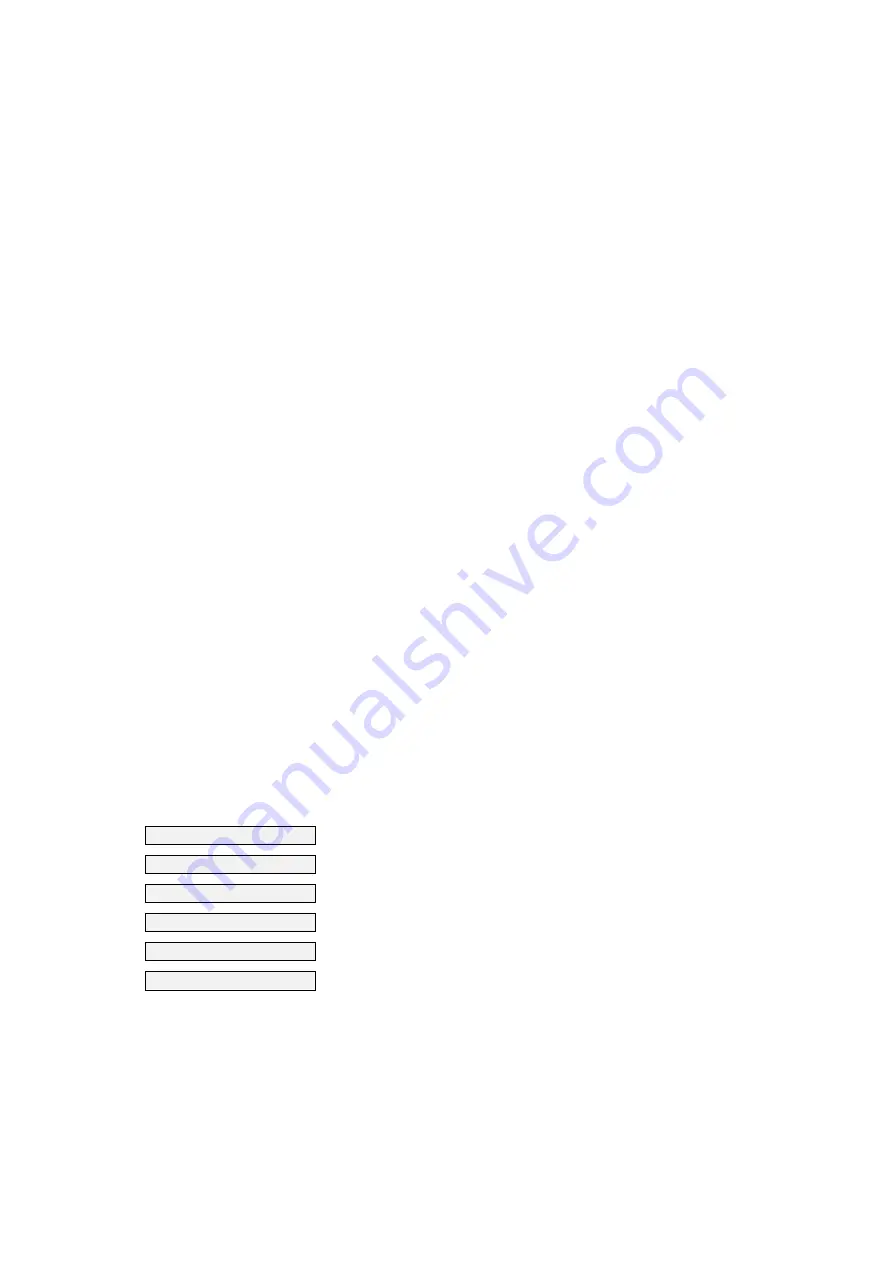
90
Adjusting ADJUST Menu Parameters
ADJUST menu parameters can only be adjusted/changed when VERSA control board DIP switch 1 is
set to ON (up). If DIP switch 1 is set to OFF (down), ADJUST menu parameters can be viewed but
cannot be adjusted/changed. DIP switch 1 OFF is the default setting.
1.
Turn heater OFF and isolate power supply to heater by switching off electrical isolator
located adjacent to heater.
2.
Remove front upper panel then remove six hex head screws retaining touchscreen surround panel
and remove panel.
3.
Switch VERSA DIP switch 1 to the ON (up) position.
4.
Restore power supply and turn heater ON.
5.
Reboot touchscreen
TOOLS > Screen Reboot > Screen Reboot
.
6.
Tap the
MENU
button to enter the home screen.
7.
Tap the
ADJUST
button to enter the adjust menu.
8.
Tap the relevant
Settings
button to enter its settings screen.
9.
If the selected settings button has a secondary menu, tap the relevant button to enter the
secondary settings screen. Skip this step if a secondary menu is not present.
10. Tap the parameters up
▲ or down ▼ buttons (or ON/OFF button or selection button) to adjust the
parameter. The value will change and the green bar above or beside the value will change to red
(if green bar is present
– not all parameters have green bar).
11. Tap the parameters
SET
button. The red bar above or beside the value will change to green and
the new value is accepted. Skip this step if a SET button is not present.
12. Perform steps 10 and 11 for all parameters in the currently entered settings screen.
13. Perform steps 6 ~ 12 for each settings screen until all parameters have been set.
14.
Turn heater OFF and isolate power supply to heater by switching off electrical isolator
located adjacent to heater.
15. Switch VERSA DIP switch 1 to the OFF (down) position.
16. Reassemble in reverse order of steps 2 ~ 1.
17. Reboot touchscreen
TOOLS > Screen Reboot > Screen Reboot
.
18. Validate correct operation.
Operation Settings
Used to adjust operating parameters (H models only)
System Settings
Used to adjust system parameters (all models)
MIX Settings
Not used (screen not available)
Indirect Settings
Only for H models with indirect DHW
(1)
Outdoor Settings
Only for H Models using optional outdoor air compensation
(2)
Modbus Settings
Used for configuring optional EMS/BMS (all models)