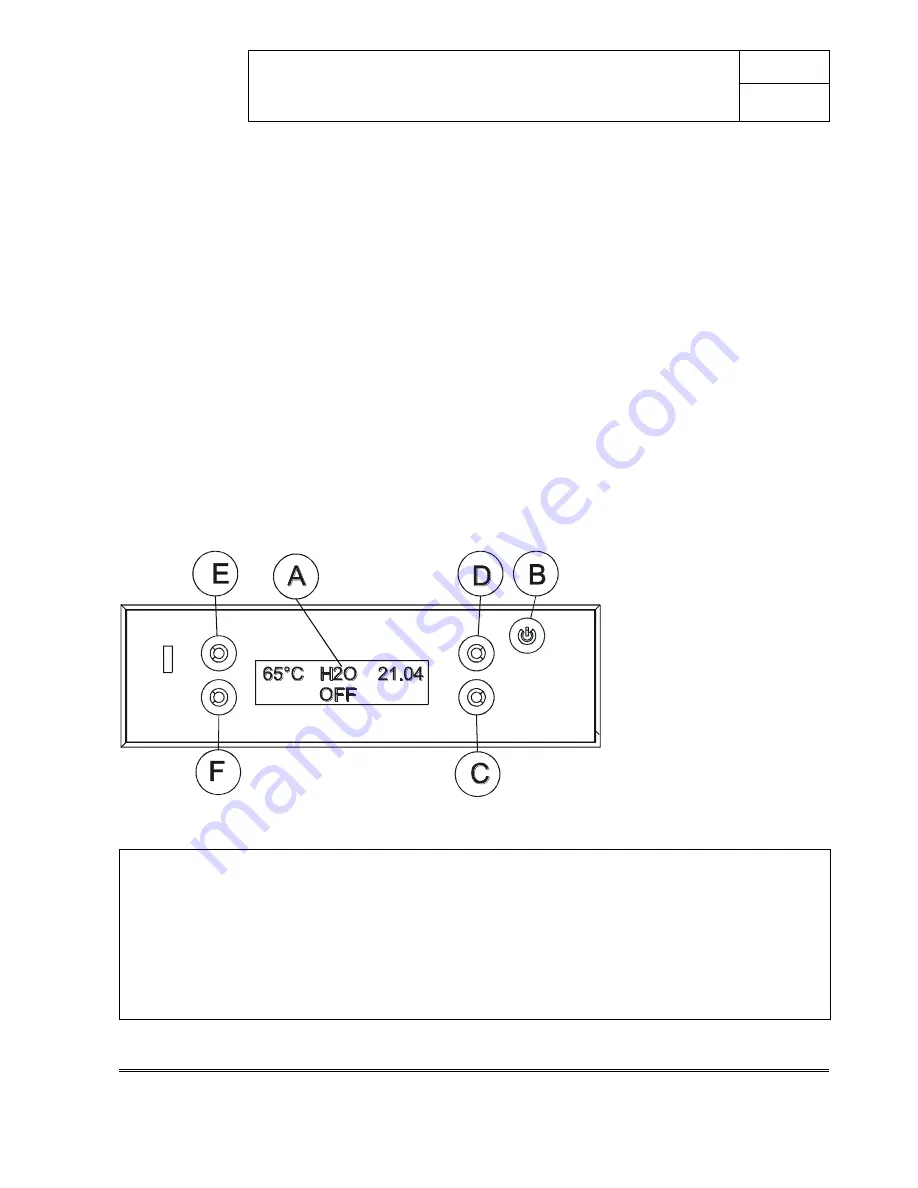
red
PRACTIKA 28-33
USE AND INSTALLATION MANUAL
Chapter 8
page 44
Control panel display
Technical dept. - All rights reserved - Reproduction prohibited
8. CONTROL PANEL DISPLAY
8.1.
Control panel logic
Below is some useful information to understand the logic for browsing and using the control panel.
The brightness of the control panel is turned off after approximately 30” if the keyboard is left
unused. To turn the backlighting back on, simply press any of the panel buttons.
The first screenshot displays the boiler operating status (ON, OFF, START-UP, SHUTDOWN...). It
also shows the current time and the temperature of the water measured in the boiler.
If you press any of the 4 keys surrounding the display (C D E F), you will enter the boiler operation
set-up screenshot (maximum flame level, boiler set temperature). In this menu, the 4 keys
surrounding the display assume "dedicated" functions, i.e. they are directly referred to the
corresponding wording shown in the four corners of the display (e.g. the top right wording refers to
key D).
When a setting is being modified at any menu level but it is not confirmed by pressing “OK”, if the
keyboard is left unused for a few
seconds, the initial screenshot will automatically be displayed and
none of the changes will be saved.
If the ON/OFF key (B) is pressed at any menu level, the display automatically returns to the initial
screenshot (boiler operating status) without saving any changes which have not been confirmed by
pressing “OK”.
KEY
A.
Display; shows a series of information about the boiler, in addition to the ID code for possible operating
faults.
B.
Start-up and shutdown key (ON/OFF) or ESC (to quit the menu).
C.
Select/modify key (from the subsequent screenshot)
D.
Select/modify key (from the subsequent screenshot)
E.
Select/modify key (from the subsequent screenshot)
F.
Select/modify key (from the subsequent screenshot)
N.B. the language can be set on the control panel.