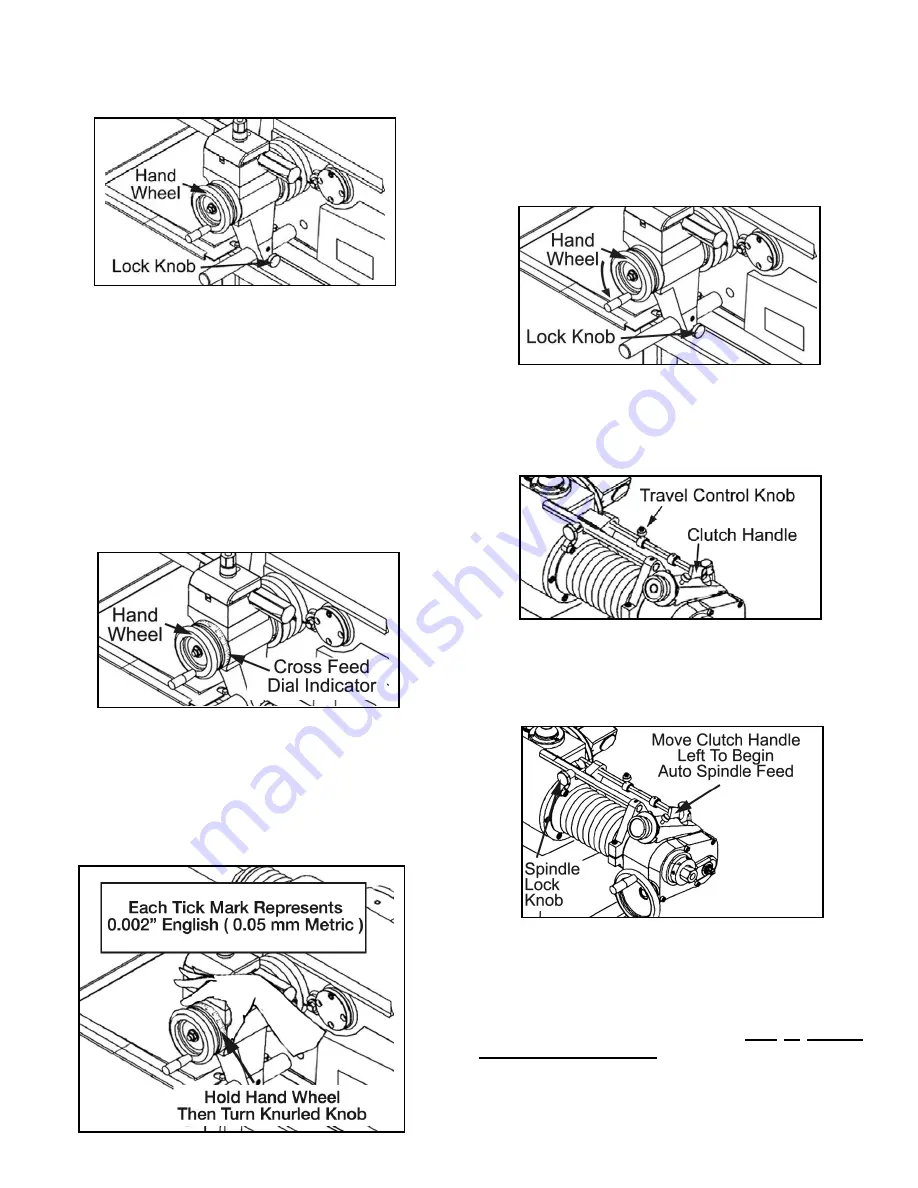
IMPORTANT NOTE
If the hand wheel does not turn freely, check to make
sure the cross feed lock knob is loosened.
13. Examine the scratch cut making sure it is uniform
around the entire circumference of the drum. If the scratch
cut appears to be deeper on one side of the drum and not
a uniform depth, then turn the power off, remove the drum
from the arbor, check the mounting adapters and arbor for
nicks, burrs, or chips, then remount the drum, and repeat
steps 4 - 13 until a uniform scratch cut is achieved.
14. Holding the cross feed hand wheel firmly in position with
your left hand, carefully rotate the cross feed dial indicator
(the outer, knurled knob) with your right hand until ZERO is
positioned at top dead center and lined up with the tick mark.
This will give you an initial zero-set starting point.
15. Turn the spindle feed hand wheel clockwise until the
boring bar reaches the innermost part of the drum. Be
careful not to crash the boring bar and cutting tip on the
inside wall of the drum or damage to tooling may result.
16. There are 100 graduations on the dial indicator. Each
tick mark represents 0.002” ( 0.05 mm metric ).
GUIDELINES TO DETERMINE THE DEPTH-OF-CUT
• Rough cuts should be no deeper than 0.020”.
• Finish cuts should be no shallower than 0.004” deep.
17. With the lathe running, turn the cross feed hand wheel
dial counterclockwise to the depth desired and then lock
the cross feed by tightening the lock knob.
18. Set the automatic feed shut-off by sliding the travel control
lock knob on the limit rod to a point that approximately equals
the depth of the drum and tighten the knob in place. The limit
rod will then automatically disengage the clutch handle and
stop the spindle feed when it reaches this point.
19. Double check to make sure the spindle lock knob is
loosened then engage the spindle feed clutch handle (move
to the left) to begin auto-feed drum resurfacing. To make sure
the clutch gear is fully engaged, hold the clutch handle to the
left until the spindle feed handwheel starts turning.
By engaging the spindle feed clutch handle, the spindle and
arbor will move the mounted brake drum to the left. The
spindle feed rate can be adjusted by using the spindle
variable speed dial. Adjust the feed rate depending on the
surface finish you desire. Fast for rough cuts and slower for
finish cuts.
REMEMBER!
Spindle feed must be adjusted
with the lathe running only. Do not try to adjust speed dial
without the drive motor running or gear damage will occur.
20. After the first cut is made, repeat steps 14 - 19 until a
smooth finish cut is made.
12