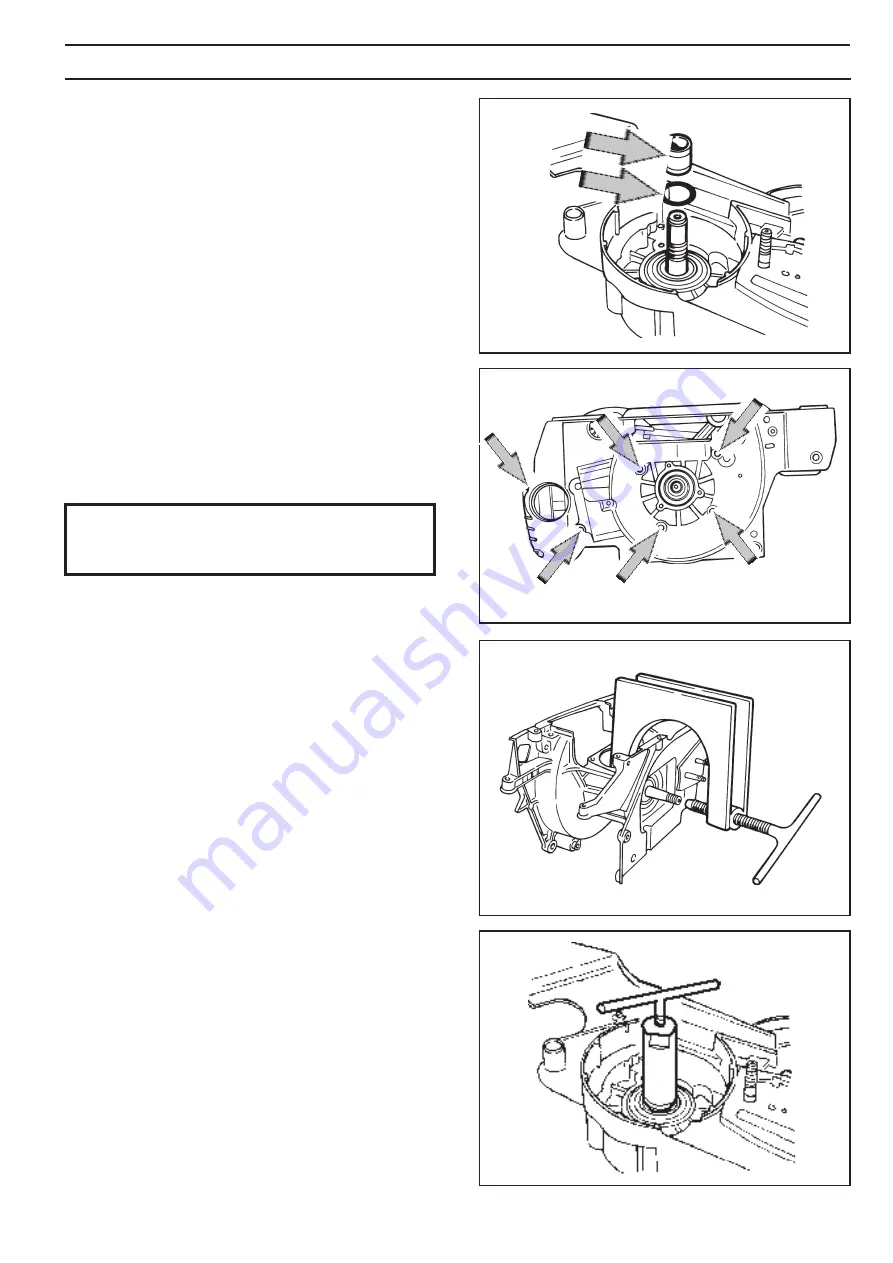
CRANKCASE AND CRANKSHAFT
English – 43
Fig. 1
Fig. 2
Fig. 3
Fig. 4
1. Before the crankcase can be split, the following
components must be removed:
A.
Chain and guide bar.
B.
Recoil starter.
C.
Electrical system.
D.
Centrifugal clutch.
E.
Lubrication system.
F.
Carburettor.
G.
Silencer.
H.
Piston and cylinder.
I.
Tank unit.
This section deals with the following:
•
Crankcase and crankshaft (describes how the whole
assembly is dismantled and reassembled)
•
Seals (describes only replacement of seals)
•
Guide bar bolts (describes only replacement of the
guide bar bolts)
2. Remove the carburettor space bottom plate by
taking out the four bolts.
3. Remove the washer and spacer on the clutch side.
See
fi g. 1.
4. Remove the six bolts on the fl ywheel side. See fi g. 2.
5. Fit tool 502 51 61-01 as shown in fi g. 3 and remove
the clutch side crankcase half.
6. Remove the flywheel side crankcase half in the
same way as for point 5 above.
7. If required remove the seals. Use tools 502 50 55-
01 and 504 91 40-01. See fi g. 4.
8. If required, remove the crankshaft bearings from the
crankcase. Proceed as follows:
Crankcase and crankshaft
Dismantling
NOTE!
Ensure that no dirt or foreign particles enter
the bearings.