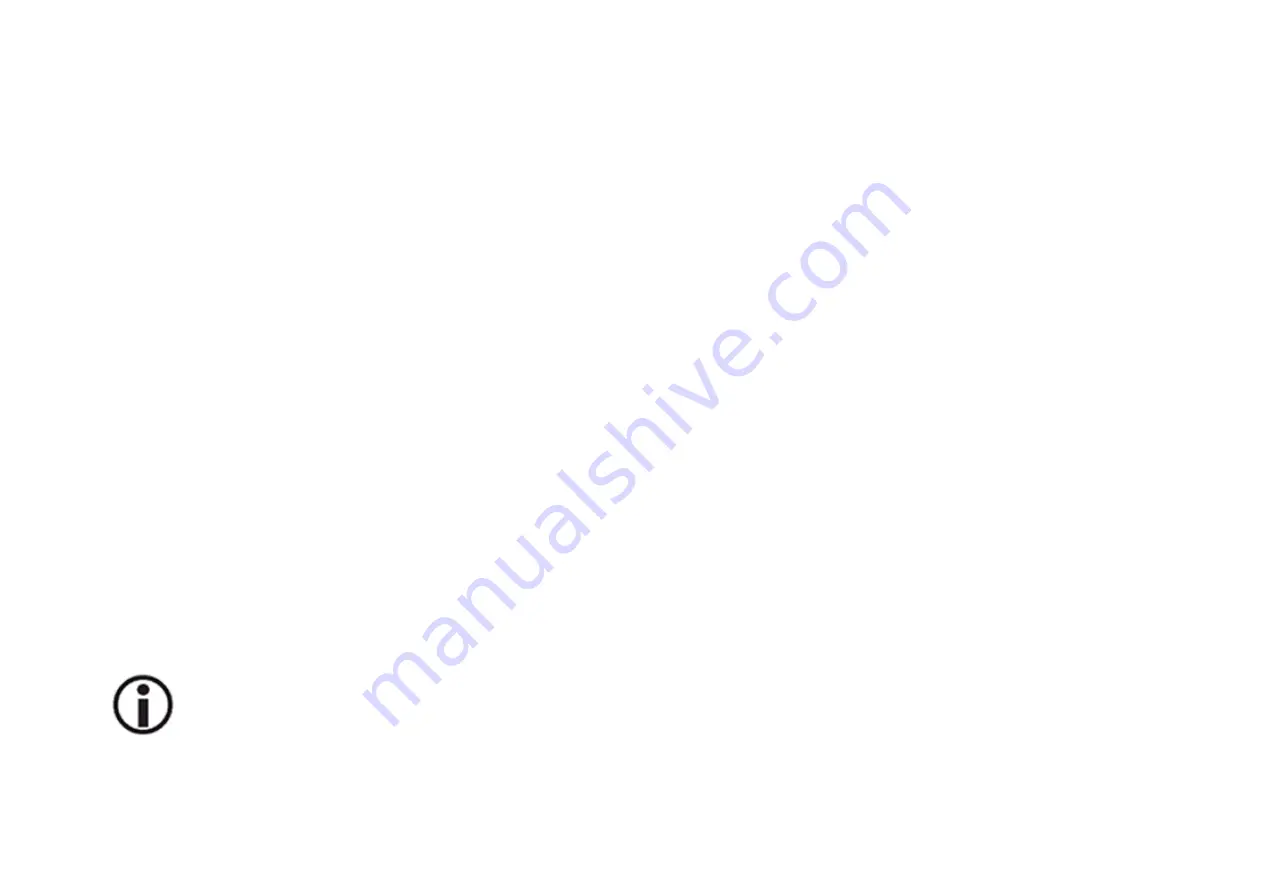
Our products are manufactured in compliance with the requirements of the various applicable European Directives.
This appliance complies with the requirements of the CE marking directive.
In the interest of UK customers, we are continuously endeavouring to make improvements in product quality. All the specifications stated in this
document are therefore subject to change without notice.
Our liability as the manufacturer may not be invoked in the following cases:
#
Failure to abide by the instructions on using the appliance.
#
Faulty or insufficient maintenance of the appliance.
#
Failure to abide by the instructions on installing the product.
Installer's liability
The installer is responsible for the installation and the commissioning of the appliance. The installer must respect the following instructions:
#
Read and follow the instructions given in the manuals provided with the appliance.
#
Carry out installation in compliance with the prevailing legislation and standards.
#
Perform the initial start up and carry out any checks necessary.
#
Complete the commissioning checklist.
#
Explain the installation to the user.
#
If maintenance is necessary, warn the user of the obligation to check the appliance and maintain it in good working order.
#
Give all the instruction manuals to the user.
Users liability
To guarantee optimum operation of the appliance, the user must respect the following instructions:
#
Read and follow the instructions given in the manuals provided with the appliance.
#
Call on qualified professionals to carry out installation and initial start up.
#
Get your fitter to explain your installation to you.
#
Have your required checks and services done.
#
Keep the instruction manuals in good condition and close to the appliance.
This appliance can be used by children aged from 8 years and above and persons with reduced physical sensory or mental capabilities or lack of experience
and knowledge if they have been given supervision or instruction concerning use of the appliance in a safe way and understand the hazards involved.
Children shall not play with the appliance.
Cleaning and user maintenance shall not be made by children without supervision.
Children must be supervised to ensure they do not play with the appliance.
Summary of Contents for 1000 Indirect
Page 2: ......
Page 11: ......
Page 13: ...Figure 3 Indirect wiring diagram 1 Thermostat Option 2...
Page 15: ...Figure 4 Single phase wiring schematic...
Page 18: ...2 port zone valve...
Page 19: ......
Page 24: ......
Page 31: ......
Page 35: ...Figure 12 Auxiliary controls...
Page 36: ...Figure 13 Indirect controls page 18 8 Operation 8 1 General...
Page 45: ...3 7 8 Part No See table Part No 95 605 176 9 12 13 Part No See table Part No 95 605 182...
Page 46: ...14 15 Part No 95 607 367 Part No 95 607 425 16 18 19 21 Part No See table Part No See table...
Page 51: ...page 27 page 28 page 29 MAINS PRESSURE HOT WATER STORAGE SYSTEM COMMISSIONING CHECKLIST...
Page 52: ......
Page 54: ......