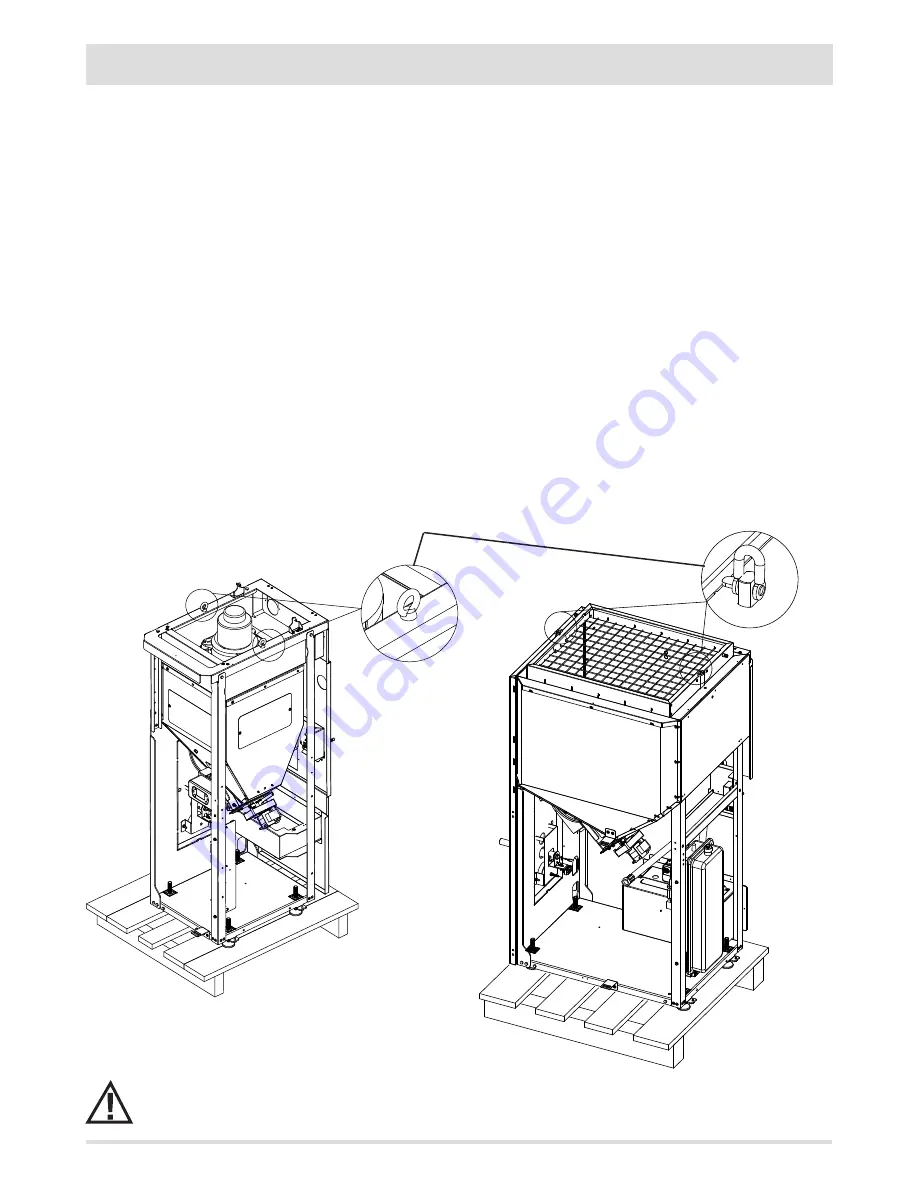
49
49
7 - INSTALLATION AND ASSEMBLY OF TANK
Technical Dept. - All rights reserved - Reproduction is prohibited
Instructions on how to install the structure of the tank:
a. Positioning on the ground (lifting or slide).
b. Put the tank in the room where it is to be installed (but NOT in its definitive position).
c. assembly of left side of the tank
d. Hydraulic connection of the tank to the boiler
e. mechanical connection between tank and boiler
f. insertion of spark plug
g. electrical and hydraulic connection of the control panel to the tank
h. electrical connection between tank and boiler
i. hydraulic connection between tank and water mains (supply-return-sanitary-filling)
l. hydraulic feed of boiler and check for leaks
k. assembly of aesthetics unit of boiler
m. assembly of trolley drawer, if easyclean kit is present
n. assembly of aesthetic unit of tank
o. hydraulic connection between the tank and water mains
a) Positioning on the ground (lifting or slide).
Open the package and remove the two front and back brackets, removing the two screws between each bracket and the tank and the two
screws that fasten the bracket to the pallet. After unpacking the structure it is possible to move the tank in two ways:
1) by means of the two lifting points on the tank.
ATTENTION! Do not use a single lifting point: use both at the same time.
WEIGHT 150 KG
Summary of Contents for LOGIKA 25
Page 79: ......