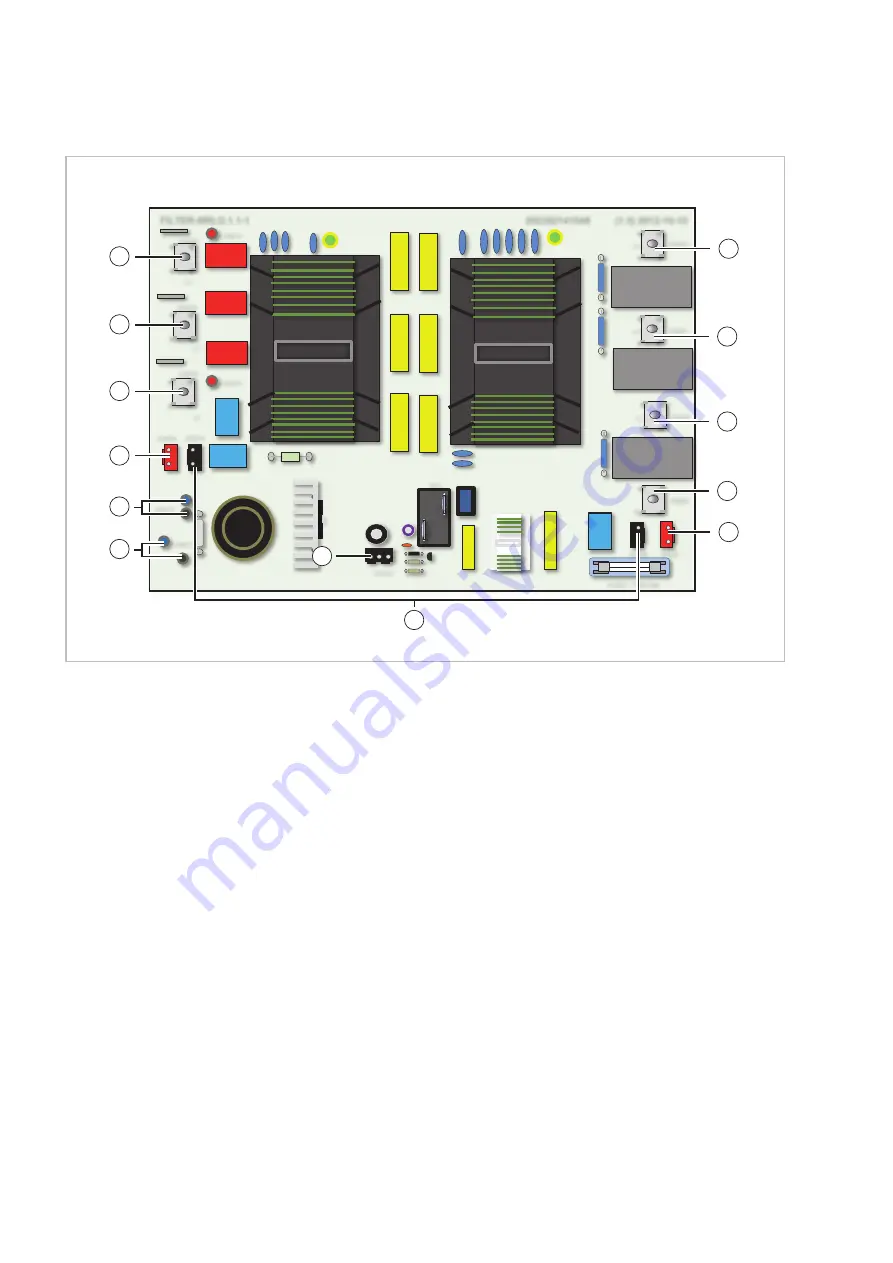
Electrical drawings MVV 2000 DC
L3
L2
L1
CN204
CN205
CN206
L1
CN200
CN201
CN202
L2
L3
CN203
N
FILTER-8R0.D.1.1-1
202302141048
(1.5) 2012-10-10
3
4
CN214
CN213
CN209 CN210
CN212
CN211
CN150
RY1
FUSE1 / T250V/8A
CN208
CN207
4
1
2
3
9
10
11
5
6
7
8
12
13
Fig. 36: Electrical drawings MVV 2000 DC power pcb
1:
Connection with the three-phase inverter
(contact: 1)
2:
Connection with the three-phase inverter
(contact: 2)
3:
Connection with the three-phase inverter
(contact: 3)
4:
Connection to the control board (contact: CN 41)
5:
Connection to the IPM board (contact: CN 2)
6:
Connection to the distribution board
(contact: CN 101)
7:
Connection to the control board
(contact: CN 150)
8:
Connected with each other
9:
Connection with the terminal block, power
supply (contact: L3)
10: Connection with the terminal block, power
supply (contact: L2)
11: Connection with the terminal block, power
supply (contact: L1)
12: Connection with the terminal block, power
supply (contact: N)
13: Connection to the control board
(contact: CN 250)
REMKO MVV...DC
40
Summary of Contents for MVV 1200 Dc
Page 67: ......