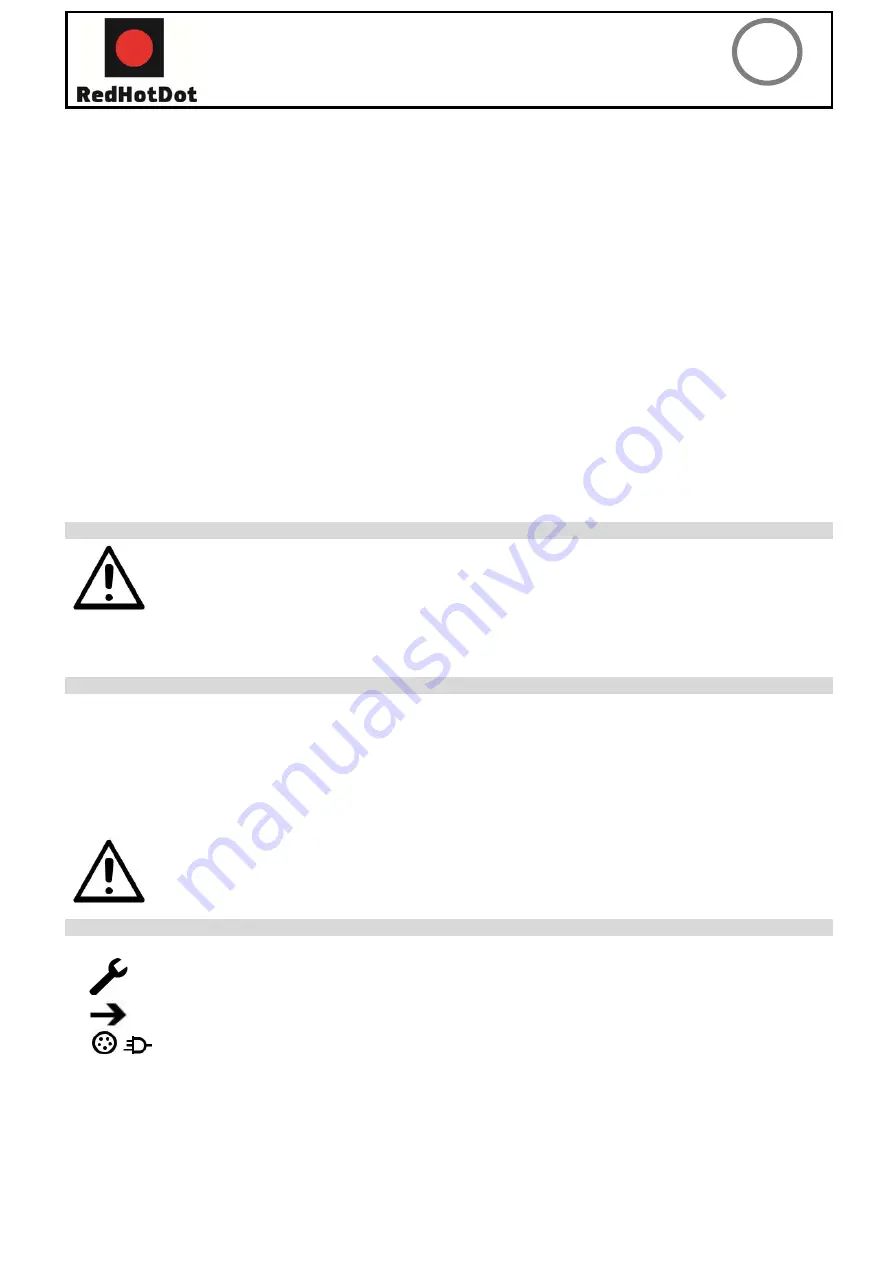
MMAX9
8
EN
filtering of the power suplly network. Consideration should be given to shielding the power supply cable in a metal conduit. It
is necessary to ensure the shielding’s electrical continuity along the cable’s entire length. The shielding should be connected to
the welding current’s source to ensure good electrical contact between the conduct and the casing of the welding current
source.
B. Maintenance of the arc welding equipment
: The arc welding machine should be be submitted to a routine maintenance
check according to the manufacturer’s recommendations. All accesses, service doors and covers should be closed and properly
locked when the arc welding equipment is on. The arc welding equipment must not be modified in any way, except for the
changes and settings outlined in the manufacturer’s instructions. The spark gap of the arc start and arc stabilization devices
must be adjusted and maintained according to the manufacturer’s recommendations.
C. Welding cables
: Cables must be as short as possible, close to each other and close to the ground, if not on the ground.
D. Electrical bonding
: consideration shoud be given to bonding all metal objects in the surrounding area. However, metal
objects connected to the workpiece increase the riskof electric shock if the operator touches both these metal elements and the
electrode. It is necessary to insulate the operator from such metal objects.
E. Earthing of the welded part
: When the part is not earthed - due to electrical safety reasons or because of its size and its
location (which is the case with ship hulls or metallic building structures), the earthing of the part can, in some cases but not
systematically, reduce emissions It is preferable to avoid the earthing of parts that could increase the risk of injury to the users
or damage other electrical equipment. If necessary, it is appropriate that the earthing of the part is done directly, but in some
countries that do not allow such a direct connection, it is appropriate that the connection is made with a capacitor selected
according to national regulations.
F. Protection and plating
: The selective protection and plating of other cables and devices in the area can reduce perturbation
issues. The protection of the entire welding area can be considered for specific situations.
TRANSPORT AND TRANSIT OF THE WELDING MACHINE
The machine is fitted with handle(s) to facilitate transportation. Be careful not to underestimate the machine’s
weight. The handle(s) cannot be used for slinging.
Do not use the cables or torch to move the machine. The welding equipment must be moved in an upright
position.
Do not place/carry the unit over people or objects.
Never lift the machine while there is a gas cylinder on the support shelf. A clear path is available when moving the tem.
EQUIPMENT INSTALLATION
• Put the machine on the floor (maximum incline of 10°.)
• Ensure the work area has sufficient ventillation for welding, and that there is easy access to the control panel.
• The machine must not be used in an area with conductive metal dusts.
• The machine must be placed in a sheltered area away from rain or direct sunlight.
• The machine protection level is IP21, which means:
- Protection against acess to dangerous parts from solid bodies of a
≥
12.5mm diameter and,
- Protection against vertically falling drops.
The manufacturer does not incur any responsability regarding damages to both objects and persons that result
from an incorrect and/or dangerous use of the machine.
MAINTENANCE / RECOMMENDATIONS
• Maintenance should only be carried out by a qualified person. Annual maintenance is recommended.
• Ensure the machine is unplugged from the mains, and wait for two minutes before carrying out main-tenance
work. DANGER High Voltage and Currents inside the machine.
• Remove the casing 2 or 3 times a year to remove any excess dust. Take this opportunity to have the
electrical connections checked by a qualified person, with an insulated tool.
• Regularly check the condition of the power supply cable. If the power cable is damaged, it must be replaced
by the manufacturer, its after sales service or an equally qualified person.
• Ensure the ventilation holes of the device are not blocked to allow adequate air circulation.
• Do not use this equipment to thaw pipes, to charge batteries, or to start any engine.
Summary of Contents for MMAX9
Page 1: ...WELDING MACHINE MMAX9 1 EN INSTRUCTION MANUAL 5 DE BEDIENUNGSANLEITUNG 12 RU 22...
Page 22: ...MMAX9 22 RU 10 40 C 14 104 F 20 55 C 4 131 F 50 40 C 104 F 90 20 C 68 F 2000 6500 10...
Page 23: ...MMAX9 23 RU 11 2 A...
Page 24: ...MMAX9 24 RU CEI 61000 3 12 EMF EMF C A B C D E F G H c 10 CISPR 11 2009...
Page 25: ...MMAX9 25 RU B C D E F 10 IP21 12 5...
Page 26: ...MMAX9 26 RU MMAX9 MMA DC MMA Tig 100 240 16A CEE7 7 230 50 60 I1eff MMAX9 265 400 50 60...
Page 28: ...MMAX9 28 RU 5 1 10 1 4 5 0 5 5 10 130 1 6 9 8 6 7 4 8 130 200 2 4 11 7 8 L 2 5 x d d L...
Page 29: ...MMAX9 29 RU 2 6 6 MMA TIG 100 240 AC TIG...
Page 32: ...MMAX9 32 12 5...