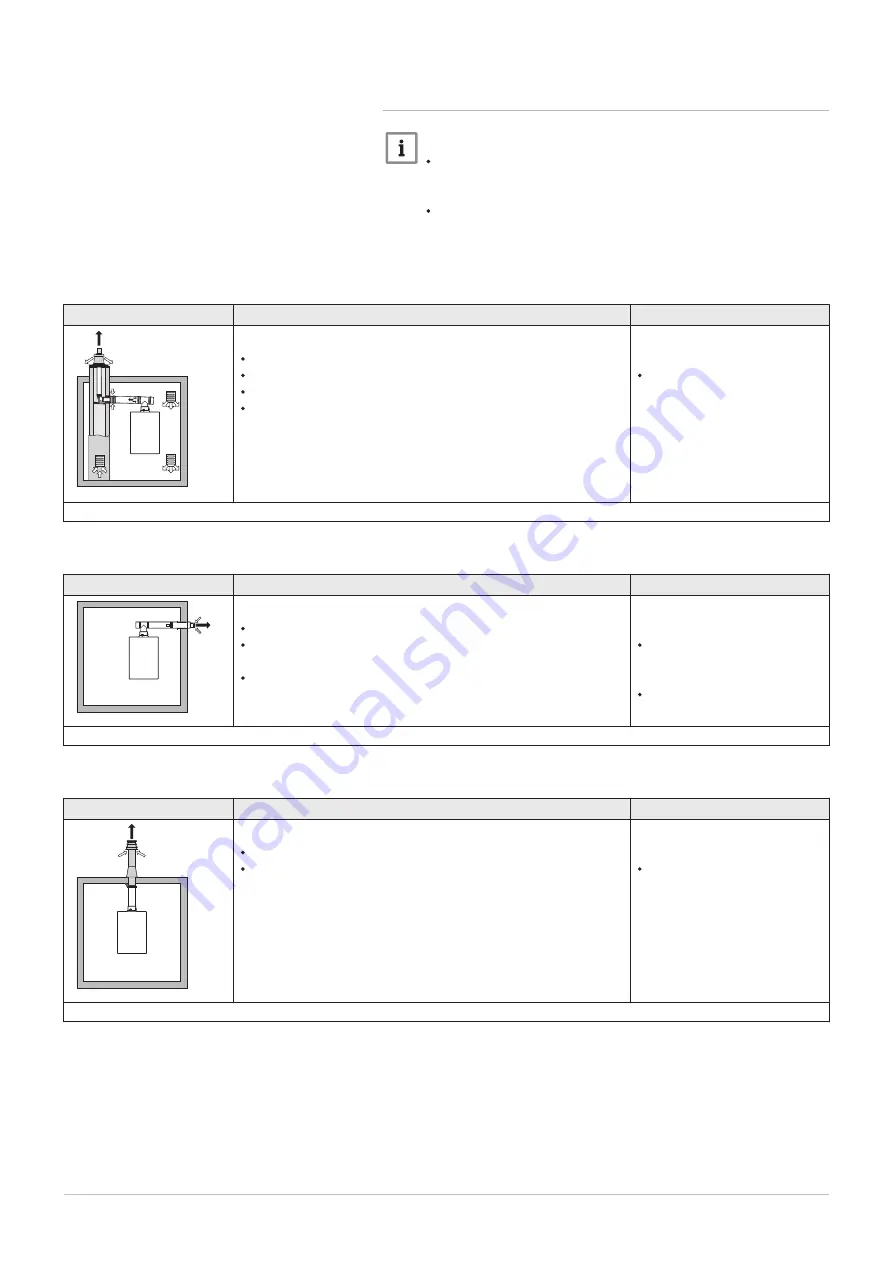
6.5.1
Classification
Important
The installer is responsible ensuring that the right type of flue
gas outlet system is used and that the diameter and length are
correct.
Always use connection materials, roof terminal and/or outside
wall terminal supplied by the same manufacturer. Consult the
manufacturer for compatibility details.
Tab.12 Type of flue gas connection: B
23P
Principle
Description
AD-3000924-01
Room-ventilated version
Without down-draught diverter.
Flue gas discharge via the roof.
Air from the installation area.
The IP rating of the boiler is lowered to IP20.
Connection material and roof
terminal:
Muelink & Grol
(1) The material must also satisfy the material property requirements from the relevant chapter.
Tab.13 Type of flue gas connection: C
13
Principle
Description
AD-3000926-01
Room-sealed version
Discharge in the outside wall.
Air supply opening is in the same pressure zone as the dis
charge (e.g. a combined outside wall terminal).
Parallel not permitted.
Outside wall terminal and con
nection material:
Remeha, combined with con
nection material from Muelink
& Grol
Muelink & Grol
(1) The material must also satisfy the material property requirements from the relevant chapter.
Tab.14 Type of flue gas connection: C
33
Principle
Description
AD-3000927-01
Room-sealed version
Flue gas discharge via the roof.
Air supply opening is in the same pressure zone as the dis
charge (e.g. a concentric roof terminal).
Roof terminal and connection
material
Muelink & Grol
(1) The material must also satisfy the material property requirements from the relevant chapter.
6 Installation
7625116 - v.06 - 17102018
29