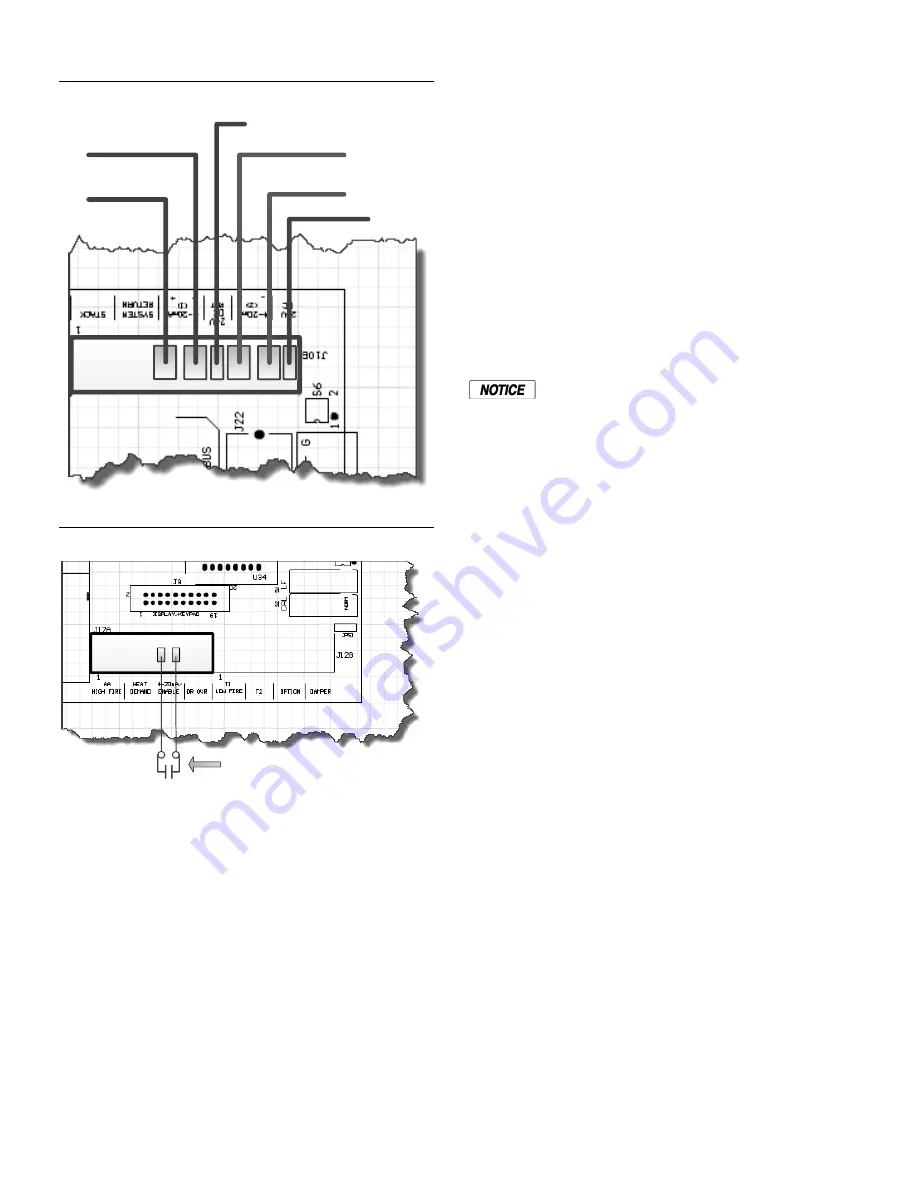
OPTIONAL FEATURES
HeatNet Control V3
Page 56
Figure 43
Example: 4
–20 mA connections
Channel 1:
4-20mA/0-10VDC
(+)
(-)
Channel 2:
4-20mA/0-10VDC
(+)
(-)
24 VDC Return
24 VDC
Figure 44
4
–20 mA enable connection
Closing this contact enables
the 4-20mA/0-10VDC input
The 4-20 mA input uses a 250 ohm sense resistor to convert
the current to a voltage from 1 to 5 volts DC for the control
to use. For this reason, a 1-5 VDC control voltage may also
be used across the 4-20mA +/- input, but it still needs to
supply the necessary current, i.e. 20mA. This resistor is
located on the bottom side of the control board. When a 4.02
mA signal is sensed, the boiler will initiate a start sequence
and fire the boiler at its minimum setting if the REMOTE
ENABLE input is closed. This is typically 25% of the boilers
output (4:1 turndown).
If the dip switch S6 is set to the 0-10 position (UP) See:
Figure 49
, the 4-20mA input will accept a 0-10 VDC signal.
The channel will also need to be setup in the menu:
ADVANCED SETUP: 4-20mA INPUT: CHANNEL
MODE
. The operating range will be from 2-10 VDC or
twice what was previously stated for the 1-5 VDC
functionality.
To convert a 0-10VDC signal to mA, divide
by 2510 (ohms).
NOTE: Due to the inability of control voltage methods (1-5,
2-10 VDC) to reject noise and compensate for line loss, the
use of the 4-20mA control current is recommended. The
control voltage methods may be less expensive, but are the
least stable. If using a 0-10VDC control signal, a source
current of a minimum 5mA is required.
If using a remote panel with a relay and a 4-20 mA
transmitter for operation, connect the 4-20mA transmitter
output from the remote panel to the Member boilers using the
floating 250 ohm method (type 4). The relay contacts on the
remote panel will then be connected to the associated 4-
20mA REMOTE ENABLE inputs on the associated boiler(s).
The minimum setting of the boiler is calibrated
so that the minimum PWM signal to control
the Blower motor is 20%. The VFD to blower
motor operates with a control signal from 20%
- 80% Pulse Width Modulation. This PWM
signal to the VFD can be measured using a
multimeter. It is a 0–10volt square wave signal
at 110 Hertz. A 20% modulation signal will
read 2.0 VDC, and an 80% modulation signal
will read 8.0 VDC on an RMS multimeter. See
Figure 59, page 75
For direct fire applications, the 0-10 volt
control signal is proportional to the output.
Such that: 1 volt will track linearly by 10%.
So, 1v=10%, 2v=20%, 3v=30%,
4v=40%... The control signal will still be
limited by the turndown and the 4-20mA
INPUT menu.
Setpoint Control
functionality can be implemented remotely
using the 4-20mA input. This function translates a 4 to 20mA
control signal to a setpoint mapped from 50F to 220F. The
feature is enabled in the SETPOINTS menu as:
SETUP:
SETPOINTS
:
SETPT SOURCE 4-20mA
.
ADVANCED SETUP: 4-20mA INPUT: CHANNEL
MODE
. Also, when selecting; SETUP: SETPOINTS:
SETPT SOURCE and selecting 4-20mA, the 4-20mA INPUT
menu will be automatically entered.
You may now select the current at which the boiler will start.
It is adjustable from 3.7mA to 5mA. Hysteresis of .1mA is
always in effect. So, if the starting mA = 4.10mA the boiler
will start when the control current applied achieves this value
of 4.10mA. The boiler must drop .1mA below this to turn
OFF, in this example 4.00mA. This hysteresis value is not
adjustable.
When using the 4-20mA setpoint control, a band may now be
set at which the 4-20mA signal will operate over. The lower
Summary of Contents for FUTERA XLF Series
Page 27: ...CONTROL METHODS HeatNet Control V3 Page 27 Figure 25 Base loading relay...
Page 67: ...WIRING CONNECTIONS HeatNet Control V3 Page 67 Figure 49 Jumper Dip Switch Locations...
Page 73: ...WIRING CONNECTIONS HeatNet Control V3 Page 73 Figure 57 Temperature sensors...