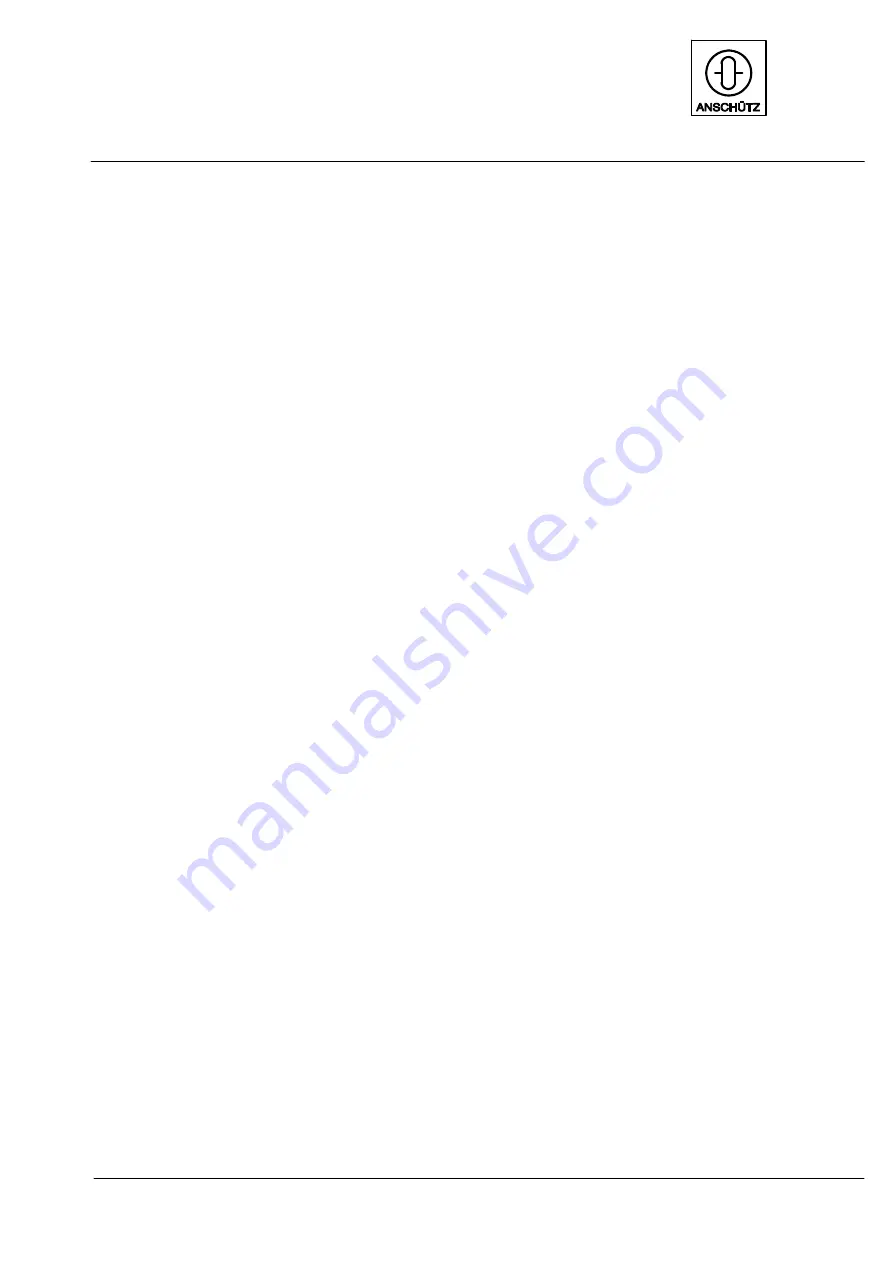
PILOTSTAR D
Autopilot
XIII
Edition: March 13, 2009
3060.DOC012
T
TRIM YAW
-- 2nd parameter for yawing (TRIM MODE)
TRIM RUD
-- 2nd parameter for rudder (TRIM MODE)
TRIM CNT
-- 2nd parameter for counter rudder (TRIM MODE)
TRACK LIM
-- track limit
W
WP
-- waypoint
WOP--circle
-- wheel over point circle
X
XTE TRIM
-- Cross Track Error Trim
Summary of Contents for Pilotstar D
Page 8: ...HSC P i l o t s t a r D VI 3060 DOC012 Edition March 13 2009 Intentionally left blank...
Page 42: ...PILOTSTAR D 1 26 Edition March 13 2009 3060 DOC012 Intentionally left blank...
Page 92: ...PILOTSTAR D 2 50 Edition March 13 2009 3060 DOC012 Intentionally left blank...
Page 144: ...PILOTSTAR D 4 40 3060 DOC012 Edition March 13 2009 Intentionally left blank...
Page 146: ...PILOTSTAR D Edition March 13 2009 3060 DOC012 Annex Content Intentionally left blank...
Page 151: ......
Page 152: ......
Page 153: ......
Page 154: ......
Page 155: ......
Page 156: ......
Page 157: ......
Page 158: ......
Page 159: ......
Page 160: ......
Page 161: ......
Page 162: ......
Page 163: ......
Page 164: ......