minutes waiting time (DVS 2207, Part 1),
welding operations can begin.
2.6. Selecting the correct welding temperature
The welder heating element is preadjusted to the average welding tempe-
rature for PE-HD pipes (210 °C). Depending on the pipe material and the
gauge of the pipe walls, it may be necessary to adjust this temperature. In
this case, observe the manufacturer’s information on the pipes or mouldings
without fail. Fig. 5 contains a graph showing the guideline temperatures for
heating elements according to the gauge of the pipe walls. In principle, the
higher temperature should be used for thinner walls and the lower tempera-
ture for thick walls, as far as possible (DVS 2207, Part 1). In addition, envi-
ronmental influences (summer/winter) may make it necessary to adjust the
temperature. For this reason, the temperature of the heating element should
be checked, e.g. with an electric surface thermometer. If necessary, the tem-
perature can be adjusted by turning the temperature adjusting screw (26).
In this case, it should be remembered that the heating element must not be
used until 10 minutes after the preset temperature has been reached.
3. Operation
3.1. Description of process
In the butt welding process, the contact faces of the two components are
matched to each other under pressure on each side of the heating element,
heated to welding temperature at reduced pressure, then joined under pres-
sure after the heating element has been withdrawn (Fig. 6).
3.2. Preparations of welding
If the machine is used in the open air, care must be taken to ensure that wel-
ding will not be adversely affected by unfavourable environmental conditions.
In bad weather or strong sunlight, the welding position should be covered,
if necessary with an awning. To prevent the uncontrolled cooling of the welding
position by draughts, the welded pipe ends should be enclosed. Out-of-round
pipe ends must be trued up before welding by e.g. carefully heating with a
warm air heater. Only pipes or pipes and mouldings of the same material
and wall thickness may be welded. Pipes should be cut off with a REMS
RAS pipe cutter (see 1.1).
3.3 Clamping the pipes
Pipe clamping inserts (27) corresponding to the pipe diameter should be in-
stalled in the clamps (19) in such a way that the cranked side of the inserts
faces the centre. The inserts are secured with hex screws (28) by means of
the wrench supplied. The two pipe support inserts (29) should be similarly
installed on the pipe supports (30) and secured with hex screws (28). The
pipes or pipe sections should be aligned in the clamping assembly before
being clamped. If necessary, long pipes should be supported with a REMS
Herkules (see 1.1). For short pipe sections, the pipe supports (30) should
be adjusted or turned through 180°. For this purpose, loosen clamping knob
(31) and reposition the pipe support or raise knob (32) and turn the pipe sup-
port about the axis of the clamping knob (31). The pipe ends should project
10-20 mm towards the centre beyond the clamping adapters or clamps to
permit planing.
Align the pipes or fittings in such a way that the faces are parallel to each
other, i.e. the pipe walls must be in alignment in the area of the joint. If
necessary, the clamps should be released and the pipes re-aligned and
turned (check for out-of-roundness). If adjustment proves unsuccessful after
several attempts, it will be necessary to readjust the clamping system. For
this purpose, the clamping screws (33) on both clamps should be released
and a pipe clamped in each of the two clamps. If the pipe is not resting in
the clamps and on the pipe supports, centre the clamps by tapping the sides.
With the pipe still clamped, retighten the clamping screws (33).
The clamps must enclose the pipe ends securely. If necessary, readjust the
clamping nut (34) under the clamping cam (35) until the clamping lever (36)
can only be closed with a certain amount of force.
3.4. Planing the pipe ends
Immediately before welding, the pipe ends must be planed flat. For this pur-
pose, the electric facing cutter (6) is swivelled into the working area and
switched on by means of the rocker switch in the handle (20). While the facing
cutter is running, the pipe ends must be slowly offered up to the planing discs
by means of the contact lever (7). Planing should be continued until an un-
broken swarf is formed on both sides. With the facing cutter still running, now
slowly ease off the contact lever (7) so that no swarf remains on the pipe
ends. After the facing cutter has been swivelled out, the planed pipe ends
should be brought together on a trial basis, so as to check that the faces are
parallel and that the pipes are not axially displaced. Under the application
of adapting pressure, the gap between the parallel faces must not exceed
the width specified in Fig. 7 or the displacement on the outside of the pipe
exceed 10% of the wall thickness. The planed faces must not be touched
again before welding takes place.
If a pipe or moulding on one side can no longer be planed or must not be
planed at all, whereas further planing is required on the other side, the stop
buffer on the underside of the planer housing should be swivelled out on the
side on which no further planing should take place.
3.5. Butt welding process
In the welding process, the joint faces are heated to welding temperature by
a heating element, then welded together under pressure after the heating
element has been withdrawn. Before each welding process, the temperature
of the heating element in the welding area should be checked. If necessary,
it must be adjusted as described in 2.6. Also before each welding process,
the heating element should be cleaned with non-adherent paper or a non-
fraying cloth and spirit or industrial alcohol. In particular, no remnant of plastic
must be left adhering to the coating on the heating element. Also in the clean-
ing process, care must be taken to ensure that the anti-adhesive coating of
the heating element is not damaged by tools.
The process stages are shown in Fig. 8.
3.5.1. Adapting
In the adapting process, the joint faces are pressed against the heating ele-
ment until a bulge forms around each circumference. During this process, a
matching-up pressure of e.g. 0.15 N/mm² should be applied for PE (DVS
2207, Part 1).
Depending on the diameter and wall thickness of the pipe, the requisite de-
gree of pressure must be calculated to ensure a pressure of 0.15 N/mm² at
the joint faces. Pressure F is calculated from the product of adapting pres-
sure p and pipe face area A (F=p·A), i.e. the greater the pipe face area, the
higher the pressure required. Thus, a pipe of e.g. 110 mm diameter and PN
3,2 (s=3.5 mm) gives a pipe face area of 1170 mm² and a requisite adap-
ting pressure of F=0.15 N/mm²·1170 mm²=175 N. A plate (37) is attached
to each machine containing a table indicating which pipes can be welded,
up to what pressure stage, and under how much pressure, with the machine
concerned. Figs. 9 to 13 show these tables for the REMS SSM models 160
R, 160 K, 250 K and 315 RF. The requisite amount of pressure should be
taken from the respective table and applied with the contact lever (7). When
the joint faces are pressed together by means of this lever, the applied pres-
sure can be seen by reference to the pointer (38).
Before welding takes place, a check must be made to ensure that the clamps
are holding the pipe sections sufficiently securely to enable them, as a mini-
mum, to absorb the necessary pressure. For this purpose, bring the pipe ends
together cold and apply at least the calculated pressure by means of the
contact lever (7) on a trial basis. If the clamps do not hold the pipe sections
securely, the clamping cams (35) must be readjusted (see 3.3.)
The adapting process is concluded when a bulge, which is at least as high
as the figure given in Fig. 14, column 2, has formed around the entire cir-
cumference of the pipe sections.
3.5.2. Heating
For the heating process, the pressure is reduced to almost zero. The heat-
ing period is given in Fig. 14, column 3. During the heating process, the heat
penetrates into the joint faces, raising them to the necessary welding tem-
perature.
3.5.3. Changeover
After heating, the joint faces shoud be withdrawn from the heating element,
which is then retracted without touching the heated faces. These are then
rapidly brought together until just before they touch. The time taken for this
process must not exceed the limit given in Fig. 14, column 4, otherwise the
joint faces will cool to an impermissible extent.